What are 10 Ounce Copper PCBs?
10 ounce copper printed circuit boards (PCBs) are a type of high-current carrying capacity PCB that uses a thicker layer of copper – 10 ounces per square foot – compared to standard 1-2 oz copper PCBs. The thicker copper allows 10 oz PCBs to handle much higher currents, up to 10-15 amps per trace. This makes them ideal for power electronics applications that require high current handling, such as:
- Power supplies
- motor controllers and drivers
- Battery management systems
- Solar inverters
- Electric vehicle charging stations
- High-power LED lighting
Advantages of 10 Oz Copper PCBs
There are several key benefits to using 10 oz copper PCBs for high-current applications:
-
Higher Current Capacity – The thicker copper traces allow 10 oz PCBs to carry much higher currents than standard PCBs. A single 10 oz trace can handle 10-15A.
-
Lower Resistance – The thicker copper results in lower trace resistance. This reduces voltage drops and power losses, improving efficiency.
-
Better Heat Dissipation – The additional copper helps conduct heat away from components more effectively. This improves reliability and allows components to run cooler.
-
Greater Mechanical Strength – 10 oz PCBs are significantly more robust and less prone to damage than standard thickness boards. This improves durability and reliability in demanding applications.
-
Reduced EMI – The lower resistance and better grounding provided by the thicker copper help reduce electromagnetic interference (EMI).
Considerations for 10 Oz Copper PCB Design
While 10 oz copper PCBs offer significant performance benefits, there are some important design considerations to keep in mind:
-
Trace Widths – 10 oz copper traces will be much wider than standard 1 oz traces for a given current. This can make routing more challenging in dense designs. Trace width calculators should be used.
-
Via Sizes – Vias need to be larger on 10 oz boards to allow enough copper in the barrel for carrying high currents. Vias of 20-30 mils or larger are typical.
-
Minimum Hole Sizes – The thicker copper makes it more difficult to drill small holes. The minimum hole size is typically 12-13 mils for 10 oz boards.
-
annular rings – The annular ring (copper pad around holes) needs to be larger to account for the larger hole sizes. 10-15 mil annular rings are recommended.
-
Solder Mask Dams – Clearances of 15 mils or more are needed between large copper pours and traces to allow for solder mask dams. This prevents shorts from solder bridges.
-
Thermal Relief – Thermal relief spokes are needed on large copper planes and pours connected to pads. This allows enough heat for soldering without sinking all the heat away.
Here is a table summarizing some typical design rules for 10 oz copper PCBs:
Design Rule | Typical Value |
---|---|
Minimum trace width | 30 mil |
Minimum via diameter | 20 mil |
Minimum hole size | 13 mil |
Minimum annular ring | 15 mil |
Solder mask dam size | 15 mil |
Thermal relief spoke width | 10 mil |
Migrating Designs to 10 Oz Copper
Many designs that were originally done using standard 1-2 oz copper PCBs can benefit from migration to 10 oz copper. The thicker copper allows higher currents and lower losses. However, some design changes are usually needed when converting a design to 10 oz copper:
-
Traces will need to be made wider to take advantage of the higher current capacity. A 10 oz trace will be about 3 times wider than a 1 oz trace for the same current.
-
Vias, pads, and holes will need to be made larger to allow for the thicker copper plating. A via that was 10 mils on a 1 oz board may need to be 20-25 mils for 10 oz.
-
Footprints for through-hole components may need to be adjusted for larger hole sizes and annular rings.
-
Layout spacing may need to be adjusted to allow for the larger features and spacing requirements of 10 oz copper.
-
Solder mask and paste layer artwork may need to be updated for the larger dams and clearances required.
It’s important to work closely with your PCB manufacturer when migrating designs to 10 oz copper. They can provide guidance on design rules and help identify any issues with the converted design.
Design library migration
Migrating an existing PCB design library to support 10 oz copper designs involves updating component footprints, adjusting design rules, and modifying CAD templates.
Updating Footprints for 10 Oz Copper
The first step is to update the land patterns and holes sizes in component footprints for 10 oz compatibility:
-
Hole sizes should be increased to at least 13 mils to allow for the thicker barrel plating. Even larger holes may be needed for high-current pins.
-
Annular rings should be increased to 10-15 mils to allow for the larger hole sizes while still maintaining enough copper for current carrying.
-
Thermal relief should be added to pads connected to large copper pours. A typical thermal consists of four 10 mil wide spokes connecting the pad to the pour.
-
Solder mask openings may need to be enlarged to allow for the larger copper features and clearances.
For surface mount components, the footprints will generally not need to be changed for 10 oz copper, since they don’t have through-hole pins. However, the solder mask opening may still need to be adjusted.
Adjusting Trace Width Design Rules
The PCB CAD design rules should be updated for 10 oz copper trace widths. Here is a table of suggested 10 oz trace widths for various current levels:
Current | Trace Width |
---|---|
1A | 10 mil |
2A | 25 mil |
5A | 50 mil |
10A | 100 mil |
The actual trace widths will also depend on acceptable temperature rise and voltage drop for the design. Still, these values provide a good starting point.
In the CAD design rules, the default trace width and clearance rules should be updated. Rules for power nets that will use wide 10 oz traces should be set to the appropriate widths.
Updating CAD Templates
CAD templates for schematic symbols, footprints, and layout artwork should be updated to support 10 oz copper designs:
- Schematic symbol templates should have 10 oz compatible footprints assigned.
- Layout templates should have 10 oz design rules loaded.
- Gerber and drill output templates may need adjustment for proper 10 oz layer mapping.
Having 10 oz compatible templates makes it easier to ensure that new designs are created with the appropriate rules and settings for 10 oz copper.
FAQ
Q: When should I consider using 10 oz copper PCBs?
A: 10 oz copper PCBs are best suited for applications requiring high current carrying capacity, typically over 5-7 amps per trace. They are commonly used in power electronics, automotive, and industrial control applications. If your design has high current traces or suffers from excessive voltage drop or heating, 10 oz copper can help.
Q: Are 10 oz copper PCBs more expensive?
A: Yes, 10 oz copper boards will be more expensive than standard 1-2 oz boards due to the additional copper used. The price increase depends on the board size and layer count, but is typically 20-50% more than a comparable standard board. However, the improved performance and reliability can make the added cost worthwhile for many applications.
Q: What are the drawbacks of using 10 oz copper?
A: The main drawbacks of 10 oz copper are the increased board cost and the need for wider traces and larger features. This can make routing more challenging, especially in dense designs. The thicker copper also requires more etching time and can be more prone to undercutting during fabrication. Designers need to work closely with their manufacturer to ensure a successful 10 oz design.
Q: Can I mix 10 oz and 1 oz copper on the same board?
A: Yes, it is possible to mix 10 oz and standard 1-2 oz copper weights on different layers of the same board. This allows the benefits of 10 oz to be gained on the power layers while keeping the signal layers at standard weights for easier routing. The stackup design must account for the different thicknesses to maintain controlled impedances. Many PCB manufacturers offer standard stackups that mix 10 oz and 1 oz layers.
Q: What cad tools support 10 oz copper design?
A: Most modern PCB CAD tools, such as Altium Designer, Cadence Allegro, Mentor PADS, and KiCad, support 10 oz copper design. The key requirements are the ability to specify different copper weights per layer, define trace width and clearance rules based on copper weight, and assign complex pad stacks. Check with your CAD vendor for specific 10 oz design capabilities and requirements.
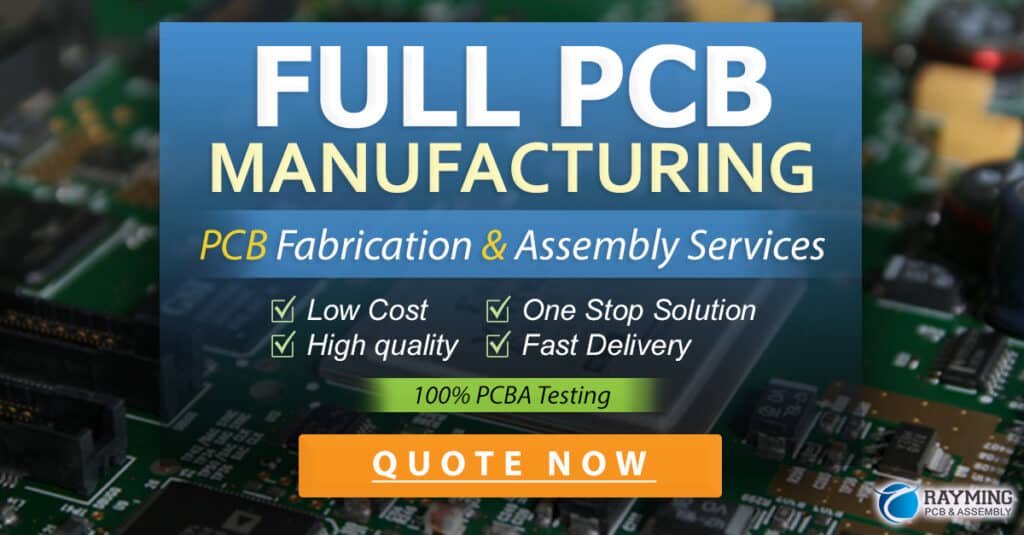
Leave a Reply