Introduction to additive manufacturing In-House
Additive manufacturing, also known as 3D printing, has revolutionized the way products are designed, prototyped, and manufactured. As the technology continues to advance, more and more companies are considering bringing additive manufacturing in-house to reap the numerous benefits it offers. In this article, we will explore seven key advantages of implementing additive manufacturing within your organization.
1. Faster Prototyping and Product Development
One of the most significant benefits of bringing additive manufacturing in-house is the ability to accelerate the prototyping and product development process. With 3D printing technology, designers and engineers can quickly create physical prototypes from digital designs, allowing for rapid iteration and refinement.
Reduced Lead Times
In-house additive manufacturing eliminates the need to outsource prototyping to external service providers, significantly reducing lead times. This enables companies to move from concept to final product more efficiently, giving them a competitive edge in the market.
Improved Design Flexibility
Additive manufacturing allows for greater design flexibility compared to traditional manufacturing methods. Complex geometries and intricate features can be easily incorporated into designs, enabling the creation of innovative and optimized products.
2. Cost Savings
Bringing additive manufacturing in-house can lead to substantial cost savings for companies in various ways.
Reduced Tooling Costs
Traditional manufacturing methods often require expensive tooling and molds, which can be costly and time-consuming to produce. Additive manufacturing eliminates the need for tooling, as parts are built directly from digital files, resulting in significant cost savings.
Lower Inventory Costs
With in-house additive manufacturing, companies can produce parts on-demand, reducing the need for large inventory stockpiles. This just-in-time (JIT) manufacturing approach minimizes inventory costs and reduces the risk of obsolete stock.
Cost-Effective Low-Volume Production
Additive manufacturing is particularly cost-effective for low-volume production runs. Unlike traditional methods that require high upfront costs for tooling and setup, 3D printing allows for the economical production of small batches or even single parts.
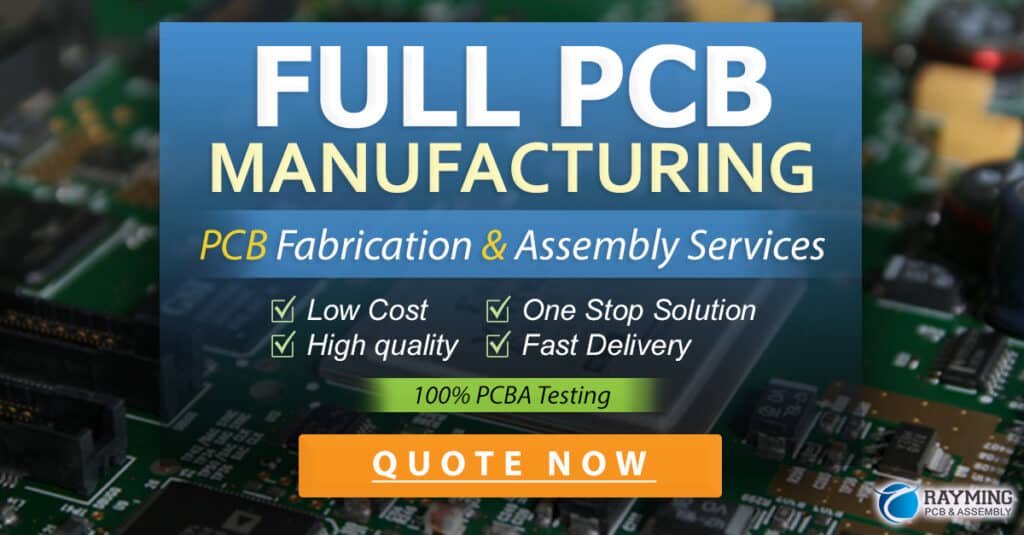
3. Enhanced Customization and Personalization
Additive manufacturing enables companies to offer highly customized and personalized products to their customers.
Mass Customization
With 3D printing, it is possible to produce unique, one-of-a-kind products without incurring additional costs. This opens up opportunities for mass customization, where customers can personalize products to their specific requirements.
Improved Customer Satisfaction
By offering customized and personalized products, companies can enhance customer satisfaction and build stronger relationships with their clients. This can lead to increased customer loyalty and repeat business.
4. Streamlined Supply Chain
Bringing additive manufacturing in-house can streamline the supply chain and reduce dependencies on external suppliers.
Reduced Reliance on External Suppliers
With in-house 3D printing capabilities, companies can produce parts and components internally, reducing their reliance on external suppliers. This gives organizations greater control over their supply chain and minimizes the risk of supply disruptions.
Shorter Lead Times
By producing parts in-house, companies can significantly shorten lead times compared to outsourcing production to external manufacturers. This allows for faster response to market demands and customer needs.
5. Improved Product Performance
Additive manufacturing enables the creation of products with improved performance characteristics.
Lightweight and Optimized Designs
3D printing allows for the creation of lightweight and optimized designs that are difficult or impossible to achieve with traditional manufacturing methods. By reducing weight and optimizing geometry, products can exhibit enhanced performance, such as increased strength-to-weight ratios or improved thermal management.
Functional Integration
Additive manufacturing enables the consolidation of multiple parts into a single, integrated component. This functional integration can lead to improved product performance, reduced assembly time, and increased reliability.
6. Increased Innovation and Creativity
Bringing additive manufacturing in-house fosters a culture of innovation and creativity within the organization.
Freedom to Experiment
With in-house 3D printing capabilities, designers and engineers have the freedom to experiment with new ideas and concepts. They can quickly iterate and test designs, encouraging a more innovative and creative approach to product development.
Rapid Prototyping and Proof of Concept
Additive manufacturing allows for rapid prototyping and proof of concept, enabling teams to validate ideas and designs early in the development process. This accelerates the innovation cycle and reduces the risk of investing in unviable concepts.
7. Competitive Advantage
Implementing additive manufacturing in-house can provide companies with a significant competitive advantage in their respective markets.
Faster Time-to-Market
By accelerating prototyping and product development, companies can bring new products to market faster than their competitors. This first-mover advantage can capture market share and establish a strong position in the industry.
Differentiation through Customization
The ability to offer highly customized and personalized products sets companies apart from their competitors. By leveraging additive manufacturing’s capabilities, organizations can differentiate themselves and meet the unique needs of their customers.
Conclusion
Bringing additive manufacturing in-house offers numerous benefits for companies across various industries. From faster prototyping and product development to cost savings, enhanced customization, streamlined supply chain, improved product performance, increased innovation, and competitive advantage, the advantages of in-house 3D printing are substantial. As the technology continues to evolve and become more accessible, more organizations are likely to adopt additive manufacturing as a core part of their operations.
Frequently Asked Questions (FAQ)
1. What are the upfront costs associated with bringing additive manufacturing in-house?
The upfront costs of bringing additive manufacturing in-house include the purchase of 3D printing equipment, software, and materials. The cost can vary depending on the type and scale of the equipment required. Companies should also consider the cost of training personnel and setting up a dedicated additive manufacturing workspace.
2. How long does it take to implement additive manufacturing in-house?
The implementation timeline for bringing additive manufacturing in-house depends on various factors, such as the complexity of the equipment, the level of expertise within the organization, and the scale of the implementation. On average, it can take several months to fully integrate additive manufacturing into an organization’s operations.
3. What skills are required for in-house additive manufacturing?
To successfully implement and operate in-house additive manufacturing, companies need personnel with skills in 3D modeling, design for additive manufacturing (DfAM), material selection, and 3D printer operation and maintenance. Depending on the complexity of the applications, additional expertise in areas such as structural analysis and post-processing may be required.
4. Can additive manufacturing completely replace traditional manufacturing methods?
While additive manufacturing offers many advantages, it is not a complete replacement for traditional manufacturing methods. Additive manufacturing is particularly well-suited for low-volume production, complex geometries, and customized parts. However, for high-volume production and certain material requirements, traditional manufacturing methods may still be more cost-effective and efficient.
5. How can companies ensure the quality of parts produced through in-house additive manufacturing?
To ensure the quality of parts produced through in-house additive manufacturing, companies should implement robust quality control processes. This includes regular calibration and maintenance of 3D printing equipment, material testing, and post-process inspection. Establishing standard operating procedures (SOPs) and training personnel on best practices can also help maintain consistent quality across all additively manufactured parts.
Benefit | Description |
---|---|
Faster Prototyping and Product Development | Accelerate prototyping and product development by quickly creating physical prototypes from digital designs, allowing for rapid iteration and refinement. |
Cost Savings | Reduce tooling costs, lower inventory costs, and enable cost-effective low-volume production. |
Enhanced Customization and Personalization | Offer highly customized and personalized products to customers, leading to improved customer satisfaction and loyalty. |
Streamlined Supply Chain | Reduce reliance on external suppliers, shorten lead times, and gain greater control over the supply chain. |
Improved Product Performance | Create lightweight and optimized designs with improved performance characteristics, and consolidate multiple parts into single, integrated components. |
Increased Innovation and Creativity | Foster a culture of innovation and creativity by allowing designers and engineers to experiment with new ideas and concepts, and rapidly prototype and validate designs. |
Competitive Advantage | Gain a competitive edge by bringing products to market faster and differentiating through customization capabilities. |
Leave a Reply