Introduction to 4 Layer PCB Stackup
A 4 layer PCB stackup is a printed circuit board (PCB) that consists of four conductive copper layers laminated together with insulating material. This type of PCB stackup is commonly used in complex electronic designs that require higher density and better signal integrity compared to simpler 2 layer PCBs. The four layers allow for more routing options, improved power distribution, and better electromagnetic interference (EMI) control.
Advantages of 4 Layer PCB Stackup
- Increased routing density
- Better signal integrity
- Improved power distribution
- Enhanced EMI control
- Reduced crosstalk and noise
Layers in a 4 Layer PCB Stackup
A typical 4 layer PCB stackup consists of the following layers:
Layer 1: Top Layer (Signal Layer)
The top layer is the outermost layer of the PCB and is primarily used for component placement and signal routing. This layer usually contains the majority of the components and their associated traces.
Layer 2: Ground Plane
The second layer is typically a ground plane, which provides a low-impedance return path for the signals on the top and bottom layers. The ground plane helps to reduce EMI and improve signal integrity by minimizing the loop area of the signal traces.
Layer 3: Power Plane
The third layer is usually a power plane, which distributes the power supply to the components on the PCB. Having a dedicated power plane helps to reduce voltage drop and improve power distribution efficiency.
Layer 4: Bottom Layer (Signal Layer)
The bottom layer is similar to the top layer and is used for additional signal routing and component placement. This layer can also accommodate surface-mounted components if required.
4 Layer PCB Stackup Configurations
There are several common 4 layer PCB stackup configurations, each with its own advantages and disadvantages. The choice of stackup configuration depends on the specific requirements of the design, such as signal integrity, EMI control, and manufacturing constraints.
Configuration 1: Signal-Ground-Power-Signal (SGPS)
In this configuration, the top and bottom layers are used for signal routing, while the inner layers are dedicated to ground and power planes.
Layer | Purpose |
---|---|
1 | Signal |
2 | Ground |
3 | Power |
4 | Signal |
Advantages:
– Good signal integrity due to the presence of ground and power planes
– Suitable for mixed-signal designs with analog and digital components
Disadvantages:
– Limited routing space on the signal layers due to the presence of components
Configuration 2: Signal-Signal-Ground-Power (SSGP)
In this configuration, the top two layers are used for signal routing, while the bottom two layers are dedicated to ground and power planes.
Layer | Purpose |
---|---|
1 | Signal |
2 | Signal |
3 | Ground |
4 | Power |
Advantages:
– Increased routing density on the signal layers
– Suitable for designs with high component density
Disadvantages:
– Potential for increased crosstalk between signal layers
– Reduced EMI control compared to the SGPS configuration
Configuration 3: Signal-Ground-Signal-Power (SGSP)
In this configuration, the top and third layers are used for signal routing, while the second and bottom layers are dedicated to ground and power planes.
Layer | Purpose |
---|---|
1 | Signal |
2 | Ground |
3 | Signal |
4 | Power |
Advantages:
– Good signal integrity due to the presence of ground and power planes between signal layers
– Suitable for high-speed designs with critical signals
Disadvantages:
– Reduced routing density compared to the SSGP configuration
– Potential for increased manufacturing complexity
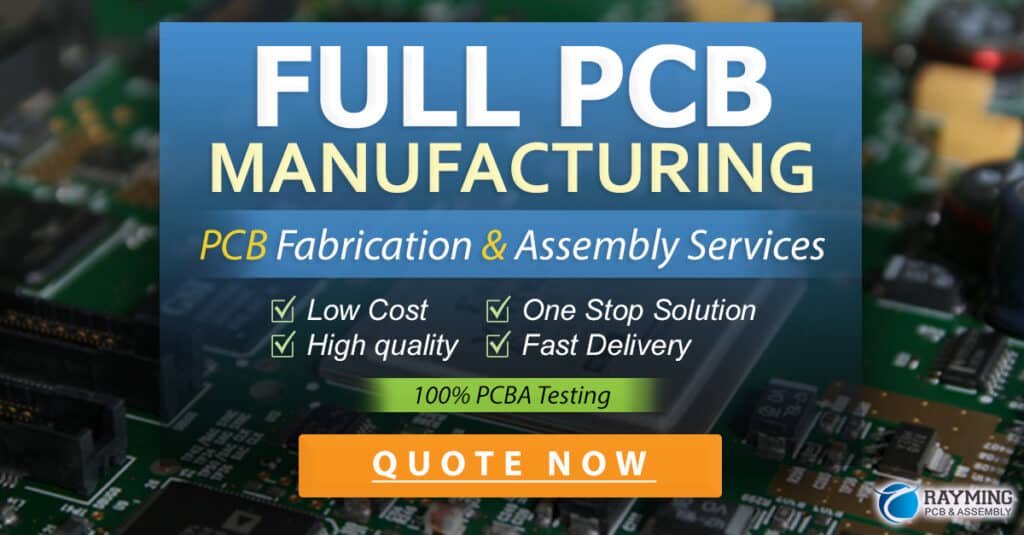
Designing with 4 Layer PCB Stackup
When designing a 4 layer PCB, several factors need to be considered to ensure optimal performance and manufacturability.
Signal Integrity
To maintain good signal integrity, it is essential to follow proper design guidelines, such as:
- Minimizing the length of signal traces
- Avoiding sharp bends and corners in traces
- Matching the impedance of traces to the source and load impedances
- Providing adequate spacing between traces to minimize crosstalk
- Using ground planes to provide a low-impedance return path for signals
Power Distribution
Efficient power distribution is crucial for the proper functioning of the PCB. Some guidelines for power distribution in a 4 layer PCB include:
- Using dedicated power planes to distribute power evenly across the board
- Placing decoupling capacitors close to the power pins of components to reduce noise and voltage fluctuations
- Using wide traces or power planes to minimize voltage drop and improve current carrying capacity
- Providing adequate copper coverage on the power plane to ensure low-impedance power distribution
EMI Control
Controlling electromagnetic interference (EMI) is essential to ensure that the PCB does not interfere with other electronic devices and meets regulatory requirements. Some techniques for EMI control in a 4 layer PCB include:
- Using ground planes to shield sensitive signals from external noise sources
- Placing noisy components, such as switching regulators, away from sensitive analog circuits
- Using shielding techniques, such as metal cans or shielding gaskets, to contain EMI from high-noise components
- Implementing proper grounding and filtering techniques for external connections, such as power inputs and communication ports
Manufacturing Considerations
When designing a 4 layer PCB, it is essential to consider the manufacturing constraints to ensure that the board can be produced reliably and cost-effectively. Some manufacturing considerations include:
- Choosing the appropriate layer thickness and copper weight based on the electrical and mechanical requirements of the design
- Ensuring that the minimum trace width and spacing guidelines are followed to avoid manufacturing issues
- Providing adequate clearance around holes and vias to ensure proper drilling and plating
- Specifying the appropriate solder mask and silkscreen colors and finishes based on the assembly and aesthetic requirements
Frequently Asked Questions (FAQ)
1. What is the typical thickness of a 4 layer PCB?
The typical thickness of a 4 layer PCB ranges from 0.8 mm to 1.6 mm, depending on the specific requirements of the design. Thicker boards offer better mechanical stability and thermal performance, while thinner boards are more suitable for space-constrained applications.
2. Can a 4 layer PCB be used for high-speed designs?
Yes, a 4 layer PCB can be used for high-speed designs, provided that proper design guidelines are followed. The presence of dedicated ground and power planes in a 4 layer stackup helps to maintain signal integrity and control EMI, which are critical for high-speed applications.
3. How does a 4 layer PCB compare to a 2 layer PCB in terms of cost?
A 4 layer PCB is generally more expensive than a 2 layer PCB due to the additional materials and processing steps required. However, the increased cost is often justified by the improved performance, higher routing density, and better EMI control offered by a 4 layer stackup.
4. Can a 4 layer PCB be used for flexible circuits?
Yes, a 4 layer PCB can be used for flexible circuits, although the design and manufacturing process is more complex compared to rigid PCBs. Flexible 4 layer PCBs use flexible substrates, such as polyimide, and require special considerations for bending and flexing.
5. What are the limitations of a 4 layer PCB stackup?
The main limitations of a 4 layer PCB stackup include increased manufacturing complexity and cost compared to simpler 2 layer designs. Additionally, the limited number of layers may not be sufficient for extremely complex designs with high component density and routing requirements. In such cases, higher layer count PCBs, such as 6 or 8 layer stackups, may be necessary.
Conclusion
A 4 layer PCB stackup is a versatile and widely used option for electronic designs that require higher routing density, better signal integrity, and improved EMI control compared to simpler 2 layer PCBs. By understanding the different layers and their functions, as well as the various stackup configurations and design considerations, engineers can create reliable and high-performance 4 layer PCBs for a wide range of applications.
When designing a 4 layer PCB, it is essential to follow best practices for signal integrity, power distribution, and EMI control, while also considering the manufacturing constraints and cost implications. By carefully balancing these factors and working closely with experienced PCB manufacturers, designers can unlock the full potential of 4 layer PCB stackups and create innovative electronic products that meet the demanding requirements of today’s markets.
Leave a Reply