Introduction
Printed Circuit Boards (PCBs) are essential components in modern electronics, forming the backbone of devices ranging from smartphones to industrial control systems. Despite advancements in manufacturing processes, PCB defects can still occur, leading to malfunctions and product failures. In this article, we will explore common printed circuit board defects and how you can leverage cloud-based tools and services to identify and fix them efficiently.
Types of Printed Circuit Board Defects
1. Solder Bridges
Solder bridges are one of the most common PCB defects, occurring when excess solder inadvertently connects two or more pads or traces that should remain separate. This unintended connection can cause short circuits and disrupt the proper functioning of the PCB.
Causes of Solder Bridges
- Excessive solder paste application
- Improper solder mask alignment
- Incorrect reflow oven temperature profile
- Inadequate cleaning of flux residues
Detecting Solder Bridges in the Cloud
Cloud-based inspection systems, such as automated optical inspection (AOI) software, can help detect solder bridges quickly and accurately. These systems utilize machine learning algorithms to analyze high-resolution images of PCBs and identify defects based on predefined parameters.
Cloud-based AOI Software | Features | Benefits |
---|---|---|
PCBInspect.io | – Automated defect detection – Real-time reporting – Scalable cloud infrastructure |
– Reduced manual inspection time – Improved accuracy – Seamless integration with existing workflows |
CloudPCB Inspector | – AI-powered defect classification – Customizable inspection rules – Secure data storage and sharing |
– Minimized false positives – Adaptable to specific PCB designs – Enhanced collaboration among team members |
Fixing Solder Bridges
To fix solder bridges, you can use the following techniques:
- Solder wick: Apply a solder wick to the affected area and heat it with a soldering iron to absorb the excess solder.
- Solder sucker: Use a solder sucker to remove the excess solder by heating the bridge and quickly sucking up the molten solder.
- Rework station: For more precise control, use a rework station with a fine-tipped nozzle to remove the excess solder and resolder the affected components.
2. Pad Lifting
Pad lifting occurs when the copper pad on a PCB separates from the substrate material, causing a break in the electrical connection. This defect can lead to intermittent or complete failure of the affected component.
Causes of Pad Lifting
- Incorrect PCB design parameters (e.g., pad size, copper thickness)
- Excessive heat during soldering
- Mechanical stress during assembly or handling
- Contamination or poor adhesion between the pad and substrate
Detecting Pad Lifting in the Cloud
Cloud-based X-ray inspection (AXI) systems can help identify pad lifting defects that may not be visible to the naked eye. These systems use advanced algorithms to analyze X-ray images of PCBs and detect anomalies in the solder joints and component connections.
Cloud-based AXI Software | Features | Benefits |
---|---|---|
CloudAXI Pro | – Automated defect detection – 3D image reconstruction – Customizable inspection profiles |
– Improved defect coverage – Enhanced visualization of hidden defects – Reduced false calls and escapes |
PCB X-Ray Inspect | – AI-assisted defect classification – Secure cloud storage and sharing – Seamless integration with MES systems |
– Increased inspection speed and accuracy – Collaborative defect analysis and reporting – Streamlined quality control processes |
Fixing Pad Lifting
To repair pad lifting defects, follow these steps:
- Clean the affected area: Remove any debris or contamination from the lifted pad and surrounding area using a solvent and brush.
- Reattach the pad: Apply a small amount of solder paste or conductive epoxy to the lifted pad and carefully position it back onto the substrate.
- Secure the pad: Use a hot air rework station or soldering iron to heat the pad and surrounding area, allowing the solder or epoxy to flow and form a secure bond.
- Inspect and test: Visually inspect the repaired pad and perform necessary electrical tests to ensure proper functionality.
3. Open Circuits
Open circuits occur when there is a break in the conductive path on a PCB, preventing current from flowing through the intended route. This defect can be caused by incomplete etching, damage to traces, or improper component placement.
Causes of Open Circuits
- Incorrect PCB design (e.g., trace width, spacing)
- Manufacturing process issues (e.g., etching, plating)
- Physical damage to traces or components
- Improper component placement or soldering
Detecting Open Circuits in the Cloud
Cloud-based in-circuit testing (ICT) platforms can help identify open circuits by verifying the continuity and resistance of PCB traces and components. These systems utilize a combination of electrical tests and cloud-based data analysis to pinpoint the location and nature of open circuit defects.
Cloud-based ICT Platform | Features | Benefits |
---|---|---|
CloudICT Suite | – Automated test program generation – Real-time data analysis and reporting – Scalable cloud infrastructure |
– Reduced test development time – Improved test coverage and accuracy – Seamless integration with existing manufacturing processes |
PCBTest.io | – AI-driven test optimization – Secure data storage and sharing – Customizable test parameters and limits |
– Minimized false failures and retests – Enhanced collaboration among team members – Adaptable to specific PCB designs and requirements |
Fixing Open Circuits
To repair open circuits, consider the following methods:
- Jumper wire: For small breaks in traces, use a jumper wire to bridge the gap and restore electrical continuity.
- Conductive ink or paint: Apply a conductive ink or paint to the damaged trace, allowing it to dry and form a conductive path.
- Trace repair kit: Use a specialized trace repair kit, which typically includes a conductive adhesive and copper tape, to mend the broken trace.
- PCB rework: In cases of severe damage or multiple open circuits, consider reworking the affected area of the PCB by removing and replacing the damaged traces and components.
Frequently Asked Questions (FAQ)
1. What are the benefits of using cloud-based tools for PCB defect detection and repair?
Cloud-based tools offer several advantages for PCB defect detection and repair, including:
- Scalability: Cloud infrastructure allows for the processing of large volumes of PCB data and images, enabling faster and more efficient defect detection.
- Accessibility: Cloud-based tools can be accessed from anywhere with an internet connection, facilitating collaboration among team members and reducing the need for specialized on-site equipment.
- Cost-effectiveness: By leveraging cloud resources, companies can reduce the upfront costs associated with purchasing and maintaining expensive inspection and testing equipment.
- Continuous improvement: Cloud-based tools can be updated and enhanced regularly, ensuring access to the latest features and algorithms for defect detection and analysis.
2. How do cloud-based inspection systems handle data security and privacy?
Cloud-based inspection systems prioritize data security and privacy through various measures, such as:
- Encryption: Data is encrypted both in transit and at rest, ensuring that sensitive information remains protected from unauthorized access.
- Access control: Strict access control mechanisms, such as multi-factor authentication and role-based permissions, are implemented to limit data access to authorized users only.
- Compliance: Cloud service providers adhere to industry-standard security and privacy regulations, such as ISO 27001, SOC 2, and GDPR, to maintain the highest levels of data protection.
- Regular audits: Third-party security audits are conducted periodically to identify and address any potential vulnerabilities or risks in the cloud infrastructure.
3. Can cloud-based tools be integrated with existing PCB manufacturing workflows?
Yes, most cloud-based PCB inspection and testing tools are designed to integrate seamlessly with existing manufacturing workflows. These tools often provide APIs (Application Programming Interfaces) and connectors that allow for easy integration with popular manufacturing execution systems (MES), enterprise resource planning (ERP) software, and other related tools. This integration enables the smooth exchange of data between systems, streamlining the overall PCB manufacturing process and facilitating data-driven decision-making.
4. How do I choose the right cloud-based PCB defect detection and repair tool for my organization?
When selecting a cloud-based PCB defect detection and repair tool, consider the following factors:
- Compatibility: Ensure that the tool is compatible with your organization’s existing PCB design and manufacturing processes, as well as any other software or systems in use.
- Scalability: Choose a tool that can scale to accommodate your organization’s current and future needs, taking into account factors such as PCB complexity, production volume, and data storage requirements.
- User-friendliness: Opt for a tool with a user-friendly interface and intuitive workflows to minimize the learning curve for your team and ensure efficient adoption.
- Support and training: Look for a provider that offers comprehensive support and training resources to help your team effectively implement and utilize the tool.
- Cost: Consider the total cost of ownership, including subscription fees, implementation costs, and any additional expenses related to training and support.
5. What is the future outlook for cloud-based PCB defect detection and repair?
The future of cloud-based PCB defect detection and repair looks promising, with several key developments on the horizon:
- Artificial Intelligence (AI) and Machine Learning (ML): Advancements in AI and ML technologies will enable more accurate and efficient defect detection, classification, and root cause analysis.
- Internet of Things (IoT): The integration of IoT devices and sensors into PCB manufacturing processes will allow for real-time monitoring and data collection, facilitating proactive defect detection and predictive maintenance.
- Digital twins: The creation of digital twins, which are virtual replicas of physical PCBs, will enable simulations and optimizations to be performed in the cloud, reducing the need for physical prototypes and accelerating the design and testing process.
- Augmented Reality (AR) and Virtual Reality (VR): The use of AR and VR technologies will enhance the visualization and interaction with PCBs in the cloud, enabling more immersive and intuitive defect analysis and repair processes.
As these technologies continue to evolve and mature, cloud-based PCB defect detection and repair tools will become increasingly sophisticated, enabling organizations to improve product quality, reduce costs, and accelerate time-to-market.
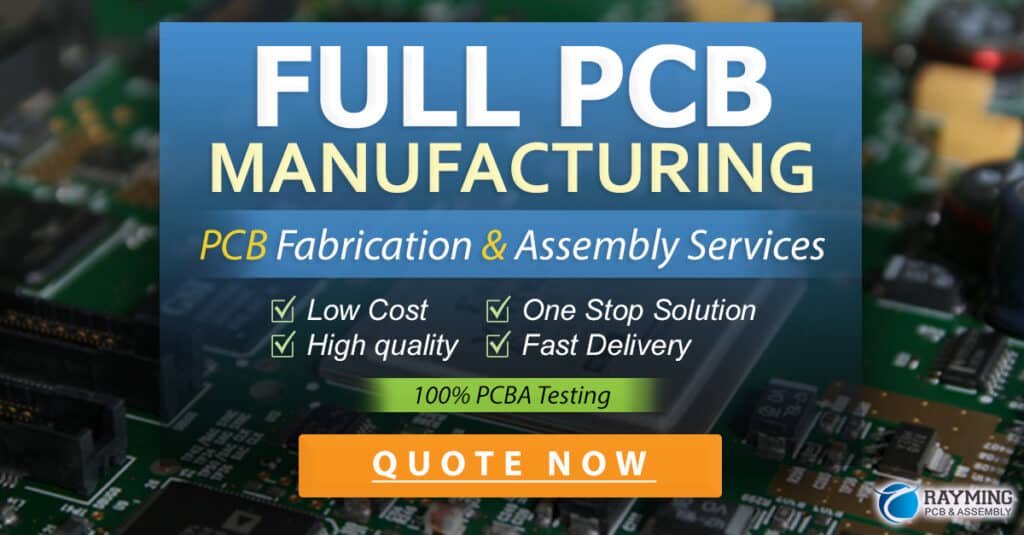
Conclusion
Printed circuit board defects can have a significant impact on the quality and reliability of electronic devices. By leveraging cloud-based tools and services, organizations can streamline the defect detection and repair process, improving efficiency and reducing costs. From automated optical inspection to in-circuit testing, cloud-based solutions offer a range of benefits, including scalability, accessibility, and continuous improvement.
As the electronics industry continues to evolve, embracing cloud-based PCB defect detection and repair will be crucial for organizations looking to stay competitive and deliver high-quality products to their customers. By understanding the common types of PCB defects, their causes, and the available cloud-based tools for addressing them, organizations can make informed decisions and implement effective strategies for optimizing their PCB manufacturing processes.
Leave a Reply