Introduction to Automotive Ethernet
Automotive Ethernet is a rapidly growing technology that is transforming the way vehicles communicate and exchange data. As the demand for connected cars and autonomous vehicles continues to rise, the need for reliable, high-speed, and secure in-vehicle networking solutions has become more pressing than ever. Automotive Ethernet has emerged as a promising solution to address these challenges, offering a range of benefits over traditional in-vehicle networking technologies.
Benefits of Automotive Ethernet
- High bandwidth: Automotive Ethernet can support data rates up to 10 Gbps, enabling the transmission of large amounts of data in real-time.
- Scalability: Ethernet networks can be easily scaled to accommodate the growing number of electronic control units (ECUs) and sensors in modern vehicles.
- Cost-effectiveness: Automotive Ethernet leverages existing Ethernet technologies, reducing development costs and time-to-market.
- Flexibility: Ethernet networks can be configured in various topologies, such as star, daisy-chain, or tree, to suit different vehicle architectures.
- Standardization: Automotive Ethernet is based on the IEEE 802.3 standard, ensuring interoperability between devices from different manufacturers.
Current Automotive Ethernet Standards
Several standards have been developed to address the specific requirements of automotive Ethernet networks. These standards define the physical layer, data link layer, and higher-layer protocols used in automotive Ethernet communication.
IEEE 802.3bw-2015 (100BASE-T1)
- Physical layer specification for 100 Mbps Ethernet over a single twisted pair cable
- Designed for automotive applications with a maximum cable length of 15 meters
- Supports full-duplex communication and power over data lines (PoDL)
IEEE 802.3bp-2016 (1000BASE-T1)
- Physical layer specification for 1 Gbps Ethernet over a single twisted pair cable
- Designed for automotive applications with a maximum cable length of 15 meters
- Supports full-duplex communication and power over data lines (PoDL)
IEEE 802.3ch-2020 (MultiGig Automotive Ethernet)
- Physical layer specification for 2.5, 5, and 10 Gbps Ethernet over a single twisted pair cable
- Designed for automotive applications with a maximum cable length of 15 meters
- Supports full-duplex communication and power over data lines (PoDL)
Automotive Ethernet Network Topologies
Automotive Ethernet networks can be configured in various topologies to suit different vehicle architectures and requirements. The choice of topology depends on factors such as the number of nodes, the required bandwidth, and the physical layout of the vehicle.
Star Topology
In a star topology, all nodes are connected to a central switch or hub. This topology offers high bandwidth and low latency, as each node has a dedicated link to the switch. However, it requires more cabling and can be more expensive to implement compared to other topologies.
Daisy-Chain Topology
In a daisy-chain topology, nodes are connected in a linear fashion, with each node having two ports: one for incoming data and one for outgoing data. This topology is simpler and more cost-effective than the star topology, as it requires less cabling. However, it has lower bandwidth and higher latency, as data must pass through multiple nodes before reaching its destination.
Tree Topology
A tree topology is a combination of star and daisy-chain topologies, where multiple star networks are connected through a backbone network. This topology offers a balance between the benefits of star and daisy-chain topologies, providing high bandwidth and scalability while minimizing cabling requirements.
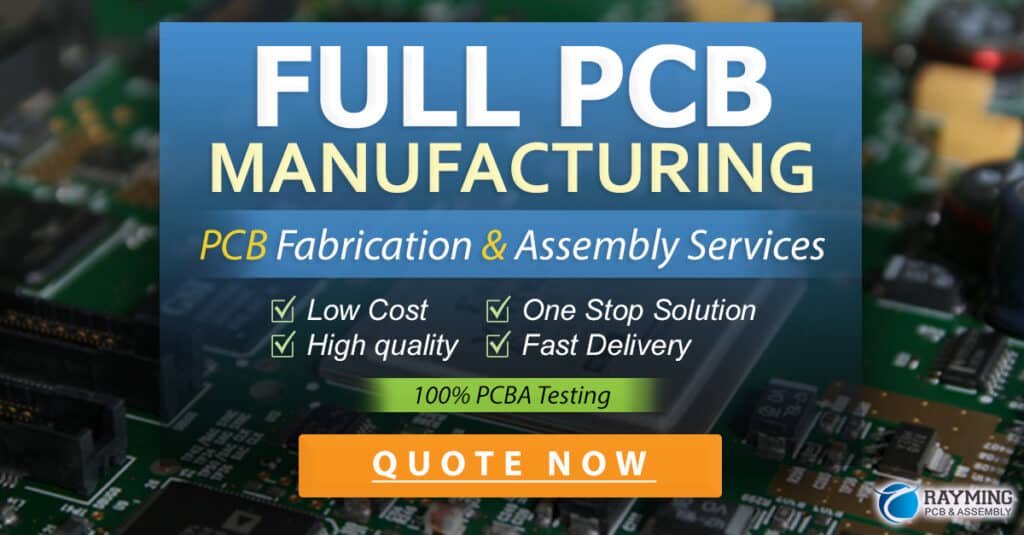
Automotive Ethernet Protocol Stack
The automotive Ethernet protocol stack consists of several layers that work together to enable reliable and secure communication between devices in a vehicle.
Physical Layer (PHY)
The physical layer is responsible for the transmission and reception of raw data over the physical medium, such as twisted pair cables. Automotive Ethernet PHYs are designed to operate in the harsh automotive environment, withstanding high temperatures, vibrations, and electromagnetic interference.
Data Link Layer (MAC)
The data link layer, also known as the Media Access Control (MAC) layer, is responsible for the reliable transfer of data between nodes on the network. It handles tasks such as framing, addressing, and error detection.
Network Layer (IP)
The network layer, typically implemented using the Internet Protocol (IP), is responsible for routing data packets between nodes on the network. In automotive Ethernet networks, IPv4 or IPv6 can be used depending on the specific requirements of the application.
Transport Layer (TCP/UDP)
The transport layer is responsible for end-to-end communication between applications running on different nodes. The two most common transport layer protocols used in automotive Ethernet are Transmission Control Protocol (TCP) and User Datagram Protocol (UDP). TCP provides reliable, connection-oriented communication, while UDP offers faster, connectionless communication.
Application Layer
The application layer consists of the various protocols and services that enable specific functionalities in the vehicle, such as diagnostics, over-the-air updates, and infotainment systems. Some common application layer protocols used in automotive Ethernet include:
- DoIP (Diagnostic over IP): Used for vehicle diagnostics and firmware updates
- SOME/IP (Scalable service-Oriented MiddlewarE over IP): Used for service discovery and communication between ECUs
- AVB/TSN (Audio Video Bridging/Time-Sensitive Networking): Used for real-time audio and video transmission
Future Trends and Challenges in Automotive Ethernet
As the automotive industry continues to evolve, several trends and challenges are shaping the future of automotive Ethernet:
Higher bandwidth requirements
With the increasing number of sensors, cameras, and infotainment systems in vehicles, the demand for higher bandwidth is growing. The adoption of MultiGig Automotive Ethernet standards, such as 2.5G, 5G, and 10G, will become more widespread to accommodate these requirements.
Time-Sensitive Networking (TSN)
TSN is a set of standards that enable deterministic, real-time communication over Ethernet networks. TSN is essential for safety-critical applications, such as autonomous driving and advanced driver assistance systems (ADAS), where low latency and high reliability are crucial.
Cybersecurity
As vehicles become more connected, the risk of cyber attacks increases. Automotive Ethernet networks must be designed with strong security measures, such as encryption, authentication, and intrusion detection, to protect against potential threats.
Interoperability
With the growing number of ECUs and sensors from different manufacturers, ensuring interoperability between devices is a significant challenge. The development and adoption of standardized protocols and interfaces will be essential to enable seamless communication and integration within automotive Ethernet networks.
Power over Data Lines (PoDL)
PoDL technology allows power to be transmitted over the same twisted pair cable used for data communication, reducing the need for separate power cables. This simplifies wiring harnesses and reduces overall system costs. The adoption of PoDL will become more widespread as automotive Ethernet networks continue to grow in complexity.
Conclusion
Automotive Ethernet is a crucial technology for the future of connected and autonomous vehicles, offering high bandwidth, scalability, and cost-effectiveness compared to traditional in-vehicle networking solutions. As the automotive industry continues to evolve, the design requirements for automotive Ethernet will become more stringent, driven by the need for higher bandwidth, real-time communication, and enhanced cybersecurity.
The adoption of advanced automotive Ethernet standards, such as MultiGig and TSN, will be essential to meet these requirements. Additionally, the development of standardized protocols and interfaces will be crucial to ensure interoperability between devices from different manufacturers.
As automotive Ethernet networks continue to grow in complexity, innovative solutions like Power over Data Lines (PoDL) will help simplify wiring harnesses and reduce overall system costs. However, the increasing connectivity of vehicles also brings new challenges, particularly in the area of cybersecurity. Automotive Ethernet networks must be designed with robust security measures to protect against potential cyber threats.
In conclusion, automotive Ethernet is a vital technology that will play a central role in shaping the future of the automotive industry. As the demand for connected and autonomous vehicles continues to rise, the design requirements for automotive Ethernet will evolve to meet the growing needs for high-speed, reliable, and secure in-vehicle communication.
Frequently Asked Questions (FAQ)
-
What is automotive Ethernet, and how does it differ from traditional Ethernet?
Automotive Ethernet is an adaptation of the standard Ethernet technology specifically designed for use in vehicles. While it is based on the same underlying principles as traditional Ethernet, automotive Ethernet has been optimized to meet the unique requirements of the automotive environment, such as high reliability, low latency, and resistance to harsh conditions like extreme temperatures and vibrations. -
What are the main benefits of using automotive Ethernet in vehicles?
Automotive Ethernet offers several key benefits, including high bandwidth (up to 10 Gbps), scalability to accommodate the growing number of electronic control units (ECUs) and sensors in modern vehicles, cost-effectiveness by leveraging existing Ethernet technologies, flexibility in network topology design, and standardization based on the IEEE 802.3 standard, which ensures interoperability between devices from different manufacturers. -
What are the current automotive Ethernet standards, and how do they differ?
The main automotive Ethernet standards are IEEE 802.3bw-2015 (100BASE-T1), IEEE 802.3bp-2016 (1000BASE-T1), and IEEE 802.3ch-2020 (MultiGig Automotive Ethernet). 100BASE-T1 and 1000BASE-T1 support data rates of 100 Mbps and 1 Gbps, respectively, over a single twisted pair cable. MultiGig Automotive Ethernet, introduced in 2020, supports data rates of 2.5, 5, and 10 Gbps over a single twisted pair cable. All these standards are designed for automotive applications with a maximum cable length of 15 meters and support full-duplex communication and power over data lines (PoDL). -
What are the most common network topologies used in automotive Ethernet networks?
The most common network topologies used in automotive Ethernet networks are star, daisy-chain, and tree. Star topology offers high bandwidth and low latency but requires more cabling. Daisy-chain topology is simpler and more cost-effective but has lower bandwidth and higher latency. Tree topology combines the benefits of star and daisy-chain topologies, providing a balance between bandwidth, scalability, and cabling requirements. -
What are the future trends and challenges in automotive Ethernet?
As the automotive industry evolves, several trends and challenges are shaping the future of automotive Ethernet. These include the need for higher bandwidth to accommodate the increasing number of sensors, cameras, and infotainment systems; the adoption of Time-Sensitive Networking (TSN) for deterministic, real-time communication in safety-critical applications; the growing importance of cybersecurity to protect against potential threats; the need for interoperability between devices from different manufacturers; and the widespread adoption of Power over Data Lines (PoDL) technology to simplify wiring harnesses and reduce overall system costs.
Leave a Reply