Introduction to 6 Layer PCB Stackups
A 6 layer PCB stackup is a popular choice for complex electronic designs that require high signal integrity, power efficiency, and electromagnetic compatibility (EMC). By utilizing six conductive layers, designers can optimize the placement of signal, power, and ground planes to achieve the desired performance characteristics. This article will provide comprehensive guidelines for designing an effective 6 layer PCB stackup.
Understanding the Layers in a 6 Layer PCB
A typical 6 layer PCB stackup consists of the following layers:
- Top Layer (Signal)
- Ground Plane
- Signal Layer 1
- Power Plane
- Signal Layer 2
- Bottom Layer (Signal)
Each layer serves a specific purpose in the overall design of the PCB.
Top and Bottom Layers (Signal)
The top and bottom layers of a 6 layer PCB are primarily used for routing signal traces. These layers are exposed to the environment and are typically covered with a solder mask to protect the traces from damage and corrosion. Components are also placed on these layers, with the top layer being the most common placement area.
Ground and Power Planes
The ground and power planes in a 6 layer PCB serve as reference planes for the signal layers. The ground plane provides a low-impedance return path for the signals, while the power plane distributes the supply voltage to the components on the board. These planes also help to reduce electromagnetic interference (EMI) and improve signal integrity by minimizing the loop area between the signal traces and their return paths.
Signal Layers 1 and 2
Signal layers 1 and 2 are used for routing additional signal traces in a 6 layer PCB. These layers are sandwiched between the ground and power planes, which provide shielding and reduce crosstalk between the signal traces on different layers. By having two dedicated signal layers, designers can route more complex signal paths and achieve higher routing density.
Designing the 6 Layer PCB Stackup
When designing a 6 layer PCB stackup, several factors must be considered to ensure optimal performance and manufacturability. These include layer thickness, dielectric material selection, trace width and spacing, via design, and impedance control.
Layer Thickness and Dielectric Material Selection
The thickness of each layer in a 6 layer PCB stackup depends on the desired electrical characteristics and the manufacturing capabilities of the PCB fabricator. A typical stackup might have the following layer thicknesses:
Layer | Thickness (mil) | Dielectric Material |
---|---|---|
Top Layer | 1.4 | FR-4 |
Prepreg | 4.0 | FR-4 |
Ground Plane | 1.0 | Copper |
Core | 6.7 | FR-4 |
Signal Layer 1 | 1.0 | Copper |
Core | 6.7 | FR-4 |
Power Plane | 1.0 | Copper |
Core | 6.7 | FR-4 |
Signal Layer 2 | 1.0 | Copper |
Prepreg | 4.0 | FR-4 |
Bottom Layer | 1.4 | FR-4 |
The dielectric material used in the stackup is typically FR-4, a glass-reinforced epoxy laminate. FR-4 is widely used due to its good mechanical and electrical properties, as well as its cost-effectiveness. Other high-performance dielectric materials, such as Rogers or Isola, may be used in applications that require lower dielectric loss or higher thermal stability.
Trace Width and Spacing
The width and spacing of the signal traces on each layer must be carefully designed to achieve the desired impedance and to minimize crosstalk. The trace width and spacing are determined by factors such as the dielectric material, layer thickness, and the desired characteristic impedance (typically 50 ohms for single-ended traces and 100 ohms for differential pairs).
To calculate the trace width and spacing, designers can use online calculators or specialized PCB design software. These tools take into account the stackup parameters and the desired impedance to provide accurate trace dimensions.
Via Design
Vias are used to connect traces on different layers of the PCB. In a 6 layer PCB stackup, there are several types of vias that can be used, including through-hole vias, blind vias, and buried vias.
- Through-hole vias: These vias go through all layers of the PCB and are typically used for connecting components to the board or for routing signals between the top and bottom layers.
- Blind vias: These vias start from either the top or bottom layer and terminate on an internal layer. They are used for connecting signal traces on the outer layers to the inner layers.
- Buried vias: These vias connect two or more internal layers without reaching the outer layers. They are used for routing signals between the inner layers and can help to reduce the number of through-hole vias, which can improve signal integrity.
When designing vias, it is important to consider the via diameter, pad size, and anti-pad size. The via diameter should be large enough to ensure reliable plating and to minimize the resistance of the via. The pad size should be sufficient to accommodate the drilling and plating tolerances, while the anti-pad size should be large enough to prevent shorts between the via and the surrounding planes.
Impedance Control
Controlling the impedance of the signal traces is critical for maintaining signal integrity and preventing reflections and other signal distortions. In a 6 layer PCB stackup, impedance control is achieved by carefully selecting the trace width, spacing, and dielectric thickness to match the desired characteristic impedance.
There are two main types of impedance control: single-ended and differential. Single-ended impedance control is used for traces that carry a signal referenced to ground, while differential impedance control is used for pairs of traces that carry differential signals.
To achieve accurate impedance control, designers must work closely with the PCB fabricator to ensure that the stackup parameters are precisely controlled during the manufacturing process. This may involve specifying tight tolerances on the dielectric thickness and copper weight, as well as performing impedance testing on sample boards to verify the impedance values.
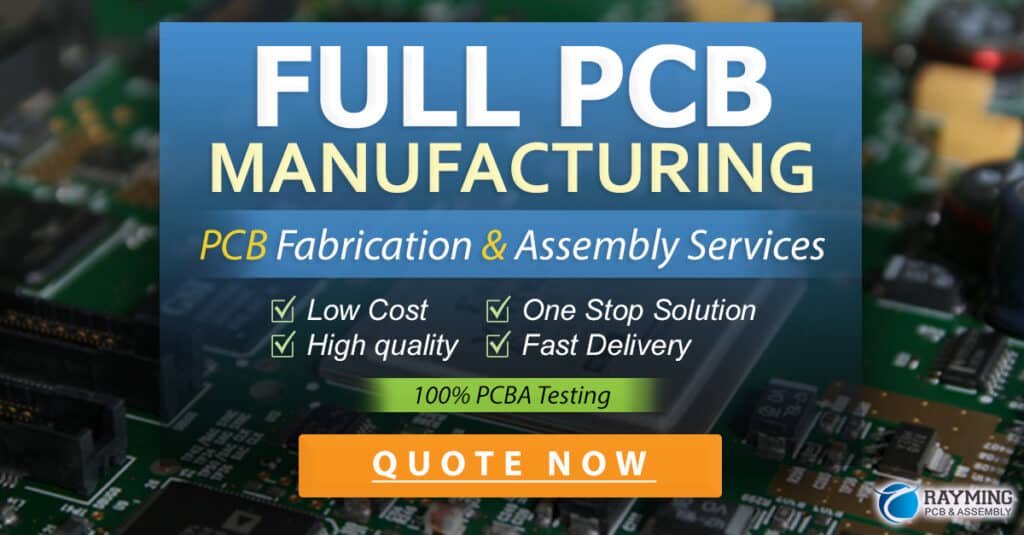
6 Layer PCB Stackup Example
Here is an example of a typical 6 layer PCB stackup with impedance-controlled traces:
Layer | Thickness (mil) | Material | Impedance (ohms) |
---|---|---|---|
Top Layer | 1.4 | FR-4 | 50 (single-ended) |
Prepreg | 4.0 | FR-4 | – |
Ground Plane | 1.0 | Copper | – |
Core | 6.7 | FR-4 | – |
Signal Layer 1 | 1.0 | Copper | 100 (differential) |
Core | 6.7 | FR-4 | – |
Power Plane | 1.0 | Copper | – |
Core | 6.7 | FR-4 | – |
Signal Layer 2 | 1.0 | Copper | 100 (differential) |
Prepreg | 4.0 | FR-4 | – |
Bottom Layer | 1.4 | FR-4 | 50 (single-ended) |
In this example, the top and bottom layers have single-ended traces with a characteristic impedance of 50 ohms, while the internal signal layers have differential pairs with a characteristic impedance of 100 ohms. The ground and power planes provide shielding and reference planes for the signal traces, and the core and prepreg layers provide the necessary dielectric thickness to achieve the desired impedance values.
Frequently Asked Questions (FAQ)
-
Q: What are the benefits of using a 6 layer PCB stackup?
A: A 6 layer PCB stackup offers several benefits, including improved signal integrity, better power distribution, increased routing density, and enhanced EMC performance. By having dedicated signal, ground, and power layers, designers can optimize the placement of traces and components to achieve the desired performance characteristics. -
Q: Can I use different dielectric materials in a 6 layer PCB stackup?
A: Yes, designers can use different dielectric materials in a 6 layer PCB stackup to achieve specific performance requirements. For example, high-speed designs may benefit from using low-loss dielectric materials such as Rogers or Isola in the signal layers, while the core and prepreg layers can use standard FR-4 material. -
Q: How do I choose the right trace width and spacing for my 6 layer PCB design?
A: The trace width and spacing depend on several factors, including the desired impedance, the dielectric material, and the layer thickness. Designers can use online calculators or PCB design software to determine the appropriate trace dimensions based on these parameters. It is important to work closely with the PCB fabricator to ensure that the chosen trace width and spacing are manufacturable and will yield the desired impedance values. -
Q: What is the difference between blind and buried vias in a 6 layer PCB stackup?
A: Blind vias start from either the top or bottom layer and terminate on an internal layer, while buried vias connect two or more internal layers without reaching the outer layers. Blind vias are used for connecting signal traces on the outer layers to the inner layers, while buried vias are used for routing signals between the inner layers and can help to reduce the number of through-hole vias. -
Q: How can I ensure accurate impedance control in my 6 layer PCB stackup?
A: To ensure accurate impedance control, designers must carefully select the trace width, spacing, and dielectric thickness to match the desired characteristic impedance. They must also work closely with the PCB fabricator to ensure that the stackup parameters are precisely controlled during the manufacturing process, including specifying tight tolerances on the dielectric thickness and copper weight and performing impedance testing on sample boards to verify the impedance values.
Conclusion
Designing a 6 layer PCB stackup requires careful consideration of various factors, including layer thickness, dielectric material selection, trace width and spacing, via design, and impedance control. By following the guidelines outlined in this article and working closely with the PCB fabricator, designers can create an optimized 6 layer PCB stackup that delivers the desired performance characteristics for their specific application.
When designing a 6 layer PCB, it is essential to consider the unique requirements of the project, such as signal speed, power distribution, and EMC performance. By leveraging the benefits of a 6 layer stackup, such as dedicated signal, ground, and power layers, designers can create complex and high-performance electronic systems that meet the demands of modern applications.
Leave a Reply