Introduction to Vias in Printed Circuit Boards
Printed Circuit Boards (PCBs) are essential components in modern electronics. They provide a platform for mounting and connecting various electronic components, such as resistors, capacitors, and integrated circuits. One crucial aspect of PCB design is the use of vias, which are conductive pathways that allow electrical connections between different layers of the board. In this article, we will focus on two specific types of vias: blind vias and buried vias.
What Are Vias?
Before diving into blind and buried vias, let’s first understand what vias are in general. Vias are essentially holes drilled through the layers of a PCB, which are then plated with a conductive material, typically copper. They enable electrical signals to travel from one layer of the board to another, allowing for more complex circuit designs and efficient use of space.
There are several types of vias used in PCB design, including:
- Through-hole vias
- Blind vias
- Buried vias
- Micro vias
Each type of via serves a specific purpose and has its own advantages and limitations.
What Are Blind Vias?
Definition and Characteristics
Blind vias are a type of via that starts from either the top or bottom layer of a PCB and terminates at one of the inner layers, without passing through the entire board. In other words, they are “blind” because they are not visible from one of the outer surfaces of the PCB.
Key characteristics of blind vias include:
- They originate from either the top or bottom layer and end at an inner layer
- They do not pass through the entire thickness of the board
- They are used to connect outer layers to inner layers
Advantages of Using Blind Vias
Blind vias offer several advantages in PCB design:
-
Space savings: By using blind vias, designers can create more compact layouts, as they do not require additional space on the opposite side of the board.
-
Improved signal integrity: Blind vias can help reduce the length of signal paths, which minimizes signal reflections and improves overall signal integrity.
-
Enhanced design flexibility: Blind vias allow for more creative and efficient routing of traces, as they can be placed in areas where through-hole vias may not be feasible.
Manufacturing Process
The manufacturing process for blind vias involves several steps:
-
Drilling: Holes are drilled partially through the PCB, starting from either the top or bottom layer and ending at a specific inner layer.
-
Plating: The drilled holes are then plated with a conductive material, usually copper, to create an electrical connection between the layers.
-
Filling: In some cases, the blind vias may be filled with a non-conductive material to improve the board’s structural integrity and prevent contamination.
What Are Buried Vias?
Definition and Characteristics
Buried vias are another type of via that are used to connect inner layers of a PCB without extending to the outer layers. They are “buried” within the board and are not visible from either the top or bottom surface.
Key characteristics of buried vias include:
- They are used to connect inner layers of a PCB
- They do not extend to the outer layers (top or bottom)
- They are completely hidden within the board
Advantages of Using Buried Vias
Buried vias provide several benefits in PCB design:
-
Increased routing density: By using buried vias, designers can create more dense and complex routing patterns on the inner layers of the board, without affecting the outer layers.
-
Improved signal integrity: Like blind vias, buried vias can help reduce signal path lengths and minimize signal reflections, leading to better signal integrity.
-
Enhanced protection: Since buried vias are completely enclosed within the board, they are protected from external factors such as moisture, dust, and mechanical stress.
Manufacturing Process
The manufacturing process for buried vias is more complex than that of blind vias:
-
Layer stacking: Multiple PCB layers are fabricated separately, with each layer containing the necessary buried via holes.
-
Plating: The buried via holes are plated with a conductive material to establish electrical connections between the layers.
-
Lamination: The individual layers are then laminated together under high pressure and temperature to form a single, solid board.
-
Drilling and plating: After lamination, additional drilling and plating processes may be performed to create other types of vias or to add surface components.
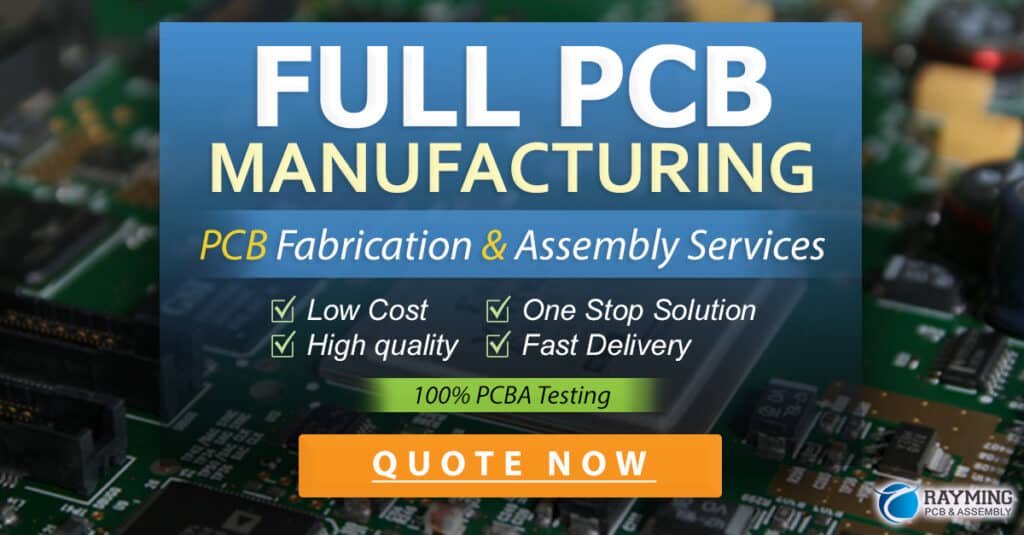
Applications of Blind and Buried Vias
High-Density Interconnect (HDI) PCBs
One of the primary applications of blind and buried vias is in the design and manufacture of High-Density Interconnect (HDI) PCBs. HDI PCBs are characterized by their high component density, fine pitch, and complex routing requirements. By using blind and buried vias, designers can create highly compact and efficient layouts that meet the demands of modern electronic devices.
HDI PCBs are commonly used in:
- Smartphones and tablets
- Wearable electronics
- Medical devices
- Aerospace and defense systems
Multilayer PCBs
Blind and buried vias are also essential in the design of multilayer PCBs, which consist of three or more conductive layers. As the number of layers increases, the use of blind and buried vias becomes increasingly important for maintaining signal integrity and routing efficiency.
Multilayer PCBs with blind and buried vias are used in a wide range of applications, such as:
- Computer motherboards
- Telecommunications equipment
- Automotive electronics
- Industrial control systems
RF and Microwave PCBs
In high-frequency applications, such as RF and microwave circuits, the use of blind and buried vias can help optimize signal paths and minimize signal loss. By carefully placing blind and buried vias in relation to the circuit components, designers can create PCBs that offer superior performance and reliability.
RF and microwave PCBs with blind and buried vias are used in:
- Wireless communication devices
- Radar systems
- Satellite communications
- High-speed data transmission networks
Design Considerations for Blind and Buried Vias
Via Size and Placement
When designing PCBs with blind and buried vias, it is crucial to consider the size and placement of the vias. The via size should be selected based on the current-carrying requirements and the available space on the board. Smaller vias can help reduce the overall board size but may have lower current-carrying capacity and higher manufacturing costs.
Via placement is also critical, as it can affect signal integrity and manufacturing reliability. Designers should follow recommended design guidelines, such as minimum via-to-via spacing and via-to-trace spacing, to ensure optimal performance and manufacturability.
Layer Stackup and Via Span
The layer stackup and via span are other important factors to consider when using blind and buried vias. The layer stackup refers to the arrangement of conductive and insulating layers in the PCB, while the via span is the number of layers that a via connects.
Designers should carefully plan the layer stackup and via span to minimize the number of vias required and to ensure that the vias can be reliably manufactured. In general, shorter via spans are easier to manufacture and have better signal integrity, but they may require more layers and increase the overall board thickness.
Signal Integrity and Impedance Matching
Maintaining signal integrity and impedance matching is crucial in high-speed digital and RF circuits. Blind and buried vias can introduce discontinuities in the signal path, leading to reflections and signal degradation. To mitigate these issues, designers should use appropriate via geometries and placement, as well as impedance-matched via structures, such as differential vias or coaxial vias.
Simulation tools, such as electromagnetic field solvers, can help designers optimize via designs for signal integrity and impedance matching.
Manufacturing Considerations and Cost
The use of blind and buried vias can significantly impact the manufacturing process and cost of PCBs. Compared to through-hole vias, blind and buried vias require additional drilling, plating, and lamination steps, which can increase the overall manufacturing complexity and lead time.
Designers should work closely with their PCB fabrication partners to ensure that their designs are manufacturable and cost-effective. In some cases, alternative design approaches, such as using microvias or high-density interconnect (HDI) techniques, may be more suitable for a given application.
Best Practices for Designing with Blind and Buried Vias
To ensure successful designs with blind and buried vias, consider the following best practices:
-
Follow the design rules: Adhere to the recommended design rules provided by your PCB fabrication partner, including minimum via sizes, spacings, and layer spans.
-
Plan the layer stackup carefully: Optimize the layer stackup to minimize the number of vias required and to ensure manufacturability.
-
Use simulation tools: Employ simulation tools to analyze signal integrity, impedance matching, and thermal performance of your via designs.
-
Consider alternative technologies: Evaluate alternative technologies, such as microvias or HDI, which may offer better performance or cost-effectiveness for your specific application.
-
Communicate with your fabrication partner: Maintain open communication with your PCB fabrication partner throughout the design process to ensure that your design is manufacturable and to address any potential issues early on.
By following these best practices, designers can create reliable and high-performance PCBs that leverage the benefits of blind and buried vias.
Frequently Asked Questions (FAQ)
- What is the difference between blind and buried vias?
-
Blind vias start from either the top or bottom layer of a PCB and terminate at an inner layer, without passing through the entire board. Buried vias, on the other hand, connect inner layers of a PCB without extending to the outer layers.
-
What are the advantages of using blind and buried vias?
-
Blind and buried vias offer several advantages, including space savings, improved signal integrity, enhanced design flexibility, and increased routing density. They also provide protection for the vias, as they are not exposed on the outer layers of the board.
-
In what applications are blind and buried vias commonly used?
-
Blind and buried vias are commonly used in high-density interconnect (HDI) PCBs, multilayer PCBs, and RF and microwave PCBs. They are essential in applications that require compact layouts, complex routing, and high signal integrity, such as smartphones, medical devices, and aerospace systems.
-
How do blind and buried vias affect the manufacturing process and cost?
-
The use of blind and buried vias can increase the manufacturing complexity and cost compared to through-hole vias. They require additional drilling, plating, and lamination steps, which can lead to longer lead times and higher fabrication costs.
-
What are some best practices for designing with blind and buried vias?
- When designing with blind and buried vias, it is essential to follow the recommended design rules, carefully plan the layer stackup, use simulation tools to analyze signal integrity and impedance matching, consider alternative technologies, and maintain open communication with your PCB fabrication partner.
Conclusion
Blind and buried vias are essential components in modern PCB design, offering numerous benefits such as space savings, improved signal integrity, and enhanced design flexibility. They are widely used in various applications, including high-density interconnect (HDI) PCBs, multilayer PCBs, and RF and microwave circuits.
When designing with blind and buried vias, it is crucial to consider factors such as via size and placement, layer stackup and via span, signal integrity, and manufacturing considerations. By following best practices and working closely with PCB fabrication partners, designers can create reliable, high-performance PCBs that leverage the advantages of blind and buried vias.
As electronic devices continue to become more compact and complex, the use of blind and buried vias will remain an essential tool in the PCB designer’s toolkit, enabling the development of innovative and efficient solutions for a wide range of applications.
Leave a Reply