Introduction to DC-DC Buck Regulators
A DC-DC buck regulator, also known as a step-down converter, is a power supply circuit that efficiently converts a higher DC voltage to a lower DC voltage. It is widely used in various electronic applications, such as battery-powered devices, mobile phones, laptops, and embedded systems, where a stable and lower voltage is required from a higher voltage source.
In this article, we will explore the fundamentals of DC-DC buck regulators, their working principle, design considerations, and a step-by-step guide to building a DC-DC buck regulator as a student project.
Key Components of a DC-DC Buck Regulator
A typical DC-DC buck regulator consists of the following key components:
- Power MOSFET: Acts as a switch to control the current flow through the inductor.
- Inductor: Stores energy in its magnetic field and smooths the output current.
- Diode: Provides a path for the inductor current when the MOSFET is off.
- Output Capacitor: Smooths the output voltage and reduces ripple.
- PWM Controller: Generates the PWM signal to control the MOSFET switching.
Working Principle of a DC-DC Buck Regulator
The working principle of a DC-DC buck regulator can be summarized in two phases:
- ON Phase: When the MOSFET is turned on, the input voltage is applied across the inductor, causing the inductor current to increase linearly. The diode is reverse-biased during this phase.
- OFF Phase: When the MOSFET is turned off, the inductor current continues to flow through the diode, and the energy stored in the inductor is transferred to the output capacitor and load. The inductor current decreases linearly during this phase.
By controlling the duty cycle of the PWM signal, the average output voltage can be regulated to the desired value.
Designing a DC-DC Buck Regulator
Step 1: Determine the Specifications
Before designing a DC-DC buck regulator, you need to determine the following specifications:
- Input Voltage Range (Vin)
- Output Voltage (Vout)
- Maximum Output Current (Iout(max))
- Switching Frequency (fs)
- Output Voltage Ripple (ΔVout)
Step 2: Calculate the Duty Cycle
The duty cycle (D) of the PWM signal can be calculated using the following formula:
D = Vout / Vin
Step 3: Select the Inductor
The inductor value (L) can be calculated using the following formula:
L = (Vin – Vout) × D / (fs × ΔIL)
Where ΔIL is the inductor current ripple, typically chosen as 20-40% of the maximum output current.
Step 4: Select the Output Capacitor
The output capacitor value (Cout) can be calculated using the following formula:
Cout = ΔIL / (8 × fs × ΔVout)
Step 5: Select the Power MOSFET and Diode
The power MOSFET and diode should be selected based on their current and voltage ratings. The MOSFET should have a low on-resistance (RDS(on)) to minimize conduction losses, and the diode should have a fast recovery time to minimize switching losses.
Building a DC-DC Buck Regulator
Required Components
- Power MOSFET (e.g., IRF540N)
- Schottky Diode (e.g., 1N5819)
- Inductor (calculated value)
- Output Capacitor (calculated value)
- PWM Controller (e.g., LM2596)
- Input Capacitor (e.g., 100µF)
- Resistors and Capacitors for the feedback network
- PCB or breadboard
- Wires and connectors
Step-by-Step Assembly
- Design the PCB layout or set up the breadboard according to the schematic.
- Solder or place the components on the PCB or breadboard.
- Connect the input capacitor between the input voltage source and ground.
- Connect the power MOSFET, inductor, and diode according to the schematic.
- Connect the output capacitor between the output voltage and ground.
- Set up the feedback network using resistors and capacitors according to the PWM controller datasheet.
- Connect the PWM controller to the MOSFET gate and feedback network.
- Double-check all connections and component orientations.
Testing and Verification
- Apply the input voltage to the circuit, starting with a low voltage and gradually increasing it to the desired value.
- Measure the output voltage using a multimeter and verify that it matches the designed value.
- Observe the output voltage ripple using an oscilloscope and ensure it is within the acceptable range.
- Test the circuit under different load conditions and verify that the output voltage remains stable.
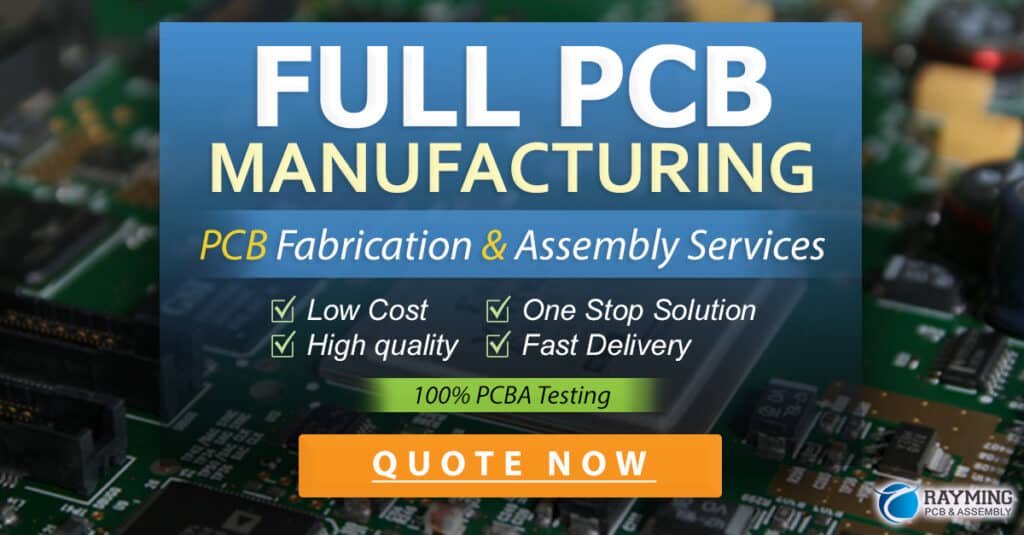
Troubleshooting Common Issues
- No Output Voltage:
- Check the input voltage and ensure it is within the specified range.
- Verify that all connections are secure and components are properly soldered.
-
Check the MOSFET and diode for any damage or incorrect orientation.
-
High Output Voltage Ripple:
- Increase the inductor value or switching frequency to reduce the inductor current ripple.
- Increase the output capacitor value to improve output voltage filtering.
-
Check for any damaged or leaky capacitors.
-
Overheating Components:
- Verify that the MOSFET and diode are properly sized for the current requirements.
- Ensure adequate heat dissipation by using heatsinks or improving airflow.
- Check for any short circuits or excessive current draw from the load.
Advanced Topics and Optimization
- Synchronous Rectification: Replace the diode with a second MOSFET to improve efficiency by reducing conduction losses.
- Soft-Start Circuit: Implement a soft-start circuit to limit inrush current during startup and protect components.
- Current Sensing and Protection: Add current sensing and protection features to prevent overcurrent conditions and ensure safe operation.
- Feedback Loop Compensation: Optimize the feedback loop compensation to improve transient response and stability.
- Efficiency Optimization: Minimize conduction and switching losses by selecting appropriate components and optimizing the PCB layout.
Conclusion
Building a DC-DC buck regulator is an excellent student project that provides hands-on experience in power electronics and circuit design. By understanding the working principle, design considerations, and following the step-by-step assembly guide, students can successfully build and test a functional DC-DC buck regulator.
This project not only reinforces theoretical concepts but also develops practical skills in component selection, PCB design, and troubleshooting. With further exploration of advanced topics and optimization techniques, students can enhance their understanding of power conversion and prepare themselves for future projects in the field of power electronics.
Frequently Asked Questions (FAQ)
-
What is the purpose of a DC-DC buck regulator?
A DC-DC buck regulator is used to efficiently step down a higher DC voltage to a lower DC voltage while maintaining a stable output. It is commonly used in battery-powered devices, embedded systems, and other applications where a lower voltage is required from a higher voltage source. -
What are the key components of a DC-DC buck regulator?
The key components of a DC-DC buck regulator include a power MOSFET, inductor, diode, output capacitor, and PWM controller. The MOSFET acts as a switch, the inductor stores energy, the diode provides a path for inductor current, the output capacitor filters the output voltage, and the PWM controller generates the control signal. -
How do I select the appropriate inductor value for my DC-DC buck regulator?
The inductor value can be calculated using the formula: L = (Vin – Vout) × D / (fs × ΔIL), where Vin is the input voltage, Vout is the output voltage, D is the duty cycle, fs is the switching frequency, and ΔIL is the inductor current ripple (typically 20-40% of the maximum output current). -
What should I do if my DC-DC buck regulator has no output voltage?
If your DC-DC buck regulator has no output voltage, first check the input voltage and ensure it is within the specified range. Then, verify that all connections are secure and components are properly soldered. Also, check the MOSFET and diode for any damage or incorrect orientation. If the issue persists, seek assistance from your instructor or a knowledgeable person. -
How can I optimize the efficiency of my DC-DC buck regulator?
To optimize the efficiency of your DC-DC buck regulator, you can consider the following techniques: select components with low conduction and switching losses, use synchronous rectification by replacing the diode with a second MOSFET, optimize the PCB layout to minimize parasitic inductance and resistance, and implement advanced control techniques such as zero-voltage switching (ZVS) or zero-current switching (ZCS).
Component | Purpose |
---|---|
Power MOSFET | Acts as a switch to control the current flow through the inductor |
Inductor | Stores energy in its magnetic field and smooths the output current |
Diode | Provides a path for the inductor current when the MOSFET is off |
Output Capacitor | Smooths the output voltage and reduces ripple |
PWM Controller | Generates the PWM signal to control the MOSFET switching |
Parameter | Symbol | Formula |
---|---|---|
Duty Cycle | D | D = Vout / Vin |
Inductor Value | L | L = (Vin – Vout) × D / (fs × ΔIL) |
Output Capacitor Value | Cout | Cout = ΔIL / (8 × fs × ΔVout) |
Leave a Reply