Introduction to 6 Layer PCB Design
Six layer printed circuit boards (PCBs) provide increased routing flexibility and signal integrity compared to simpler 2 or 4 layer boards. The additional inner layers allow for more complex designs and better isolation of critical signals. However, proper design techniques are essential to realize the full benefits of a 6 layer stackup.
In this article, we’ll dive into the best practices and guidelines for designing high-performance 6 layer PCBs. From choosing the right layer arrangement to managing return paths and avoiding EMI, you’ll learn actionable tips to optimize your next 6 layer PCB design. Let’s get started!
Advantages of Using a 6 Layer PCB
Before we look at specific design guidelines, it’s important to understand the key advantages of 6 layer PCBs and when to choose this type of stackup. Here are the main benefits compared to 2 or 4 layer boards:
- More routing space and flexibility
- Ability to isolate sensitive signals on dedicated layers
- Lower crosstalk and electromagnetic interference (EMI)
- Improved power integrity with dedicated power and ground planes
- Better thermal management and mechanical strength
A 6 layer PCB is ideal for designs with:
– High component density
– Many power rails or supply voltages
– High-speed digital interfaces like DDR RAM or PCIe
– Sensitive analog or RF circuits
– Strict EMI requirements
If your design fits any of the above criteria, using a 6 layer stackup will help you achieve better performance, reliability, and manufacturability. Now let’s look at how to choose the optimal layer stackup.
Choosing the Best 6 Layer PCB Stackup
The layer arrangement, or stackup, is one of the most important design choices for a 6 layer PCB. It determines which layers are used for signals, power, and ground. Here is a common 6 layer stackup:
Layer | Usage |
---|---|
Top | Signals, components |
L2 | Ground plane |
L3 | Signals |
L4 | Power plane |
L5 | Signals |
Bottom | Signals, components |
In this stackup:
– Signal layers are alternated with power/ground layers to provide constant reference planes and reduce crosstalk
– The ground layer (L2) is placed close to the top to provide a low-inductance return path for signals
– Power (L4) is in the middle to minimize IR drop
– Two inner signal layers (L3, L5) provide ample routing space
– Planes separate groups of signal layers to reduce layer-to-layer crosstalk
This is a tried-and-true stackup that works well for many designs. However, the optimal arrangement depends on the specific needs of your PCB. For example:
- If EMI is a major concern, you may opt for a stackup that has power or ground on the outer layers to provide additional shielding
- For a board with many supply voltages, you can use two or more layers as power planes and segment them as needed
- In some cases it’s preferable to put the two signal layers adjacent to each other in the middle for easier routing of buses
The table below shows some common 6 layer stackups and their typical applications:
L1 | L2 | L3 | L4 | L5 | L6 | Applications |
---|---|---|---|---|---|---|
Signal | Ground | Signal | Power | Signal | Signal | General purpose |
Ground | Signal | Ground | Power | Signal | Signal | EMI-sensitive |
Signal | Ground | Power | Signal | Power | Signal | Multiple voltages |
Signal | Signal | Ground | Signal | Signal | Power | High-speed buses |
When choosing a stackup, also consider the PCB material and thickness. The dielectric constant of the material determines the impedance of traces, while the thickness affects both impedance and crosstalk. Work with your manufacturer to select a stackup and material that meets your electrical and mechanical requirements.
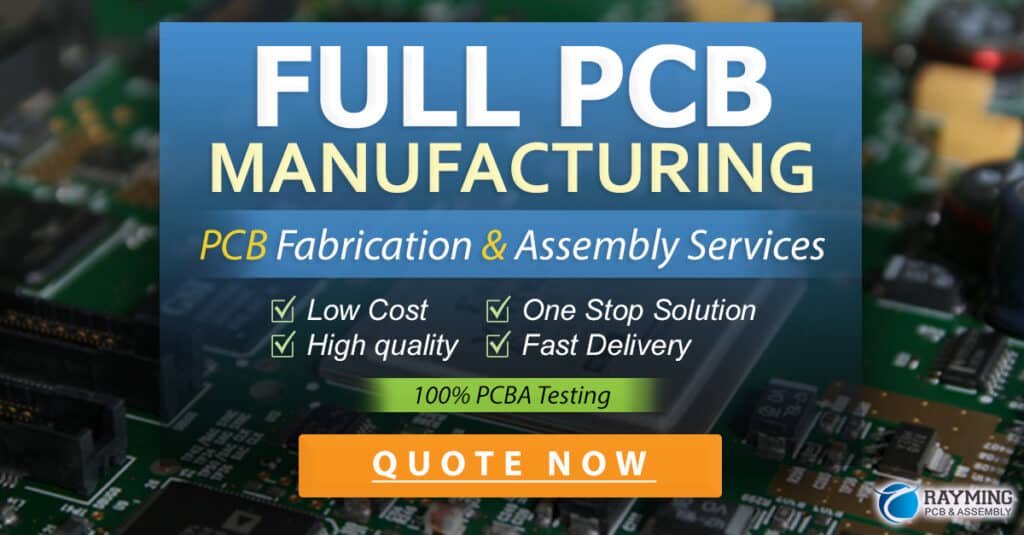
Best Practices for Signal Routing on 6 Layer PCBs
Proper signal routing is critical to maintaining signal integrity and avoiding issues like crosstalk, reflections, and EMI. Here are some guidelines to follow when routing signals on a 6 layer PCB:
Keep Signal Traces Short and Direct
- Route signals as directly as possible between source and destination
- Avoid unnecessary jogs, meanders, or vias that increase trace length
- Place components to minimize distance between connected pins
Shorter traces have lower resistance, inductance, and capacitance, which all help maintain signal quality. They are also less prone to picking up noise or interference.
Maintain Controlled Impedance
- Route critical signals on layers adjacent to uninterrupted reference planes
- Avoid crossing split planes or changing reference layers unnecessarily
- Use the PCB stackup impedance calculator to determine trace width and spacing
- Keep trace width and spacing consistent along the length of a signal
Controlled impedance is essential for high-speed and sensitive signals to avoid reflections, ringing, and signal distortion. Having a continuous reference plane beneath the signal layer ensures a low-impedance return path.
Minimize Crosstalk
- Route critical signals on separate layers from potential aggressors
- Provide adequate spacing between signal traces
- Avoid routing parallel bus lines on adjacent layers
- Use ground guard traces or pours between sensitive signals
Crosstalk occurs when signals couple energy into each other through electric and magnetic fields. Increasing the spacing between traces and avoiding broadside coupling between layers helps reduce crosstalk.
Optimize Via Usage
- Use minimum size vias to reduce capacitance and stub effects
- Avoid unnecessary layer transitions and keep vias short
- Provide sufficient clearance around vias for manufacturability
- Consider blind or buried vias for dense designs
Vias are essential for routing signals between layers, but they can also degrade signal quality if used improperly. The stub portion of a through-hole via acts like an antenna and can cause reflections or EMI.
Minimize Loop Area
- Route signals and their return paths close together
- Use ground pour or gridded reference planes
- Avoid split planes under critical signals
- Provide stitching vias to connect reference planes
The current loop formed by a signal and its return path is a key determinant of inductance and EMI radiation. Minimizing the loop area by providing nearby return paths reduces these effects.
By following these routing best practices and working within the constraints of your 6 layer stackup, you can ensure high-quality signal transmission and minimize signal integrity issues.
Power Integrity Considerations for 6 Layer PCBs
In addition to signal integrity, power integrity is another key aspect of 6 layer PCB design. Power distribution networks (PDNs) must provide clean, stable power to all the components on the board. Here are some tips for maintaining power integrity:
Use Solid Power and Ground Planes
- Dedicate entire layers to power and ground when possible
- Avoid splitting planes or cutting off return paths
- Connect planes with stitching vias near connectors and components
Solid reference planes have much lower impedance than narrow traces, so they can supply high transient currents without significant voltage drop. They also minimize loop area and radiation.
Decouple Power Supplies
- Place decoupling capacitors close to ICs and connectors
- Use multiple capacitor values to cover different frequency ranges
- Connect capacitors to power and ground planes with short, wide traces
- Simulate the PDN impedance to determine the number and values of capacitors
Decoupling capacitors supply transient current and filter high-frequency noise on power rails. They should be placed as close as possible to the pins of ICs to minimize connection inductance.
Partition Power Planes
- Create separate regions or layers for different supply voltages
- Isolate analog and digital power supplies to prevent noise coupling
- Provide adequate clearance between power regions
- Connect planes together at a single point to avoid ground loops
In mixed-signal designs or boards with multiple supply voltages, it’s important to isolate power planes to prevent noise from coupling between them. Digital switching noise can easily contaminate sensitive analog circuits.
Size Traces for Current Capacity
- Determine expected current draw for each power net
- Use IPC-2152 charts or calculator to size traces and planes
- Consider temperature rise and voltage drop requirements
- Provide additional copper for high-current nets like battery charging or motor drivers
Power traces and planes must be sized appropriately to handle the maximum expected current without excessive voltage drop or temperature rise. Undersized traces can lead to reliability issues or even catastrophic failures.
By designing a robust PDN and following these power integrity guidelines, you can ensure that your 6 layer PCB has clean, stable power delivery to all components. This is essential for reliable operation and optimal performance.
EMI Reduction Techniques for 6 Layer PCBs
Electromagnetic interference (EMI) is a common challenge in PCB design, especially for boards with high-speed digital interfaces or sensitive analog circuits. Here are some techniques to minimize EMI in 6 layer PCBs:
Use Proper Grounding Techniques
- Provide low-impedance return paths for all signals
- Use ground planes instead of traces whenever possible
- Stitch ground planes together with vias near connectors and components
- Avoid split ground planes or slots that force return currents to take long paths
Good grounding is perhaps the most important factor in reducing EMI. Signals should always have a nearby return path to minimize loop area and prevent them from radiating.
Filter Inputs and Outputs
- Use LC filters or ferrite beads on cable connections
- Place filters close to connectors or edge of board
- Use series termination resistors on high-speed signals
- Add ESD protection diodes on sensitive inputs
Cables and connectors are common paths for EMI to enter or exit a PCB. Filtering these interfaces helps prevent the board from both radiating and receiving interference.
Minimize Loop Area
- Follow the routing best practices mentioned earlier to keep signal and return paths close together
- Use ground pours on outer layers to provide additional shielding
- Route differential pairs tightly coupled to each other
- Avoid unnecessarily long or meandering traces
As mentioned before, minimizing loop area is key to reducing both radiation and susceptibility to EMI. This applies to both signal traces and power distribution networks.
Use Shielding Techniques
- Place sensitive circuits away from potential sources of interference
- Use shielding cans or conductive tape over critical components
- Place power and ground layers on the outer layers of the PCB for additional shielding
- Use guard traces or copper pours to isolate sensitive signals
In some cases, it may be necessary to provide additional shielding beyond what the PCB stackup can provide. Metallic shields or even conductive tape can help block electric fields from coupling into sensitive circuits.
Optimize Component Placement
- Group components by function and place them close together
- Keep high-speed digital components away from sensitive analog circuits
- Orient components to minimize coupling between them
- Place decoupling capacitors close to ICs and connectors
Proper component placement can help reduce EMI by minimizing the distance that signals have to travel and preventing coupling between different circuit blocks. It’s also important for maintaining signal integrity and power integrity.
By using a combination of these EMI reduction techniques and following good PCB design practices, you can minimize both radiated and conducted emissions from your 6 layer board. This will help you pass EMC testing and ensure reliable operation in the intended environment.
Thermal Management in 6 Layer PCBs
Thermal management is another important consideration in 6 layer PCB design, especially for boards with high power dissipation or densely packed components. Here are some tips for managing heat in your PCB:
Use Copper Pours for Heat Spreading
- Place large copper pours on outer layers near heat-generating components
- Connect pours to inner power or ground planes with thermal vias
- Use thicker copper weights (2 oz or more) for better thermal conductivity
Copper is an excellent thermal conductor, so using large copper pours can help spread heat away from hot components. These pours should be connected to inner planes with plenty of thermal vias to provide a low-resistance path for heat transfer.
Optimize Component Placement for Thermal Management
- Place high-power components near the edges of the board for better airflow
- Provide adequate spacing between hot components to prevent thermal coupling
- Orient components to maximize heat transfer to thermal pours or planes
Proper component placement is important for thermal management as well as signal integrity and EMI. Hot components should be spaced out as much as possible and placed in areas with good airflow.
Use Thermal Reliefs on Pads
- Provide thermal relief connections on pads for easier soldering
- Use a spoke or web style relief instead of a solid connection
- Ensure that reliefs are large enough to allow adequate heat transfer
Thermal reliefs are necessary to prevent heat from being drawn away from pads during soldering, which can lead to poor solder joints. However, they also reduce the thermal conductivity between the pad and the surrounding copper pour. A balance must be struck between solderability and heat transfer.
Consider External Cooling Methods
- Use heatsinks or heat spreaders on high-power components
- Provide mounting holes for fans or other active cooling devices
- Consider using thermally conductive adhesives or gap pads
In some cases, the PCB alone may not be able to dissipate enough heat to keep components within their safe operating limits. External cooling methods such as heatsinks, fans, or even liquid cooling may be necessary. The PCB should be designed with provisions for mounting these devices.
By following these thermal management guidelines and carefully considering the heat dissipation requirements of your components, you can ensure that your 6 layer PCB operates reliably even under heavy thermal loads. Proper thermal design is essential for long-term reliability and performance.
Designing for Manufacturing (DFM) in 6 Layer PCBs
Designing a 6 layer PCB that works well electrically is only half the battle – it also needs to be manufacturable at scale and with good yield. Here are some key DFM considerations for 6 layer boards:
Follow Manufacturer’s Design Rules
- Consult with your PCB fabricator early in the design process
- Obtain their detailed design rules and constraints for 6 layer boards
- Follow rules for minimum trace/space, via size, annular ring, etc.
- Verify that your design meets all manufacturability requirements
Each PCB manufacturer has their own specific design rules and capabilities, so it’s important to engage with them early and ensure that your design is compatible with their processes. Failing to follow these rules can lead to delays, extra costs, or even non-functional boards.
Use Standard Sizes and Shapes
- Stick to standard PCB sizes and aspect ratios when possible
- Avoid odd shapes or cutouts that require special tooling
- Use rectangular boards with straight edges and rounded corners
- Place components and connectors away from edges to prevent damage
Using standard sizes and shapes helps reduce manufacturing costs and lead times, as the fabricator can use existing tooling and processes. Odd shapes or sizes may require custom tooling or special handling, which adds expense and risk.
Optimize Panelization
- Design your board to fit efficiently on a standard panel size
- Provide adequate spacing between boards for depanelization
- Use mouse bites or V-grooves for easy separation of boards
- Consider using a frame or rails for additional support during assembly
Panelization is the process of arranging multiple copies of a PCB on a larger panel for production. Efficient panelization helps reduce costs and improve yields by minimizing wasted material and allowing for easier handling and testing.
Provide Adequate Clearances
- Ensure that there is sufficient clearance between components, traces, and vias
- Follow manufacturer’s guidelines for pad and via sizes and spacings
- Provide additional clearance around connectors and mechanical features
- Consider the tolerances and variability of the manufacturing process
Proper clearances are essential for reliable manufacturing and assembly of PCBs. Insufficient clearances can lead to short circuits, solder bridges, or mechanical interference between components.
Use dfm analysis Tools
- Run your design through a DFM analysis tool before sending it to the manufacturer
- Check for common issues like acid traps, slivers, or insufficient clearances
- Verify that your design meets all manufacturing constraints and guidelines
- Make any necessary changes to improve manufacturability and yield
Many PCB design tools include built-in DFM analysis features that can catch common manufacturability issues early in the design process. These tools can save time and money by identifying problems before the design is sent to the fabricator.
By following these DFM guidelines and working closely with your PCB manufacturer, you can ensure that your 6 layer design is not only electrically sound but also easy and cost-effective to manufacture at scale. A little extra effort in the design phase can save a lot of headaches and expenses down the road.
Conclusion
Designing a high-quality 6 layer PCB requires careful consideration of signal integrity, power integrity, EMI, thermal management, and manufacturability. By following the guidelines and best practices outlined in this article, you can create 6 layer designs that perform well electrically and are also cost-effective and reliable to manufacture.
Remember to:
– Choose an appropriate 6 layer stackup for your design requirements
– Follow best practices for signal routing and power distribution
– Use EMI reduction techniques to minimize interference and noise
– Consider thermal management and use copper pours and thermal vias effectively
– Follow DFM guidelines and work closely with your PCB manufacturer
By taking a holistic approach to PCB design and considering all of these factors together, you can unlock the full potential of 6 layer PCB
Leave a Reply