Introduction to Radar Technology in the Automotive Industry
In recent years, the automotive industry has witnessed a significant surge in the adoption of advanced driver assistance systems (ADAS) and autonomous driving technologies. One of the key components enabling these innovations is the 77 GHz radar system. This high-frequency radar technology offers superior performance in terms of range, resolution, and weather resilience compared to its lower-frequency counterparts. However, designing and manufacturing printed circuit boards (PCBs) for 77 GHz radar systems presents unique challenges, particularly in the areas of routing and signal integrity.
The Importance of 77 GHz Radar in Automotive Applications
77 GHz radar systems have become increasingly popular in the automotive industry due to their numerous advantages:
- Long-range detection: 77 GHz radar can detect objects up to 250 meters away, making it ideal for highway driving and adaptive cruise control applications.
- High resolution: The shorter wavelength of 77 GHz signals enables better resolution, allowing for more precise object detection and classification.
- Weather resilience: Unlike optical sensors, 77 GHz radar can operate effectively in adverse weather conditions such as rain, fog, and snow.
- Compact size: The small wavelength of 77 GHz signals allows for the design of compact and lightweight radar modules, which can be easily integrated into vehicles.
Challenges in 77 GHz Radar PCB Design
Designing PCBs for 77 GHz radar systems presents several challenges that must be addressed to ensure optimal performance and reliability:
- High-frequency signal integrity: At 77 GHz, signal integrity issues such as reflections, crosstalk, and losses become more pronounced, requiring careful design and layout techniques.
- Material selection: The choice of PCB substrate material is critical, as it must have low dielectric loss and stable properties at high frequencies.
- Manufacturability: The small feature sizes and tight tolerances required for 77 GHz PCBs can be challenging for manufacturers, necessitating close collaboration between design and production teams.
- Thermal management: High-frequency components generate significant heat, which must be effectively dissipated to ensure reliable operation and prevent premature failure.
PCB Material Selection for 77 GHz Radar
Choosing the right PCB substrate material is crucial for ensuring the performance and reliability of 77 GHz radar systems. The ideal material should have the following properties:
- Low dielectric constant (Dk): A lower Dk value reduces the wavelength of the signal in the material, allowing for smaller feature sizes and improved signal propagation.
- Low dissipation factor (Df): A low Df value minimizes signal loss and helps maintain signal integrity at high frequencies.
- Thermal stability: The material should maintain its properties over a wide temperature range to ensure reliable operation in automotive environments.
- Mechanical stability: The material should have good mechanical strength and dimensional stability to withstand the stresses of manufacturing and operation.
Some commonly used PCB materials for 77 GHz radar applications include:
Material | Dielectric Constant (Dk) | Dissipation Factor (Df) |
---|---|---|
Rogers RO3003 | 3.00 | 0.0010 |
Rogers RO4835 | 3.48 | 0.0037 |
ISOLA I-Tera MT40 | 3.45 | 0.0030 |
NELCO N4000-13 SI | 3.14 | 0.0025 |
High-Frequency PCB Routing Techniques
Effective PCB routing is essential for maintaining signal integrity and minimizing losses in 77 GHz radar systems. Some key techniques include:
Microstrip and Stripline Transmission Lines
Microstrip and stripline transmission lines are commonly used for high-frequency signal routing. Microstrip lines are exposed on the top layer of the PCB, while striplines are embedded within the PCB layers.
Advantages of microstrip lines:
– Easy to fabricate and modify
– Lower cost compared to striplines
– Allows for the placement of components on the same layer
Advantages of striplines:
– Better shielding and isolation from external interference
– Lower radiation losses
– More consistent impedance control
grounded coplanar waveguide (GCPW)
Grounded coplanar waveguide (GCPW) is another popular transmission line structure for high-frequency PCBs. In a GCPW, the signal trace is flanked by ground planes on the same layer, with additional ground planes on the adjacent layers.
Advantages of GCPW:
– Excellent isolation and shielding
– Low dispersion and radiation losses
– Allows for easy integration of components and transitions
Impedance Matching and Termination
Proper impedance matching and termination are critical for minimizing reflections and ensuring efficient power transfer in 77 GHz radar PCBs. Some common techniques include:
- Resistive termination: Adding a resistor with a value equal to the characteristic impedance of the transmission line at the end of the signal path.
- Capacitive termination: Using a capacitor to provide a high-frequency short-circuit termination while allowing DC bias to pass through.
- Inductive termination: Employing an inductor to provide a high-frequency open-circuit termination while allowing low-frequency signals to pass.
Via Optimization
Vias are used to interconnect signals between different layers of a PCB. At 77 GHz, via design and optimization are critical to minimize reflections and signal loss. Some best practices include:
- Minimize via length: Shorter vias reduce the inductance and improve signal propagation.
- Optimize via diameter: Choosing the appropriate via diameter based on the signal wavelength and PCB thickness helps maintain impedance control.
- Use via shielding: Adding ground vias around signal vias helps reduce crosstalk and improve isolation.
- Employ via back-drilling: Removing the unused portion of the via stub by back-drilling can help reduce reflections and improve signal integrity.
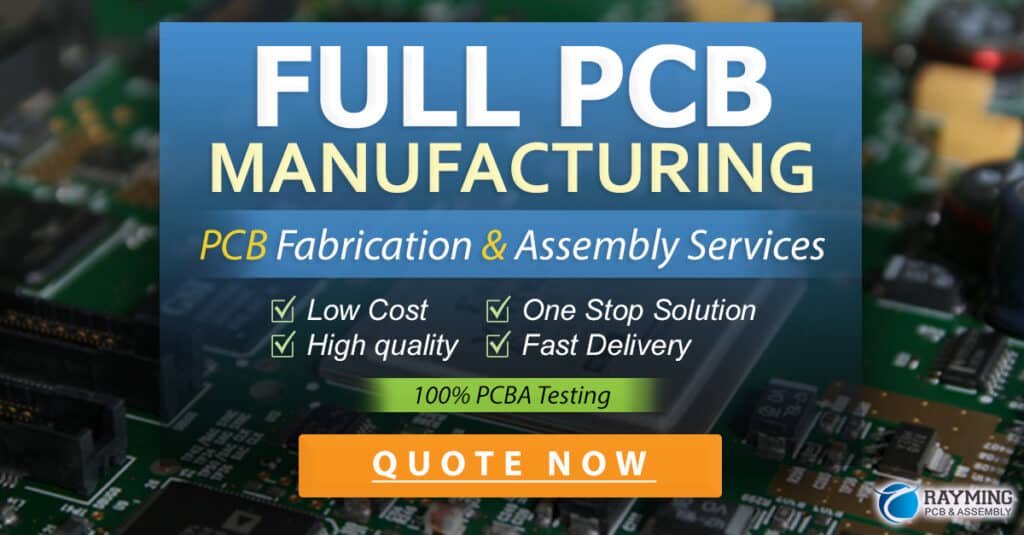
signal integrity analysis and Simulation
To ensure the performance and reliability of 77 GHz radar PCBs, it is essential to conduct thorough signal integrity analysis and simulation during the design process. Some key aspects to consider include:
Time-Domain Reflectometry (TDR)
Time-Domain Reflectometry (TDR) is a technique used to characterize the impedance profile of a transmission line and identify discontinuities or reflections. By sending a high-frequency pulse through the signal path and analyzing the reflected waveform, designers can pinpoint and address impedance mismatches.
3D Electromagnetic (EM) Simulation
3D electromagnetic (EM) simulation tools, such as Ansys HFSS or CST Studio Suite, allow designers to accurately model and analyze the high-frequency behavior of PCBs. These tools can help optimize transmission line dimensions, via placement, and component layout to minimize losses and ensure signal integrity.
Eye Diagram Analysis
Eye diagram analysis is a technique used to assess the quality of a digital signal by overlaying multiple signal transitions and observing the resulting pattern. A wide, open eye indicates good signal integrity, while a closed or distorted eye suggests the presence of signal degradation or interference.
Thermal Management Considerations
Effective thermal management is crucial for ensuring the reliable operation of 77 GHz radar PCBs. High-frequency components, such as power amplifiers and voltage-controlled oscillators (VCOs), generate significant heat that must be efficiently dissipated to prevent performance degradation and premature failure.
Some thermal management techniques for 77 GHz radar PCBs include:
- Thermal vias: Adding thermal vias beneath high-power components helps conduct heat away from the device and into the PCB layers or external heatsinks.
- Heatsinks and heat spreaders: Attaching heatsinks or heat spreaders to high-power components helps dissipate heat more efficiently by increasing the surface area for convection cooling.
- Thermal interface materials (TIMs): Using thermal interface materials, such as thermal pads or pastes, between components and heatsinks or heat spreaders helps improve thermal conductivity and reduce thermal resistance.
- Airflow and ventilation: Ensuring adequate airflow over the PCB and high-power components, either through natural convection or forced air cooling, helps remove heat more effectively.
Manufacturing Considerations for 77 GHz Radar PCBs
The small feature sizes and tight tolerances required for 77 GHz radar PCBs can pose challenges for manufacturers. To ensure successful fabrication and assembly, consider the following:
- Choose an experienced manufacturing partner: Work with a PCB manufacturer that has experience in producing high-frequency, high-density boards and can meet the necessary tolerances and quality standards.
- Communicate design intent clearly: Provide comprehensive documentation, including detailed layer stackups, material specifications, and critical dimensions, to ensure that the manufacturer understands the design requirements.
- Consider the impact of manufacturing processes: Be aware of the limitations and potential impacts of various manufacturing processes, such as etching, plating, and lamination, on the performance of the final PCB.
- Conduct thorough testing and inspection: Implement rigorous testing and inspection procedures, including automated optical inspection (AOI), X-ray inspection, and electrical testing, to identify and address any manufacturing defects or performance issues.
Frequently Asked Questions (FAQ)
- What are the main advantages of using 77 GHz radar in automotive applications?
-
77 GHz radar offers long-range detection (up to 250 meters), high resolution, weather resilience, and compact size, making it ideal for various automotive applications such as adaptive cruise control and collision avoidance systems.
-
What are the key challenges in designing PCBs for 77 GHz radar systems?
-
The main challenges include ensuring high-frequency signal integrity, selecting suitable PCB materials with low dielectric loss and stable properties, achieving manufacturability with small feature sizes and tight tolerances, and managing thermal dissipation from high-frequency components.
-
What are some common PCB materials used for 77 GHz radar applications?
-
Some common PCB materials for 77 GHz radar include Rogers RO3003, Rogers RO4835, ISOLA I-Tera MT40, and NELCO N4000-13 SI. These materials offer low dielectric constant, low dissipation factor, and good thermal and mechanical stability.
-
What are the main differences between microstrip and stripline transmission lines?
-
Microstrip lines are exposed on the top layer of the PCB and are easier to fabricate and modify, while striplines are embedded within the PCB layers and offer better shielding and isolation from external interference. Striplines also provide more consistent impedance control and lower radiation losses.
-
Why is thermal management important for 77 GHz radar PCBs, and what are some common techniques used?
- Effective thermal management is crucial for ensuring reliable operation and preventing performance degradation or premature failure of high-frequency components. Common techniques include using thermal vias, heatsinks, heat spreaders, thermal interface materials, and ensuring adequate airflow and ventilation.
Conclusion
Designing and manufacturing PCBs for 77 GHz radar systems in automotive applications requires careful consideration of various factors, including material selection, high-frequency routing techniques, signal integrity analysis, thermal management, and manufacturing processes. By understanding and addressing these challenges, engineers can develop robust and reliable radar systems that enhance vehicle safety and enable the development of advanced driver assistance systems and autonomous driving technologies.
As the automotive industry continues to evolve and embrace these cutting-edge technologies, the demand for high-performance 77 GHz radar PCBs will only continue to grow. By staying up-to-date with the latest design techniques, simulation tools, and manufacturing processes, PCB designers and manufacturers can play a crucial role in shaping the future of transportation.
Leave a Reply