Understanding the Importance of PCB Hole Size Tolerance
PCB hole size tolerance is a critical aspect of PCB design and manufacturing. It directly impacts the fit and function of components, such as through-hole components, vias, and mounting holes. Properly specified hole size tolerances ensure that components can be easily inserted and soldered, while maintaining reliable electrical connections.
Hole size tolerances are typically expressed as a nominal diameter with a +/- tolerance. For example, a hole size specification of 0.8mm +/-0.05mm means that the acceptable range of hole diameters is between 0.75mm and 0.85mm.
Consequences of Incorrect Hole Size Tolerances
Incorrectly specified hole size tolerances can lead to various problems during PCB assembly and operation:
- Difficulty inserting components: If the holes are too small, it may be challenging or impossible to insert components without damaging them or the PCB.
- Poor solderability: Holes that are too large can result in insufficient solder joint formation, leading to weak or unreliable connections.
- Alignment issues: Inconsistent hole sizes can cause misalignment of components, affecting the overall board layout and functionality.
- Stress on components: Forcibly inserting components into holes that are too small can put undue stress on the components, potentially causing damage or premature failure.
Tip 1: Consider Component Specifications
When specifying PCB hole size tolerances, it is essential to consider the specifications of the components that will be used on the board. Different components have varying lead diameters and tolerances, which must be accounted for when determining the appropriate hole sizes.
Through-Hole Component Lead Diameters
Through-hole components, such as resistors, capacitors, and connectors, have leads that are inserted into the PCB holes and soldered in place. The lead diameters of these components can vary depending on the component package and size.
Common through-hole component lead diameters and their typical hole size recommendations:
Component Package | Lead Diameter | Recommended Hole Size |
---|---|---|
Axial-lead | 0.5mm – 0.8mm | 0.8mm – 1.0mm |
Radial-lead | 0.5mm – 0.8mm | 0.8mm – 1.0mm |
TO-220 | 0.8mm – 1.0mm | 1.2mm – 1.5mm |
DIP | 0.4mm – 0.6mm | 0.7mm – 0.9mm |
Connector Pin Diameters
Connectors, such as header pins, socket pins, and terminal blocks, also have specific pin diameters that must be considered when specifying hole sizes.
Common connector pin diameters and their typical hole size recommendations:
Connector Type | Pin Diameter | Recommended Hole Size |
---|---|---|
2.54mm pitch | 0.6mm – 0.8mm | 0.9mm – 1.1mm |
2.00mm pitch | 0.4mm – 0.6mm | 0.7mm – 0.9mm |
1.27mm pitch | 0.3mm – 0.5mm | 0.6mm – 0.8mm |
Tip 2: Follow Manufacturing Capabilities and Limitations
PCB manufacturers have specific capabilities and limitations when it comes to drilling holes. It is essential to understand these constraints and design your PCB accordingly to ensure manufacturability and minimize costs.
Minimum Hole Size
PCB manufacturers have a minimum hole size that they can reliably drill. This minimum hole size depends on the manufacturing process, equipment, and the PCB material. Typically, the minimum hole size ranges from 0.2mm to 0.3mm. Attempting to specify hole sizes smaller than the manufacturer’s minimum can result in increased costs or manufacturing issues.
Aspect Ratio
The aspect ratio of a hole refers to the ratio of the hole depth to its diameter. PCB manufacturers have limitations on the maximum aspect ratio they can achieve. A common maximum aspect ratio is 8:1, meaning that the hole depth cannot exceed eight times its diameter. Designing holes with aspect ratios greater than the manufacturer’s capability can lead to drilling difficulties and inconsistencies.
Hole Tolerance Capabilities
Different PCB manufacturers have varying capabilities when it comes to hole size tolerances. Some manufacturers may be able to achieve tighter tolerances than others. It is essential to communicate with your chosen PCB manufacturer to understand their specific hole tolerance capabilities and design your PCB accordingly.
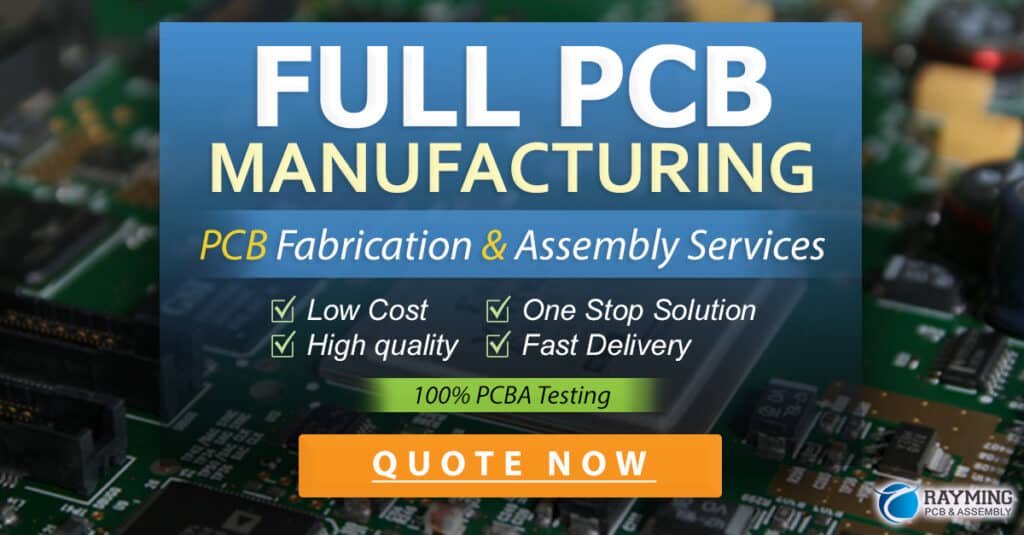
Tip 3: Use Appropriate Hole Size Tolerances for Different Applications
The required hole size tolerances can vary depending on the specific application and the type of components being used. It is important to consider the functional requirements of your PCB and specify hole size tolerances that meet those needs.
General-Purpose Applications
For general-purpose applications, where the components have standard lead diameters and tolerances, a hole size tolerance of +/-0.05mm to +/-0.1mm is usually sufficient. This tolerance range allows for easy insertion of components while maintaining reliable electrical connections.
High-Precision Applications
In high-precision applications, such as those involving fine-pitch components or high-density layouts, tighter hole size tolerances may be necessary. In these cases, a hole size tolerance of +/-0.025mm to +/-0.05mm is recommended. Tighter tolerances ensure proper component fit and minimize the risk of assembly issues.
Plated vs. Non-Plated Holes
Plated holes, which have a conductive metal coating on the hole walls, generally require tighter tolerances compared to non-plated holes. This is because the plating process can slightly reduce the hole diameter, and the plating thickness must be accounted for when specifying the hole size.
For plated holes, a tolerance of +/-0.05mm to +/-0.075mm is common, while for non-plated holes, a tolerance of +/-0.1mm to +/-0.15mm is generally acceptable.
Tip 4: Communicate Clearly with Your PCB Manufacturer
Clear communication with your PCB manufacturer is crucial to ensure that your hole size tolerances are properly understood and implemented. Provide detailed information about your requirements and any specific considerations for your PCB design.
Include Hole Size Tolerances in Your Documentation
When creating your PCB design files and documentation, make sure to clearly specify the hole size tolerances for each type of hole on your board. This includes through-hole component holes, vias, and mounting holes. Use clear and consistent notation, such as “+/-0.05mm,” to avoid any ambiguity.
Discuss Your Requirements with the Manufacturer
Before finalizing your PCB design, discuss your hole size tolerance requirements with your chosen PCB manufacturer. They can provide valuable insights and recommendations based on their specific capabilities and experience. This collaboration can help you optimize your design for manufacturability and ensure that your hole size tolerances are achievable.
Request a Design for Manufacturability (DFM) Review
Many PCB manufacturers offer Design for Manufacturability (DFM) review services. These reviews involve analyzing your PCB design files to identify any potential manufacturing issues, including hole size tolerance concerns. Requesting a DFM review can help catch and address any problems early in the design process, saving time and costs in the long run.
Tip 5: Allow for Proper Hole-to-Copper Clearance
When specifying hole size tolerances, it is important to consider the clearance between the holes and the surrounding copper features on the PCB. Adequate hole-to-copper clearance helps ensure proper electrical insulation and prevents short circuits.
Minimum Hole-to-Copper Clearance
The minimum hole-to-copper clearance depends on the PCB manufacturing process and the voltage requirements of your circuit. As a general rule, a minimum clearance of 0.25mm to 0.5mm is recommended between the edge of a hole and any adjacent copper feature.
Pad Size Considerations
When designing component pads, make sure to account for the hole size tolerance and provide sufficient pad diameter to accommodate the hole. The pad diameter should be larger than the maximum possible hole diameter, considering the tolerance. This ensures that there is enough copper around the hole for proper soldering and electrical connection.
A common guideline is to design the pad diameter to be at least 0.5mm larger than the maximum hole diameter. For example, if the hole size tolerance is +/-0.1mm and the nominal hole diameter is 0.8mm, the pad diameter should be at least 1.4mm (0.8mm + 0.1mm + 0.5mm).
Frequently Asked Questions (FAQ)
-
What is PCB hole size tolerance, and why is it important?
PCB hole size tolerance refers to the acceptable range of diameters for drilled holes in a printed circuit board. It is important because it directly affects the fit and function of components, as well as the reliability of electrical connections. -
How are hole size tolerances typically specified?
Hole size tolerances are typically specified as a nominal diameter with a +/- tolerance. For example, a hole size specification of 0.8mm +/-0.05mm means that the acceptable range of hole diameters is between 0.75mm and 0.85mm. -
What are the consequences of incorrectly specified hole size tolerances?
Incorrectly specified hole size tolerances can lead to problems such as difficulty inserting components, poor solderability, alignment issues, and stress on components. These issues can impact the assembly process and the overall functionality of the PCB. -
How do I determine the appropriate hole size tolerances for my components?
To determine the appropriate hole size tolerances, consider the specifications of the components you will be using, such as through-hole component lead diameters and connector pin diameters. Refer to component datasheets and recommendations for typical hole sizes based on the component package and size. -
What should I do if I’m unsure about the hole size tolerances for my PCB design?
If you are unsure about the hole size tolerances for your PCB design, communicate with your chosen PCB manufacturer. Discuss your requirements and seek their guidance based on their specific capabilities and experience. Requesting a Design for Manufacturability (DFM) review can also help identify any potential issues and ensure that your hole size tolerances are suitable for manufacturing.
Conclusion
Specifying appropriate PCB hole size tolerances is essential for ensuring proper component fit, reliable electrical connections, and overall board functionality. By considering component specifications, manufacturing capabilities, and the specific requirements of your application, you can determine the optimal hole size tolerances for your PCB design.
Remember to communicate clearly with your PCB manufacturer, provide detailed documentation, and allow for proper hole-to-copper clearance. By following these tips and collaborating with your manufacturer, you can achieve a successful PCB design that meets your performance and reliability goals.
Leave a Reply