Introduction
Printed Circuit Boards (PCBs) are the backbone of modern electronic devices. From smartphones to medical equipment, PCBs play a crucial role in ensuring the proper functioning and reliability of these devices. As a PCB designer, it is essential to stay updated with the latest design facts and trends to create efficient and cost-effective PCBs. In this article, we will discuss five crucial PCB design facts that your boss needs to know to make informed decisions and stay ahead of the competition.
PCB Design Fact #1: Proper Component Placement is Key
The Importance of Component Placement
One of the most critical aspects of PCB design is component placement. Proper component placement ensures that the PCB functions as intended, minimizes signal interference, and facilitates efficient manufacturing. Poor component placement can lead to various issues, such as:
- Signal integrity problems
- Increased electromagnetic interference (EMI)
- Difficulties in PCB assembly
- Higher manufacturing costs
Best Practices for Component Placement
To optimize component placement, consider the following best practices:
- Group related components together to minimize signal path lengths and reduce interference.
- Place sensitive components, such as high-speed devices or analog circuits, away from potential sources of interference.
- Ensure adequate spacing between components to facilitate PCB assembly and allow for proper heat dissipation.
- Consider the mechanical constraints of the PCB, such as connectors and mounting holes, when placing components.
Component Type | Placement Consideration |
---|---|
High-speed devices | Away from potential sources of interference |
Analog circuits | Separated from digital circuits |
Power components | Close to power input and with adequate heat dissipation |
Connectors | Easily accessible and aligned with mechanical constraints |
By following these best practices, you can create PCBs with optimal component placement, leading to improved performance, reliability, and manufacturability.
PCB Design Fact #2: Signal Integrity is Essential
Understanding Signal Integrity
Signal integrity refers to the ability of a PCB to maintain the quality and timing of electrical signals as they travel through the board. Poor signal integrity can lead to various issues, such as:
- Signal distortion and attenuation
- Crosstalk between adjacent traces
- Electromagnetic interference (EMI)
- Timing errors and synchronization issues
Techniques for Improving Signal Integrity
To ensure good signal integrity, consider the following techniques:
- Use appropriate trace routing techniques, such as avoiding sharp angles and minimizing trace lengths.
- Implement proper grounding and shielding to reduce EMI and crosstalk.
- Use appropriate trace widths and spacing based on the signal frequencies and currents.
- Employ impedance matching techniques to minimize signal reflections and distortions.
- Use simulation tools to analyze and optimize signal integrity during the design process.
Signal Type | Trace Width | Trace Spacing |
---|---|---|
High-speed digital | 0.1 mm – 0.2 mm | 0.2 mm – 0.3 mm |
Low-speed digital | 0.2 mm – 0.4 mm | 0.3 mm – 0.5 mm |
Analog | 0.2 mm – 0.5 mm | 0.5 mm – 1.0 mm |
Power | 0.5 mm – 2.0 mm | 1.0 mm – 3.0 mm |
By implementing these techniques and following the appropriate guidelines for trace widths and spacing, you can create PCBs with excellent signal integrity, ensuring reliable performance and minimizing potential issues.
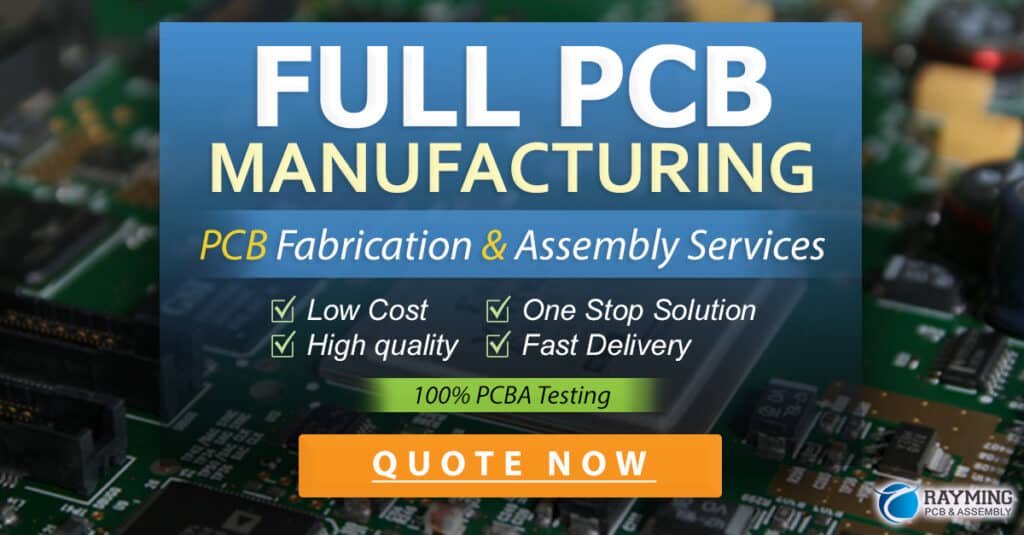
PCB Design Fact #3: Thermal Management is Crucial
The Importance of Thermal Management
Thermal management is a critical aspect of PCB design, as it ensures that the components on the board operate within their specified temperature ranges. Poor thermal management can lead to various problems, such as:
- Reduced component lifespan
- Decreased performance and reliability
- Increased risk of component failure
- Potential safety hazards
Thermal Management Techniques
To effectively manage heat dissipation on a PCB, consider the following techniques:
- Use appropriate heat sinks and thermal pads to dissipate heat from high-power components.
- Incorporate thermal vias to transfer heat from components to the PCB’s internal layers or the opposite side of the board.
- Use copper pours and planes to distribute heat evenly across the PCB.
- Consider the use of thermal interface materials (TIMs) to improve heat transfer between components and heat sinks.
- Perform thermal simulations to identify potential hot spots and optimize the PCB layout accordingly.
Component Power Dissipation | Thermal Management Technique |
---|---|
Low (< 0.5 W) | Copper pours and planes |
Medium (0.5 W – 2 W) | Thermal vias and copper pours |
High (> 2 W) | Heat sinks, thermal pads, and thermal vias |
By implementing appropriate thermal management techniques based on the power dissipation of the components, you can create PCBs that operate reliably and safely, even under demanding conditions.
PCB Design Fact #4: DFM Considerations are Essential
Understanding Design for Manufacturability (DFM)
Design for Manufacturability (DFM) is the practice of designing PCBs in a way that optimizes their manufacturability, ensuring that they can be efficiently and cost-effectively produced. Poor DFM can lead to various issues, such as:
- Increased manufacturing costs
- Longer production times
- Higher defect rates
- Reduced product quality and reliability
DFM Best Practices
To ensure that your PCB designs are optimized for manufacturability, consider the following best practices:
- Follow the manufacturer’s design guidelines and constraints, such as minimum trace widths, spacing, and hole sizes.
- Use standard component sizes and packages whenever possible to reduce costs and improve availability.
- Incorporate appropriate clearances and tolerances to account for manufacturing variations.
- Avoid complex or unconventional PCB shapes and features that may be difficult or expensive to manufacture.
- Communicate with your manufacturer early in the design process to identify potential DFM issues and incorporate their feedback.
PCB Feature | Minimum Value |
---|---|
Trace width | 0.1 mm |
Trace spacing | 0.1 mm |
Hole size | 0.2 mm |
Annular ring | 0.05 mm |
By following these DFM best practices and adhering to the manufacturer’s guidelines, you can create PCB designs that are easier and more cost-effective to manufacture, resulting in higher-quality products and shorter time-to-market.
PCB Design Fact #5: Collaboration and Communication are Key
The Importance of Collaboration and Communication
PCB design is a collaborative process that involves multiple stakeholders, including designers, engineers, manufacturers, and clients. Effective collaboration and communication are essential for ensuring that the final product meets all requirements and expectations. Poor collaboration and communication can lead to various issues, such as:
- Misaligned design goals and priorities
- Delays in the design and manufacturing process
- Increased costs due to rework and redesigns
- Reduced product quality and customer satisfaction
Best Practices for Collaboration and Communication
To foster effective collaboration and communication in the PCB design process, consider the following best practices:
- Establish clear lines of communication between all stakeholders, including regular meetings and progress updates.
- Use a centralized project management system to track tasks, deadlines, and deliverables.
- Implement version control and documentation practices to ensure that all team members are working with the most up-to-date information.
- Encourage open and transparent communication, allowing team members to share ideas, concerns, and feedback.
- Regularly review and validate design decisions with all relevant stakeholders to ensure alignment and consensus.
Stakeholder | Communication Frequency |
---|---|
Design team | Daily |
Engineering team | Weekly |
Manufacturing team | Bi-weekly |
Clients | Monthly |
By prioritizing collaboration and communication throughout the PCB design process, you can ensure that all stakeholders are aligned, informed, and working towards a common goal, resulting in a more efficient and successful project outcome.
Frequently Asked Questions (FAQ)
-
Q: What is the importance of proper component placement in PCB design?
A: Proper component placement ensures that the PCB functions as intended, minimizes signal interference, and facilitates efficient manufacturing. It helps to reduce signal integrity problems, electromagnetic interference, and difficulties in PCB assembly, while also lowering manufacturing costs. -
Q: How can I improve signal integrity in my PCB designs?
A: To improve signal integrity, use appropriate trace routing techniques, implement proper grounding and shielding, use appropriate trace widths and spacing, employ impedance matching techniques, and use simulation tools to analyze and optimize signal integrity during the design process. -
Q: Why is thermal management crucial in PCB design?
A: Thermal management is crucial because it ensures that the components on the board operate within their specified temperature ranges. Effective thermal management helps to increase component lifespan, maintain performance and reliability, reduce the risk of component failure, and ensure safety. -
Q: What is Design for Manufacturability (DFM), and why is it important?
A: Design for Manufacturability (DFM) is the practice of designing PCBs in a way that optimizes their manufacturability, ensuring that they can be efficiently and cost-effectively produced. By following DFM best practices, you can reduce manufacturing costs, shorten production times, lower defect rates, and improve product quality and reliability. -
Q: How can I foster effective collaboration and communication in the PCB design process?
A: To foster effective collaboration and communication, establish clear lines of communication between all stakeholders, use a centralized project management system, implement version control and documentation practices, encourage open and transparent communication, and regularly review and validate design decisions with all relevant stakeholders.
Conclusion
In conclusion, understanding and implementing these five crucial PCB design facts can help your boss make informed decisions and stay ahead of the competition. By prioritizing proper component placement, signal integrity, thermal management, DFM considerations, and effective collaboration and communication, you can create PCBs that are efficient, reliable, and cost-effective. As a PCB designer, staying updated with the latest design trends and best practices is essential for driving innovation and success in your organization.
Leave a Reply