Introduction
Printed Circuit Board (PCB) design is a crucial aspect of modern electronics manufacturing. However, despite its importance, there are many misconceptions surrounding PCB design that can lead to costly mistakes and delays in the production process. In this article, we will explore seven of the most common misconceptions about PCB design and provide insights to help you avoid these pitfalls.
Misconception 1: PCB Design Is Easy and Can Be Done Quickly
One of the most common misconceptions about PCB design is that it is a simple and quick process. Many people believe that with the right software tools, anyone can design a PCB in a matter of hours. However, this is far from the truth.
PCB design is a complex process that requires a deep understanding of electronics, materials science, and manufacturing processes. It involves multiple stages, including schematic design, component selection, layout design, and testing. Each stage requires careful consideration and attention to detail to ensure that the final product meets the desired specifications and performs reliably.
Rushing through the PCB design process can lead to a host of problems, including:
- Incorrect component placement
- Signal integrity issues
- Thermal management problems
- Manufacturing defects
To avoid these issues, it is important to allocate sufficient time and resources to the PCB design process. This includes working with experienced designers who have a deep understanding of the various aspects of PCB design and can help ensure that the final product meets all the necessary requirements.
Misconception 2: More Layers Always Mean Better Performance
Another common misconception about PCB design is that more layers always lead to better performance. While it is true that increasing the number of layers can provide more routing space and improve signal integrity, it is not always necessary or desirable.
Adding more layers to a PCB can increase its complexity and cost, as well as introduce new challenges in terms of manufacturing and assembly. In some cases, adding more layers can actually degrade performance by increasing the overall thickness of the board and introducing additional capacitance and inductance.
When deciding on the number of layers for a PCB, it is important to consider the specific requirements of the application and the trade-offs involved. Factors to consider include:
- Signal integrity requirements
- Power distribution needs
- Component placement and routing constraints
- Manufacturing capabilities and costs
In many cases, a well-designed four-layer board can provide excellent performance at a lower cost than a more complex multi-layer board. It is important to work with experienced designers who can help determine the optimal layer stack-up for a given application.
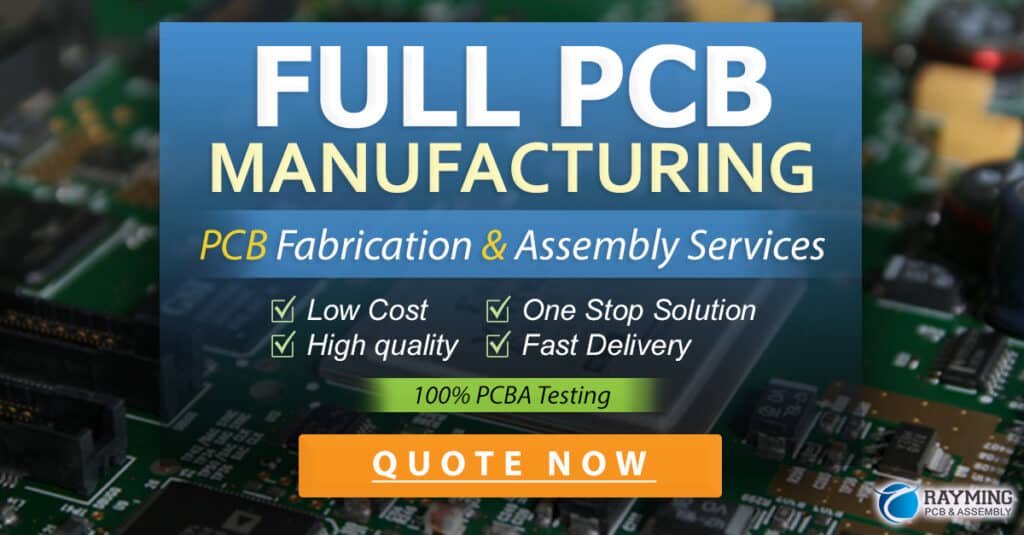
Misconception 3: Autorouting Is Always the Best Option
Autorouting is a feature of many PCB design software tools that automatically routes traces between components based on a set of rules and constraints. While autorouting can be a useful tool for quickly generating a preliminary layout, it is not always the best option for final design.
Autorouting algorithms are based on predefined rules and cannot take into account all the nuances and complexities of a specific design. They may generate layouts that are suboptimal in terms of signal integrity, power distribution, or manufacturing feasibility.
In addition, autorouting can often result in layouts that are difficult to read and understand, making it harder to troubleshoot issues or make modifications later on.
For these reasons, it is often better to use autorouting as a starting point and then refine the layout manually based on the specific requirements of the design. This allows for greater control over the placement of components and routing of traces, and can help ensure that the final design meets all the necessary performance and manufacturing requirements.
Misconception 4: Cheaper Components Always Save Money
When designing a PCB, it can be tempting to choose the cheapest components available in order to save money. However, this is often a common misconception that can lead to costly problems down the line.
Cheaper components may have lower quality or reliability, which can lead to increased failure rates and shorter product lifetimes. They may also have inferior performance characteristics, such as higher resistance or lower current-carrying capacity, which can impact the overall performance of the PCB.
In addition, cheaper components may not be available in the quantities or lead times required for mass production, which can lead to delays and additional costs.
When selecting components for a PCB, it is important to consider the total cost of ownership over the lifetime of the product, rather than just the upfront cost. This includes factors such as:
- Reliability and failure rates
- Performance characteristics
- Availability and lead times
- Compatibility with other components and manufacturing processes
By selecting high-quality components that meet the specific requirements of the application, designers can help ensure the long-term reliability and performance of the final product, even if it means a slightly higher upfront cost.
Misconception 5: Testing Is Optional
Another common misconception about PCB design is that testing is optional or can be skipped to save time and money. However, testing is a critical step in the PCB design process that helps ensure the reliability and performance of the final product.
Testing can take many forms, including:
- Design rule checking (DRC) to verify that the layout meets all the necessary design rules and constraints
- Electrical rule checking (ERC) to verify that the schematic is electrically correct and free of errors
- signal integrity analysis to ensure that signals are transmitted reliably and with minimal distortion
- Thermal analysis to ensure that the PCB can dissipate heat effectively and maintain safe operating temperatures
- Manufacturing testing to verify that the PCB meets all the necessary quality and reliability standards
Skipping testing can lead to a host of problems, including:
- Increased defect rates and field failures
- Delays in time-to-market due to rework and redesign
- Increased costs associated with warranty claims and returns
- Damage to brand reputation and customer satisfaction
To avoid these issues, it is important to allocate sufficient time and resources to testing throughout the PCB design process. This includes working with experienced test engineers who can help develop and execute comprehensive test plans that cover all the necessary aspects of the design.
Misconception 6: All PCB Manufacturers Are the Same
When it comes to manufacturing PCBs, many people assume that all manufacturers are the same and that price is the only factor that matters. However, this is a common misconception that can lead to significant problems down the line.
PCB manufacturing is a complex process that requires specialized equipment, materials, and expertise. Different manufacturers may have different capabilities and quality standards, which can impact the final product.
Factors to consider when selecting a PCB manufacturer include:
- Manufacturing capabilities and capacity
- Quality control processes and certifications
- Material selection and sourcing
- Turnaround times and lead times
- Customer support and communication
Choosing a low-cost manufacturer with subpar capabilities or quality standards can lead to a host of problems, including:
- Increased defect rates and field failures
- Delays in time-to-market due to rework and redesign
- Inconsistent quality and reliability
- Difficulty in scaling up production volumes
To avoid these issues, it is important to work with reputable PCB manufacturers who have a proven track record of quality and reliability. This may require a higher upfront cost but can ultimately save time and money in the long run by ensuring a consistent and reliable supply of high-quality PCBs.
Misconception 7: PCB Design Is a One-Time Process
Finally, a common misconception about PCB design is that it is a one-time process that ends once the PCB is manufactured and assembled. However, in reality, PCB design is an ongoing process that requires continuous improvement and optimization.
As products evolve and new requirements emerge, PCBs may need to be redesigned or updated to meet changing needs. This may involve adding new features, improving performance, or reducing costs.
In addition, as manufacturing processes and technologies evolve, new opportunities may arise for improving the design or manufacturing of PCBs. For example, advances in materials science may enable the use of new substrates or coatings that improve performance or reliability.
To stay competitive and meet changing customer needs, it is important to view PCB design as an ongoing process that requires continuous improvement and optimization. This may involve:
- Regular design reviews and audits to identify areas for improvement
- Collaboration with suppliers and partners to stay up-to-date on the latest technologies and best practices
- Investment in research and development to explore new materials, processes, and designs
- Continuous testing and validation to ensure that designs meet all the necessary performance and reliability standards
By viewing PCB design as an ongoing process, companies can stay ahead of the curve and deliver high-quality, reliable products that meet the evolving needs of their customers.
Conclusion
PCB design is a complex and critical process that requires careful consideration and attention to detail. By understanding and avoiding the seven common misconceptions outlined in this article, designers can help ensure the success of their PCB projects and deliver high-quality, reliable products to their customers.
Misconception | Reality |
---|---|
PCB design is easy and can be done quickly | PCB design is a complex process that requires time and expertise |
More layers always mean better performance | The optimal number of layers depends on the specific requirements of the application |
Autorouting is always the best option | Manual routing allows for greater control and optimization of the layout |
Cheaper components always save money | High-quality components can provide better performance and reliability in the long run |
Testing is optional | Testing is a critical step in ensuring the reliability and performance of the final product |
All PCB manufacturers are the same | Different manufacturers have different capabilities and quality standards |
PCB design is a one-time process | PCB design is an ongoing process that requires continuous improvement and optimization |
By working with experienced designers, selecting high-quality components and manufacturers, and allocating sufficient time and resources to testing and optimization, companies can create PCBs that meet the highest standards of performance, reliability, and cost-effectiveness.
Frequently Asked Questions (FAQ)
- What is the most important factor to consider when designing a PCB?
The most important factor to consider when designing a PCB is the specific requirements of the application. This includes factors such as signal integrity, power distribution, thermal management, and manufacturing feasibility. By understanding and prioritizing these requirements, designers can create PCBs that meet the highest standards of performance and reliability.
- How can I ensure the reliability of my PCB design?
To ensure the reliability of your PCB design, it is important to follow best practices in design, component selection, and testing. This includes using high-quality components, designing for manufacturability, and conducting comprehensive testing and validation throughout the design process. Working with experienced designers and manufacturers can also help ensure the reliability of your PCB design.
- What is the difference between autorouting and manual routing?
Autorouting is a feature of PCB design software that automatically routes traces between components based on predefined rules and constraints. Manual routing, on the other hand, involves manually placing and routing traces based on the specific requirements of the design. While autorouting can be a useful tool for quickly generating a preliminary layout, manual routing allows for greater control and optimization of the final design.
- How do I select the right PCB manufacturer for my project?
When selecting a PCB manufacturer, it is important to consider factors such as manufacturing capabilities, quality control processes, material selection, and customer support. Look for manufacturers with a proven track record of quality and reliability, and be sure to communicate your specific requirements and expectations clearly. It may also be helpful to request samples or references from previous clients to assess the manufacturer’s capabilities and quality.
- How often should I review and update my PCB designs?
The frequency of PCB design reviews and updates will depend on the specific requirements and lifecycle of your product. In general, it is a good idea to conduct regular design reviews and audits to identify areas for improvement and ensure that your designs are meeting all the necessary performance and reliability standards. As new technologies and requirements emerge, it may also be necessary to update or redesign your PCBs to stay competitive and meet changing customer needs. By viewing PCB design as an ongoing process and investing in continuous improvement and optimization, you can ensure the long-term success of your products.
Leave a Reply