Table of Contents
- Introduction to Solderless Assembly
- Breadboards: The Foundation of Solderless Prototyping
- Jumper Wires and Header Pins
- Screw Terminals and Terminal Blocks
- Crimp Connectors and Wire Harnesses
- Conductive Adhesives and Pastes
- Solderless PCB Connectors
- Wire Wrapping Techniques
- Modular Electronics and Plug-and-Play Systems
- Troubleshooting and Best Practices
- Frequently Asked Questions (FAQ)
- Conclusion
Introduction to Solderless Assembly
Solderless assembly refers to the process of creating electrical connections between components without the use of solder. This approach offers several advantages, such as:
- Accessibility for beginners and those who may not have access to soldering equipment
- Faster prototyping and iteration, as connections can be easily made and modified
- Reduced risk of damage to sensitive components due to heat exposure
- Increased flexibility in circuit design and layout
In the following sections, we will explore various techniques and tools that enable successful solderless assembly, catering to a wide range of projects and skill levels.
Breadboards: The Foundation of Solderless Prototyping
Breadboards are an essential tool for solderless prototyping and are widely used by educators, students, and hobbyists. They provide a platform for quickly building and testing electronic circuits without the need for permanent connections.
How Breadboards Work
A typical breadboard consists of a plastic board with a grid of holes, each connected by metal clips underneath. These metal clips are arranged in a specific pattern, allowing components to be inserted and connected as desired.
Breadboard Section | Description |
---|---|
Power Rails | Typically located along the sides of the breadboard, these rails are used to distribute power (+) and ground (-) to the circuit. |
Terminal Strips | The main area of the breadboard, consisting of rows of interconnected holes. Each row is electrically isolated from the others. |
DIP Support | A central gap in the breadboard allows for the insertion of dual-inline package (DIP) chips, such as microcontrollers or integrated circuits. |
Breadboard Best Practices
When working with breadboards, keep the following tips in mind:
- Organize your components and wires to maintain a clean and readable layout.
- Use color-coded jumper wires to distinguish different parts of the circuit (e.g., power, ground, signals).
- Be mindful of the current limitations of breadboards, as they are not suitable for high-current applications.
- Double-check your connections before applying power to the circuit to avoid short circuits or unintended paths.
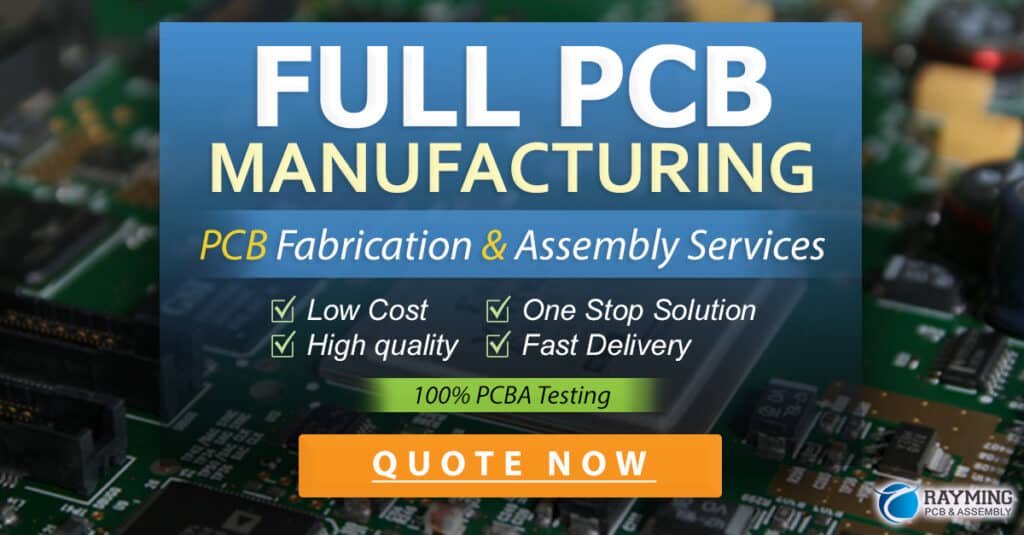
Jumper Wires and Header Pins
Jumper wires and header pins are essential components for making connections on breadboards and between different modules or boards.
Jumper Wires
Jumper wires are pre-cut, insulated wires with male or female connectors on either end. They come in various lengths and colors, making it easy to create custom connections and organize your circuit.
Jumper Wire Type | Description |
---|---|
Male-to-Male | Used for connecting two points on a breadboard or between header pins. |
Male-to-Female | Used for connecting a male header pin to a female connector or breadboard point. |
Female-to-Female | Used for connecting two female connectors or breadboard points. |
Header Pins
Header pins are small, conductive pins that can be soldered to PCBs or used with jumper wires for solderless connections. They provide a convenient way to interface between different modules or boards.
Header Pin Type | Description |
---|---|
Male Headers | Pins that protrude from a surface, typically soldered to a PCB. |
Female Headers | Sockets that accept male header pins, allowing for removable connections. |
Screw Terminals and Terminal Blocks
Screw terminals and terminal blocks offer a secure and reliable method for connecting wires without soldering. They are particularly useful for projects involving higher currents or when a more robust connection is required.
Screw Terminals
Screw terminals consist of a conductive block with one or more screws that tighten down onto the wire, creating a strong electrical and mechanical connection. They are available in various sizes and configurations to accommodate different wire gauges and numbers of connections.
Terminal Blocks
Terminal blocks are modular units that house multiple screw terminals in a single package. They provide a neat and organized way to manage multiple connections and are often used in industrial or high-reliability applications.
Terminal Block Type | Description |
---|---|
Barrier Strips | A basic terminal block with screw terminals arranged in a single row. |
Sectional Blocks | Modular terminal blocks that can be snapped together to create custom configurations. |
DIN Rail Mounts | Terminal blocks designed to be mounted on standard DIN rails for easy installation and maintenance. |
Crimp Connectors and Wire Harnesses
Crimp connectors and wire harnesses offer a solderless solution for creating custom cable assemblies and interconnects.
Crimp Connectors
Crimp connectors are specialized terminals that are attached to the end of a wire using a crimping tool. The crimping process deforms the connector around the wire, creating a secure electrical and mechanical connection.
Crimp Connector Type | Description |
---|---|
Spade Terminals | U-shaped terminals that are crimped onto the end of a wire and secured under a screw or bolt. |
Ring Terminals | Circular terminals with a hole in the center, used for secure connections to screw terminals or posts. |
Butt Connectors | Cylindrical connectors used for joining two wires end-to-end. |
Quick Disconnects | Connectors with a male tab and female receptacle, allowing for easy connection and disconnection. |
Wire Harnesses
Wire harnesses are pre-assembled cable assemblies that use crimp connectors and other components to create custom interconnects between different parts of a system. They offer a organized and efficient solution for managing complex wiring in larger projects.
Conductive Adhesives and Pastes
Conductive adhesives and pastes provide a solderless method for attaching components to circuits or creating conductive traces on various surfaces.
Conductive Adhesives
Conductive adhesives are specialized glues that contain conductive particles, such as silver or carbon, which allow electrical current to flow through the bond. They can be used to attach components to PCBs or other surfaces without the need for soldering.
Conductive Adhesive Type | Description |
---|---|
Epoxy-Based | Two-part adhesives that offer strong mechanical bonds and good electrical conductivity. |
Silicone-Based | Flexible adhesives that maintain conductivity over a wide temperature range. |
Acrylic-Based | Fast-curing adhesives with good adhesion to various surfaces. |
Conductive Pastes
Conductive pastes, also known as conductive inks, are spreadable mixtures that can be applied to surfaces to create conductive traces or patterns. They are often used in combination with stencils or screen printing techniques to create custom circuits on flexible or rigid substrates.
Solderless PCB Connectors
Solderless PCB connectors provide a way to interface between PCBs and other components or modules without the need for soldering.
Pin Headers and Sockets
Pin headers and sockets are commonly used for connecting PCBs to breadboards, jumper wires, or other boards. Male pin headers are soldered to the PCB, while female sockets are used to make the removable connection.
Edge Connectors
Edge connectors are designed to mate with the exposed copper pads along the edge of a PCB. They provide a simple and effective way to connect a PCB to another board or system without the need for additional wiring.
Press-Fit Connectors
Press-fit connectors, also known as solderless press-fit or compliant pin connectors, feature pins with a unique geometry that allows them to be pressed directly into plated through-holes on a PCB. The pins make a secure mechanical and electrical connection without the need for soldering.
Wire Wrapping Techniques
Wire wrapping is a solderless method for making connections between components using thin, solid-core wire and specialized wire wrapping tools.
Wire Wrapping Process
The wire wrapping process involves the following steps:
- Strip a small portion of insulation from the end of the wire.
- Insert the wire into the wire wrapping tool.
- Place the tool over the square post of the component or socket.
- Rotate the tool to wrap the wire tightly around the post.
- Trim the excess wire and move on to the next connection.
Advantages of Wire Wrapping
Wire wrapping offers several advantages over soldering:
- Creates a secure, gas-tight connection that is resistant to vibration and thermal stress
- Allows for high-density wiring and compact designs
- Facilitates easy modification and troubleshooting, as connections can be unwrapped and rewrapped as needed
- Suitable for high-reliability applications, such as aerospace or military systems
Modular Electronics and Plug-and-Play Systems
Modular electronics and plug-and-play systems are designed to simplify the assembly process by providing pre-built modules that can be easily connected without soldering.
Modular Electronics
Modular electronics involve the use of standardized, self-contained modules that perform specific functions. These modules can be connected together to create custom systems or devices without the need for complex wiring or soldering.
Examples of modular electronics include:
- Arduino shields and compatible modules
- Raspberry Pi HATs (Hardware Attached on Top)
- Grove System modules and sensors
- Adafruit Feather boards and FeatherWings
Plug-and-Play Systems
Plug-and-play systems take the concept of modular electronics a step further by providing a complete ecosystem of compatible components that can be easily connected and configured without the need for soldering or advanced technical knowledge.
Examples of plug-and-play systems include:
- littleBits electronic building blocks
- Snap Circuits educational kits
- SAM Labs wireless electronics kits
- Piper Computer Kit
These systems often use proprietary connectors or magnetic couplings to ensure a secure and foolproof connection between modules.
Troubleshooting and Best Practices
When working with solderless assembly methods, it’s important to keep the following troubleshooting tips and best practices in mind:
- Double-check all connections before applying power to the circuit to avoid short circuits or unintended paths.
- Use a multimeter to test continuity and verify connections.
- Keep your workspace clean and organized to minimize the risk of errors or accidents.
- Use appropriate tools and follow the manufacturer’s instructions for each solderless assembly method.
- Be mindful of the current and voltage limitations of each connection method, and choose the appropriate technique for your application.
- When troubleshooting, systematically isolate and test each component or module to identify the source of the problem.
- Regularly inspect and maintain your solderless connections, especially in applications subject to vibration or environmental stress.
Frequently Asked Questions (FAQ)
-
Q: Can solderless assembly methods be used for all electronic projects?
A: While solderless assembly methods are versatile and suitable for many projects, some applications may require the strength and reliability of soldered connections. High-current, high-voltage, or high-reliability systems may benefit from traditional soldering techniques. -
Q: Are solderless connections as reliable as soldered ones?
A: When properly implemented, solderless connections can be reliable and effective. However, the reliability of solderless connections depends on factors such as the quality of the components, the skill of the assembler, and the environment in which the device will be used. -
Q: Can I mix and match different solderless assembly methods in a single project?
A: Yes, it’s often possible and beneficial to combine different solderless assembly methods to suit the specific needs of your project. For example, you might use a breadboard for prototyping, then transition to crimp connectors and terminal blocks for a more permanent installation. -
Q: Are there any limitations to using solderless assembly methods?
A: Some limitations of solderless assembly methods include current and voltage restrictions, potential for intermittent connections due to vibration or environmental factors, and the need for careful planning and organization to ensure a successful assembly. -
Q: What skills do I need to work with solderless assembly methods?
A: Working with solderless assembly methods requires attention to detail, basic understanding of electronic principles, and the ability to follow instructions and best practices. Familiarity with tools such as wire strippers, crimpers, and multimeters can also be beneficial.
Conclusion
Solderless assembly methods offer a wide range of possibilities for creating electronic projects without the need for soldering. From breadboards and jumper wires to crimp connectors and modular systems, these techniques provide accessibility, flexibility, and efficiency in the development process.
By understanding the various solderless assembly methods and their applications, you can choose the best approach for your specific project and skill level. Whether you’re a beginner learning the basics of electronics or an experienced maker looking to streamline your workflow, solderless assembly can open up new opportunities for innovation and creativity.
As you explore the world of solderless assembly, remember to prioritize safety, organization, and attention to detail. With practice and persistence, you’ll be able to create robust and reliable electronic projects that showcase your skills and imagination.
Leave a Reply