Introduction to PCB Reference Planes
In the world of printed circuit board (PCB) design, reference planes play a crucial role in ensuring signal integrity and reducing electromagnetic interference (EMI). PCB reference planes, also known as power planes or ground planes, are large copper areas that provide a low-impedance return path for high-speed signals. These planes help maintain a stable reference voltage and minimize the loop area between the signal trace and its return path, reducing inductance and EMI.
When designing multilayer PCBs, engineers often face the challenge of managing multiple reference planes and determining the optimal way to route signals across different layers. Changing reference planes during routing can have a significant impact on signal integrity, crosstalk, and EMI. In this article, we will explore the concepts behind PCB reference planes, the challenges associated with changing reference planes during routing, and best practices for maintaining signal integrity in multilayer boards.
The Role of Reference Planes in PCB Design
Power and Ground Planes
In a typical multilayer PCB, reference planes are dedicated to power and ground. These planes serve as low-impedance sources of power and provide a stable reference voltage for the signals traveling on the signal layers. By using large copper areas, the power and ground planes minimize the resistance and inductance of the power distribution network (PDN), ensuring a clean and stable power supply to the components on the board.
Signal Return Paths
In addition to providing a stable power source, reference planes also serve as return paths for high-speed signals. When a signal travels along a trace on a signal layer, it induces a corresponding return current on the adjacent reference plane. This return current follows the path of least impedance, which is typically directly underneath the signal trace.
By placing a reference plane close to the signal layer, the loop area between the signal trace and its return path is minimized, reducing the inductance and EMI associated with the signal. This close proximity also helps maintain the characteristic impedance of the trace, which is essential for preserving signal integrity.
Shielding and EMI Reduction
Reference planes also act as shields between different signal layers, reducing crosstalk and EMI. When a signal on one layer induces electromagnetic fields, the reference plane between the layers helps contain these fields and prevents them from interfering with signals on adjacent layers. This shielding effect is particularly important in high-speed designs where EMI can cause significant problems.
Challenges of Changing Reference Planes During Routing
Signal Integrity Issues
One of the primary challenges of changing reference planes during routing is maintaining signal integrity. When a signal transitions from one reference plane to another, it experiences a discontinuity in its return path. This discontinuity can cause reflections, ringing, and other signal integrity issues that can degrade the quality of the signal and lead to data corruption or system malfunctions.
The severity of these issues depends on several factors, including the frequency and rise time of the signal, the distance between the reference planes, and the design of the transition via. At high frequencies, even small discontinuities can have a significant impact on signal integrity.
Impedance Mismatch
Another challenge associated with changing reference planes is maintaining the characteristic impedance of the signal trace. The characteristic impedance of a trace is determined by its geometry and the properties of the dielectric material surrounding it. When a signal transitions between reference planes, the geometry of the trace and its surrounding environment changes, leading to an impedance mismatch.
If the impedance mismatch is significant, it can cause reflections and standing waves on the trace, degrading signal quality and increasing EMI. To minimize these issues, designers must carefully control the geometry of the transition via and ensure that the impedance of the trace remains consistent across the reference plane change.
Crosstalk and EMI
Changing reference planes during routing can also increase the risk of crosstalk and EMI. When a signal transitions between reference planes, it can radiate electromagnetic energy into the surrounding environment. This radiated energy can couple onto nearby traces, causing crosstalk and potentially disrupting the operation of other circuits on the board.
Additionally, the discontinuity in the return path can create a voltage difference between the two reference planes, leading to common-mode noise and EMI. This noise can propagate throughout the system and cause interference with other electronic devices.
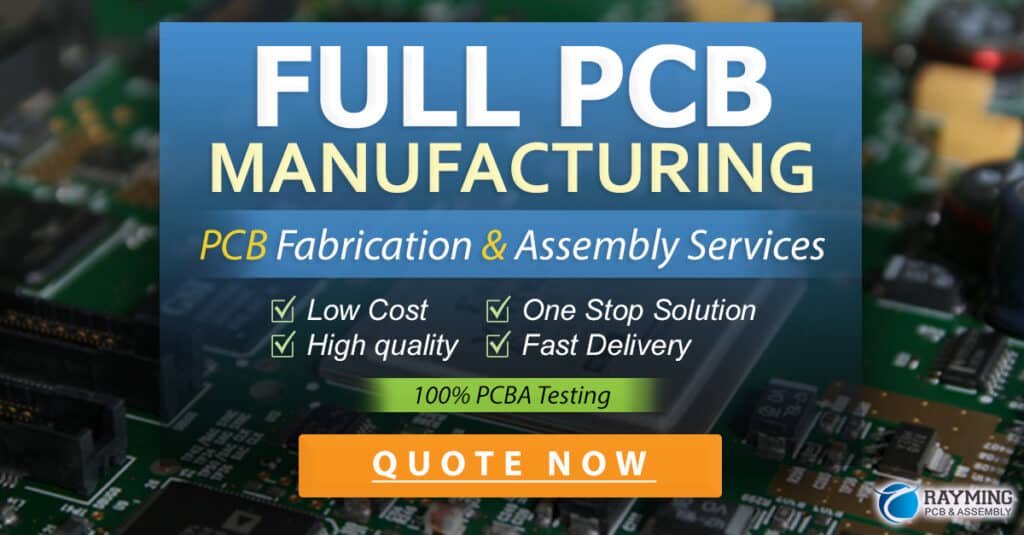
Best Practices for Changing Reference Planes
Minimize Reference Plane Changes
One of the most effective ways to mitigate the challenges associated with changing reference planes is to minimize the number of changes required. When possible, designers should route signals on a single reference plane, avoiding the need for plane changes altogether. This approach simplifies the routing process and reduces the risk of signal integrity issues and EMI.
When reference plane changes are unavoidable, designers should carefully plan the routing to minimize the number of changes required. By grouping signals with similar reference plane requirements and routing them together, designers can reduce the overall number of plane changes and simplify the routing process.
Use Stitching Vias
When a signal must transition between reference planes, designers can use stitching vias to minimize the discontinuity in the return path. Stitching vias are small vias that are placed adjacent to the signal via and connect the two reference planes together. These vias provide a low-impedance path for the return current, minimizing the impact of the reference plane change on signal integrity.
Stitching vias should be placed as close to the signal via as possible to minimize the loop area and inductance associated with the transition. The number and size of the stitching vias depend on the frequency and current requirements of the signal, as well as the available space on the board.
Control Via Geometry
The geometry of the transition via plays a critical role in maintaining signal integrity and minimizing impedance mismatch. Designers should carefully control the diameter and length of the via to ensure that its impedance matches the impedance of the trace on the signal layers.
In general, smaller via diameters and shorter via lengths help minimize the discontinuity in the return path and reduce the impact of the reference plane change on signal integrity. However, designers must also consider the manufacturing limitations and the current-carrying requirements of the via when selecting its geometry.
Use Ground Floods
Ground floods are large copper areas that are placed on the signal layers and connected to the reference planes through vias. These floods help minimize the impedance of the return path and reduce the impact of reference plane changes on signal integrity.
By placing ground floods near the transition vias and connecting them to the reference planes with multiple vias, designers can provide a low-impedance path for the return current and minimize the discontinuity in the return path. Ground floods also help reduce crosstalk and EMI by providing a larger area for the return current to flow.
Simulate and Test
Finally, designers should simulate and test their designs to verify the impact of reference plane changes on signal integrity and EMI. Modern PCB design software includes tools for simulating the behavior of signals as they transition between reference planes, allowing designers to identify potential issues before the board is manufactured.
Additionally, designers should perform thorough testing of the manufactured board to ensure that the reference plane changes do not cause signal integrity issues or EMI. This testing should include both frequency-domain and time-domain measurements to characterize the behavior of the signals and identify any potential problems.
Case Study: High-Speed Digital Design
To illustrate the importance of properly managing reference plane changes, let’s consider a case study involving a high-speed digital design. In this example, a designer is working on a multilayer PCB for a high-performance computing application. The board includes several high-speed digital interfaces, such as PCI Express and DDR4 memory, that must maintain signal integrity and minimize EMI.
The designer begins by carefully planning the layer stack-up and selecting appropriate materials for the PCB. They choose to use a 12-layer board with dedicated power and ground planes, as well as multiple signal layers for routing the high-speed interfaces.
Layer | Type | Material | Thickness (mil) |
---|---|---|---|
1 | Signal | FR-4 | 1.2 |
2 | Ground | Copper | 0.7 |
3 | Signal | FR-4 | 1.2 |
4 | Power | Copper | 0.7 |
5 | Signal | FR-4 | 1.2 |
6 | Ground | Copper | 0.7 |
7 | Signal | FR-4 | 1.2 |
8 | Power | Copper | 0.7 |
9 | Signal | FR-4 | 1.2 |
10 | Ground | Copper | 0.7 |
11 | Signal | FR-4 | 1.2 |
12 | Signal | FR-4 | 1.2 |
During the routing process, the designer encounters several situations where signals must transition between reference planes. For example, the PCI Express interface requires signals to transition from the ground plane on layer 2 to the power plane on layer 4 to maintain a continuous reference plane.
To minimize the impact of these reference plane changes, the designer follows best practices such as:
- Placing stitching vias adjacent to the signal vias to provide a low-impedance path for the return current.
- Carefully controlling the geometry of the transition vias to match the impedance of the signal traces.
- Using ground floods on the signal layers and connecting them to the reference planes with multiple vias.
The designer also simulates the behavior of the signals as they transition between reference planes using their PCB design software. The simulations help identify potential signal integrity issues and allow the designer to optimize the placement and geometry of the transition vias.
After the board is manufactured, the designer performs thorough testing to verify the signal integrity and EMI performance of the high-speed interfaces. The testing includes time-domain reflectometry (TDR) measurements to characterize the impedance of the traces and identify any discontinuities in the return path.
Thanks to the careful planning and adherence to best practices, the high-speed digital interfaces on the board perform well, maintaining signal integrity and minimizing EMI. The success of this project demonstrates the importance of properly managing reference plane changes in high-speed PCB designs.
FAQ
-
What are PCB reference planes, and why are they important?
PCB reference planes, also known as power or ground planes, are large copper areas that provide a low-impedance return path for high-speed signals. They help maintain a stable reference voltage, minimize the loop area between the signal trace and its return path, and reduce inductance and EMI. -
What challenges can arise when changing reference planes during routing?
Changing reference planes during routing can lead to signal integrity issues, impedance mismatch, crosstalk, and EMI. These problems arise due to discontinuities in the return path, changes in trace geometry, and the radiation of electromagnetic energy into the surrounding environment. -
How can designers minimize the impact of reference plane changes on signal integrity?
Designers can minimize the impact of reference plane changes by using stitching vias, controlling via geometry, using ground floods, and minimizing the number of plane changes required. Stitching vias provide a low-impedance path for the return current, while controlling via geometry helps maintain the impedance of the trace. Ground floods minimize the impedance of the return path and reduce the impact of plane changes on signal integrity. -
What role do simulations and testing play in managing reference plane changes?
Simulations and testing are essential for verifying the impact of reference plane changes on signal integrity and EMI. PCB design software includes tools for simulating the behavior of signals as they transition between reference planes, allowing designers to identify potential issues before the board is manufactured. Thorough testing of the manufactured board, including frequency-domain and time-domain measurements, helps ensure that the reference plane changes do not cause signal integrity issues or EMI. -
Can you provide an example of a situation where changing reference planes is necessary?
One example of a situation where changing reference planes is necessary is in high-speed digital designs, such as those involving PCI Express or DDR4 memory interfaces. In these cases, signals may need to transition from a ground plane to a power plane to maintain a continuous reference plane. Proper management of these reference plane changes is critical for maintaining signal integrity and minimizing EMI in these high-performance applications.
Conclusion
Changing reference planes during routing in multilayer PCBs is a complex challenge that requires careful planning and adherence to best practices. Reference planes play a crucial role in maintaining signal integrity, minimizing EMI, and providing a stable power distribution network. However, when signals must transition between reference planes, designers must contend with issues such as signal integrity degradation, impedance mismatch, crosstalk, and EMI.
To mitigate these challenges, designers should follow best practices such as minimizing the number of reference plane changes, using stitching vias, controlling via geometry, and using ground floods. Simulations and thorough testing are also essential for verifying the impact of reference plane changes on signal integrity and EMI.
By understanding the principles behind PCB reference planes and the challenges associated with changing them during routing, designers can create high-performance, reliable PCBs for a wide range of applications. As the demand for faster, more complex electronic systems continues to grow, the ability to effectively manage reference plane changes will remain a critical skill for PCB designers.
Leave a Reply