Introduction to BOM Planning
Bill of Materials (BOM) planning is a critical process in manufacturing that involves determining the components, materials, and quantities needed to produce a finished product. It is an essential part of production planning and helps ensure that the right materials are available at the right time and in the right quantities to meet production demands.
BOM planning can be done at different levels of production, depending on the complexity of the product and the manufacturing process. The three main levels of BOM planning are:
- Single-level BOM planning
- Multi-level BOM planning
- Modular BOM planning
Single-Level BOM Planning
Single-level BOM planning is the simplest form of BOM planning and is used for products that have a flat structure, meaning that all components are directly used in the finished product. In this type of planning, the focus is on determining the quantities of each component needed to produce the finished product.
Steps in Single-Level BOM Planning
-
Identify the finished product: The first step in single-level BOM planning is to identify the finished product that needs to be produced.
-
List all components: Next, list all the components that are needed to produce the finished product. This includes raw materials, sub-assemblies, and any other items that are used in the production process.
-
Determine the quantities needed: For each component listed, determine the quantity needed to produce one unit of the finished product. This information is typically obtained from the product design or engineering specifications.
-
Calculate total quantities: Based on the production plan or sales forecast, calculate the total quantities of each component needed to meet the production demand.
Example of Single-Level BOM
Let’s consider an example of a simple wooden chair. The single-level BOM for the chair would look like this:
Component | Quantity per chair |
---|---|
Wooden legs | 4 |
Seat | 1 |
Backrest | 1 |
Screws | 12 |
Wood glue | 50 ml |
If the production plan calls for 100 chairs to be produced, the total quantities needed would be:
Component | Total Quantity |
---|---|
Wooden legs | 400 |
Seat | 100 |
Backrest | 100 |
Screws | 1200 |
Wood glue | 5000 ml |
Multi-Level BOM Planning
Multi-level BOM planning is used for products that have a more complex structure, with components that are used in sub-assemblies, which are then used in the finished product. In this type of planning, the focus is on determining the quantities of components needed at each level of the BOM.
Steps in Multi-Level BOM Planning
-
Identify the finished product: As with single-level BOM planning, the first step is to identify the finished product that needs to be produced.
-
Create a multi-level BOM: Break down the finished product into its sub-assemblies and components, creating a hierarchical structure that shows the relationships between the different levels.
-
Determine the quantities needed at each level: For each component and sub-assembly, determine the quantity needed to produce one unit of the next higher-level item. This information is obtained from the product design or engineering specifications.
-
Calculate total quantities: Based on the production plan or sales forecast, calculate the total quantities of each component and sub-assembly needed to meet the production demand.
Example of Multi-Level BOM
Let’s consider an example of a more complex product, such as a bicycle. The multi-level BOM for the bicycle would look like this:
- Bicycle (Level 0)
- Frame (Level 1)
- Top tube (Level 2)
- Down tube (Level 2)
- Seat tube (Level 2)
- Head tube (Level 2)
- Bottom bracket (Level 2)
- Fork (Level 1)
- Fork blades (Level 2)
- Fork steerer (Level 2)
- Wheels (Level 1)
- Front wheel (Level 2)
- Front rim (Level 3)
- Front spokes (Level 3)
- Front hub (Level 3)
- Rear wheel (Level 2)
- Rear rim (Level 3)
- Rear spokes (Level 3)
- Rear hub (Level 3)
- Drivetrain (Level 1)
- Crankset (Level 2)
- Bottom bracket (Level 2)
- Chain (Level 2)
- Cassette (Level 2)
- Derailleurs (Level 2)
- Brakes (Level 1)
- Brake levers (Level 2)
- Brake calipers (Level 2)
- Brake cables (Level 2)
- Handlebars (Level 1)
- Handlebar (Level 2)
- Stem (Level 2)
- Grips (Level 2)
- Seat (Level 1)
- Seat post (Level 2)
- Saddle (Level 2)
In this example, the bicycle is the finished product (Level 0), and it is composed of several sub-assemblies (Level 1), such as the frame, fork, wheels, drivetrain, brakes, handlebars, and seat. Each sub-assembly is further broken down into its components (Level 2 and Level 3).
To calculate the total quantities needed for production, the quantities of each component and sub-assembly would be determined based on the number of bicycles to be produced.
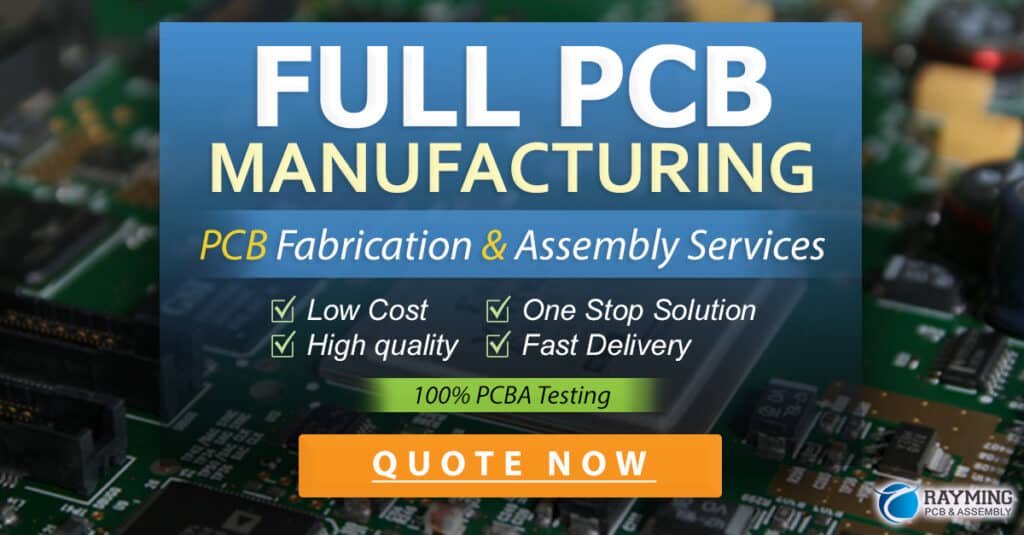
Modular BOM Planning
Modular BOM planning is used for products that have a modular design, where different configurations can be created by combining various modules or options. In this type of planning, the focus is on determining the quantities of each module needed to meet the demand for different product configurations.
Steps in Modular BOM Planning
-
Identify the base product and modules: The first step in modular BOM planning is to identify the base product and the various modules or options that can be added to create different configurations.
-
Create a modular BOM: Develop a BOM that shows the base product and the relationships between the different modules and options.
-
Determine the quantities needed for each module: Based on the forecasted demand for each product configuration, determine the quantities of each module needed to meet the demand.
-
Calculate total quantities: Aggregate the quantities of each module needed across all product configurations to determine the total quantities required for production.
Example of Modular BOM
Let’s consider an example of a modular desk system. The base product is a simple desk, and customers can choose from various modules to customize their desk, such as drawers, shelves, and keyboard trays.
The modular BOM for the desk system would look like this:
- Desk (Base Product)
- Tabletop (Required)
- Legs (Required)
- Modules
- Drawer Unit (Optional)
- Drawer box
- Drawer slides
- Drawer front
- Handles
- Shelf Unit (Optional)
- Shelf
- Shelf brackets
- Keyboard Tray (Optional)
- Tray
- Tray slides
In this example, the desk is the base product, and it requires a tabletop and legs. The modules, such as the drawer unit, shelf unit, and keyboard tray, are optional and can be added to the base product to create different configurations.
To calculate the total quantities needed for production, the forecasted demand for each product configuration would be used to determine the quantities of the base product and each module required.
Importance of Accurate BOM Planning
Accurate BOM planning is essential for several reasons:
-
Ensures material availability: By accurately planning the quantities of components and materials needed, manufacturers can ensure that they have the necessary items available when needed for production, reducing the risk of stockouts or production delays.
-
Reduces inventory costs: Accurate BOM planning helps manufacturers maintain optimal inventory levels, minimizing the cost of holding excess inventory and reducing the risk of obsolescence.
-
Improves production efficiency: With accurate BOM planning, manufacturers can schedule production activities more effectively, reducing the need for last-minute changes or rush orders.
-
Enhances customer satisfaction: By ensuring that the necessary materials are available and production is running smoothly, manufacturers can deliver products to customers on time, improving customer satisfaction and loyalty.
Challenges in BOM Planning
Despite its importance, BOM planning can present several challenges for manufacturers:
-
Complex product structures: Products with complex, multi-level BOMs can be challenging to plan, as the relationships between components and sub-assemblies must be accurately captured and maintained.
-
Changing product designs: As products evolve and new versions are released, BOMs must be updated to reflect the changes, which can be time-consuming and prone to errors.
-
Inaccurate or incomplete data: BOM planning relies on accurate data about components, quantities, and lead times. If this data is inaccurate or incomplete, it can lead to incorrect planning and production issues.
-
Integration with other systems: BOM planning must be integrated with other systems, such as inventory management and production scheduling, to ensure that the entire manufacturing process runs smoothly. This integration can be complex and require significant resources.
Best Practices for Effective BOM Planning
To overcome these challenges and ensure effective BOM planning, manufacturers should follow these best practices:
-
Maintain accurate and up-to-date BOMs: Regularly review and update BOMs to ensure that they accurately reflect the current product design and components.
-
Use a centralized BOM management system: Implement a centralized system for managing BOMs, such as a Product Lifecycle Management (PLM) or Enterprise Resource Planning (ERP) system, to ensure that all stakeholders have access to the most current and accurate BOM data.
-
Collaborate across departments: Foster collaboration between engineering, purchasing, and production teams to ensure that BOM planning is aligned with product design, material availability, and production capacity.
-
Leverage automation: Use automated tools and systems to streamline BOM planning processes, reduce manual errors, and improve efficiency.
-
Continuously monitor and improve: Regularly monitor BOM planning performance and identify opportunities for improvement, such as reducing lead times, optimizing inventory levels, or improving data accuracy.
Conclusion
BOM planning is a critical process in manufacturing that helps ensure the right materials are available at the right time and in the right quantities to meet production demands. By understanding the different levels of BOM planning and following best practices for effective BOM management, manufacturers can improve production efficiency, reduce costs, and enhance customer satisfaction.
As products continue to become more complex and customer demands evolve, the importance of accurate and efficient BOM planning will only continue to grow. Manufacturers that prioritize BOM planning and invest in the necessary tools and processes will be well-positioned to succeed in today’s competitive market.
Frequently Asked Questions (FAQ)
1. What is the difference between a single-level and multi-level BOM?
A single-level BOM is used for products with a flat structure, where all components are directly used in the finished product. A multi-level BOM, on the other hand, is used for products with a more complex structure, where components are used in sub-assemblies, which are then used in the finished product.
2. What is the purpose of modular BOM planning?
Modular BOM planning is used for products with a modular design, where different configurations can be created by combining various modules or options. The purpose of modular BOM planning is to determine the quantities of each module needed to meet the demand for different product configurations.
3. Why is accurate BOM planning important?
Accurate BOM planning is important because it ensures material availability, reduces inventory costs, improves production efficiency, and enhances customer satisfaction by ensuring that products are delivered on time.
4. What are some challenges in BOM planning?
Some challenges in BOM planning include complex product structures, changing product designs, inaccurate or incomplete data, and integration with other systems.
5. What are some best practices for effective BOM planning?
Best practices for effective BOM planning include maintaining accurate and up-to-date BOMs, using a centralized BOM management system, collaborating across departments, leveraging automation, and continuously monitoring and improving the BOM planning process.
Leave a Reply