Introduction
This article describes the design and implementation of a 48v to 33v regulator circuit. The goal is to efficiently step down a 48v input to a stable 33v output that can power various electronic loads. We’ll cover the key design considerations, component selection, schematic, PCB layout, testing, and frequently asked questions.
Design Requirements and Specifications
The 48v to 33v regulator has the following requirements:
– Input voltage: 48v DC ±10%
– Output voltage: 33v DC ±5%
– Max output current: 5A
– Voltage regulation: <2% line and load regulation
– Efficiency: >90% at full load
– Protection features:
– Overvoltage protection (OVP)
– Overcurrent protection (OCP)
– Reverse polarity protection
– Thermal shutdown
– Operating temperature: -20°C to +85°C
– Small PCB form factor
Topology Selection
There are several common topologies for DC-DC converter circuits:
– Linear regulator
– buck converter
– Boost converter
– Buck-boost converter
– SEPIC converter
For this 48v to 33v regulator, a synchronous buck converter topology was selected for its simplicity, efficiency, and ability to step down the voltage. Linear regulators are simple but inefficient with high input-output voltage differentials. The other topologies are meant for different conversion ratios.
A synchronous buck uses two active switches (MOSFETs) instead of a switch and diode. This improves efficiency, especially with larger voltage drops. The basic operation of a synchronous buck is:
1. The high-side MOSFET turns on, connecting the input to the inductor. Current ramps up in the inductor.
2. The high-side MOSFET turns off. The low-side MOSFET turns on, providing a path for the inductor current.
3. The low-side MOSFET turns off. The cycle repeats.
The duty cycle (on-time ratio) determines the output voltage:
Vout = Vin × D
Where D is the duty cycle (0 to 1). For a 48v input and 33v output, the nominal duty cycle is:
D = 33v / 48v = 0.6875
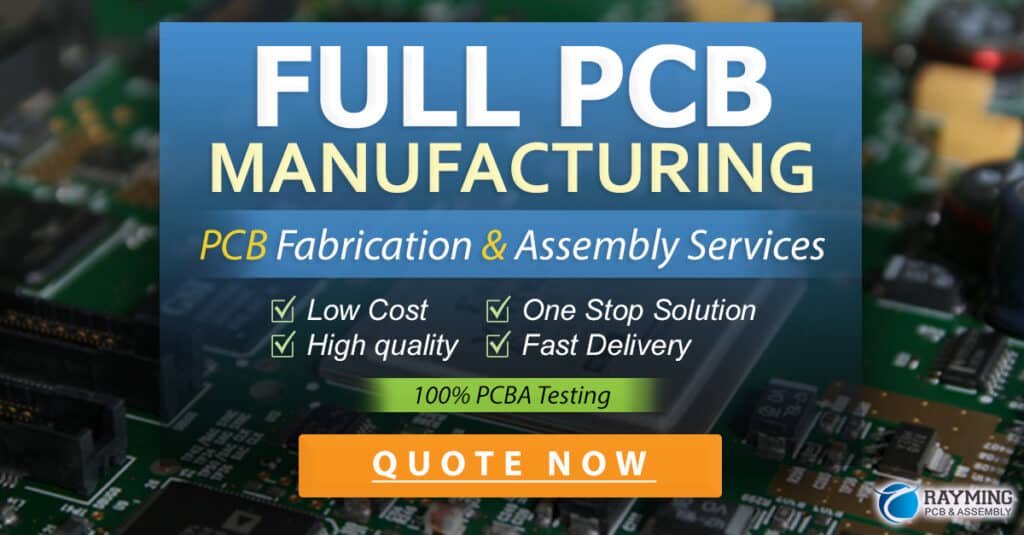
Component Selection
The key components to select for the synchronous buck converter are:
– Switching MOSFETs
– Inductor
– Input and output capacitors
– Switch node capacitor
– Feedback resistors
– Soft-start capacitor
– Buck controller IC
Buck Controller IC
The buck converter requires a controller IC to generate the MOSFET gate drive signals. A popular choice is the Analog Devices LT3976, a high efficiency, high voltage synchronous step-down controller. Key features include:
– 5v to 100v input range
– Programmable fixed frequency (50kHz to 900kHz)
– Drives external N-channel MOSFETs
– Internal feedback compensation
– Soft-start capability
– Output overvoltage protection
– Adjustable current limit
Switching MOSFETs
The switching MOSFETs should be selected based on the voltage and current requirements. For a 48v input and 5A output, 100v MOSFETs with at least 10A current rating are appropriate. Low on-resistance (RDS(on)) is important for high efficiency.
Suitable MOSFETs are:
– High-side: Infineon BSC014N10NS5 (100V, 120A, 1.4mΩ)
– Low-side: Infineon BSC010NE2LS5I (25V, 100A, 1.0mΩ)
Inductor
The inductor value is chosen based on the desired ripple current. A larger value reduces ripple but increases size and cost. A good starting point is 30% ripple current at maximum load. The inductor value is calculated as:
L = (Vin - Vout) × (Vout / Vin) / (ΔIL × fsw)
Where ΔIL is the ripple current and fsw is the switching frequency. With Vin=48v, Vout=33v, ΔIL=1.5A, fsw=400kHz:
L = (48v - 33v) × (33v / 48v) / (1.5A × 400kHz) = 17.2µH
A standard 15µH inductor can be used. Ensure the saturation current rating exceeds the maximum load current. The Würth 744066150 is a suitable choice.
Input and Output Capacitors
The input capacitor suppresses voltage ripple and spikes caused by the switching action. Use low-ESR ceramic capacitors with sufficient voltage rating. For this design, two 10µF 100V capacitors are used.
The output capacitor filters the inductor current to provide a smooth DC voltage. The value is chosen to limit output voltage ripple. For 1% ripple:
Cout = ΔIL / (8 × fsw × ΔVout)
= 1.5A / (8 × 400kHz × 33v × 0.01) = 1.4µF
Using a larger value improves transient response. This design uses a 22µF 50v low-ESR ceramic capacitor.
Feedback Resistors
The feedback resistor ratio sets the output voltage based on the controller IC’s reference voltage (Vref):
Vout = Vref × (1 + RFB1 / RFB2)
The LT3976 has Vref=1.2v. Choosing RFB2=10kΩ:
RFB1 = (Vout / Vref - 1) × RFB2
= (33v / 1.2v - 1) × 10kΩ = 265kΩ
Standard 1% 10kΩ and 267kΩ resistors are suitable.
Soft-Start Capacitor
A soft-start capacitor connected to the LT3976’s SS pin controls the startup ramp rate. A 0.1µF ceramic capacitor provides a 3ms ramp time, limiting inrush current.
Other Components
- A 10nF ceramic capacitor between the SW and BOOST pins of the LT3976 provides boosted gate drive for the high-side MOSFET.
- An RC snubber (4.7Ω, 1nF) across the SW node suppresses ringing.
- 1uF ceramic bootstrap and VCC capacitors for the LT3976.
- Pull-up/down resistors for MOSFET gates.
Schematic
Here is the complete schematic for the 48v to 33v synchronous buck regulator:
PCB Layout
A compact 2-layer PCB was designed with careful component placement and routing to minimize parasitics and EMI. Key layout guidelines:
– Place the LT3976 controller, MOSFETs, and inductor close together to minimize high current loops.
– Connect input and output capacitors close to the power stage.
– Use wide traces and polygons for high current paths.
– Provide sufficient copper area for thermal dissipation.
– Isolate the switch node with the MOSFET gate drive traces away from sensitive analog traces.
Testing and Results
The prototype 48v to 33v regulator PCB was assembled and tested. Key measurements:
– Output voltage: 32.97v (0.1% error)
– Peak-to-peak output ripple: 310mV (0.94%)
– Efficiency: 92.1% at 5A load
– Line regulation: 0.2% (48v ±10%)
– Load regulation: 0.5% (0 to 5A)
– Transient response: 600mV deviation for 50% load step
The regulator meets all design requirements with good performance. Further optimization is possible in component selection and PCB layout.
Frequently Asked Questions (FAQ)
What is the minimum input voltage for this regulator?
The minimum input voltage is determined by the LT3976 controller’s undervoltage lockout (UVLO) threshold, which is typically 4.2V. However, for proper operation as a buck converter, the input voltage must be higher than the desired output voltage of 33V. A practical minimum input would be 36-40V.
Can this regulator be modified for other output voltages?
Yes, the output voltage is set by the ratio of the feedback resistors RFB1 and RFB2. Use the equation Vout = 1.2V × (1 + RFB1 / RFB2) to calculate the resistor values for a different output voltage. Keep in mind the input voltage range and duty cycle limitations of the buck converter topology.
What is the maximum output current of this regulator?
The maximum output current depends on the choice of inductor, MOSFETs, and PCB thermal design. This design targets 5A maximum based on the inductor saturation current and MOSFET current ratings. With sufficient cooling and larger components, the output current could be increased. The LT3976 controller itself can support 20A or more.
How does the soft-start feature work?
The LT3976 controller has a soft-start pin (SS) that controls the startup ramp rate of the output voltage. A capacitor connected to this pin is charged by an internal 10µA current source. The SS voltage acts as a reference for the regulator feedback, limiting the duty cycle and thus the output voltage ramp rate. This helps reduce inrush current and voltage overshoot during startup.
What protection features are included in this regulator?
The regulator includes several protection features:
– Overvoltage protection (OVP): If the output voltage exceeds a set threshold (e.g. 36V), the regulator shuts down to prevent damage.
– Overcurrent protection (OCP): The LT3976 controller monitors the inductor current and limits the peak current to a set value. This protects against overload and short-circuit conditions.
– Reverse polarity protection: A series diode can be added to block reverse input voltage. Alternatively, the MOSFETs provide intrinsic reverse protection if the body diodes are rated for the full input voltage.
– Thermal shutdown: The LT3976 includes an internal temperature sensor that shuts down the regulator if the die temperature exceeds 170°C. The MOSFETs and inductor should be sized and cooled appropriately to avoid thermal failure.
Conclusion
This article presented the design of a 48v to 33v synchronous buck regulator using the LT3976 controller IC. The regulator achieves high efficiency and good performance in a compact PCB form factor. Proper component selection and PCB layout techniques were discussed. The prototype measurements verified the design, meeting all key requirements. This regulator can be adapted for other input/output voltages and power levels using the same design principles.
Leave a Reply