Introduction to 3D Printing Electronic Boards
3D printing technology has revolutionized the way we manufacture objects, and its applications have expanded to include the creation of electronic boards. 3D printing electronic boards offers a cost-effective and efficient alternative to traditional PCB manufacturing methods. This article will explore the process, benefits, and challenges of 3D printing electronic boards.
What is 3D Printing?
3D printing, also known as additive manufacturing, is a process of creating three-dimensional objects by depositing materials layer by layer. The process begins with a digital 3D model, which is then sliced into thin layers by specialized software. The 3D printer then builds the object by depositing materials, such as plastic or metal, one layer at a time until the object is complete.
The Benefits of 3D Printing Electronic Boards
Cost-effective
One of the main advantages of 3D printing electronic boards is its cost-effectiveness. Traditional PCB manufacturing methods require expensive equipment and materials, which can be cost-prohibitive for small-scale production or prototyping. 3D printing, on the other hand, allows for the creation of electronic boards at a fraction of the cost.
Rapid Prototyping
3D printing also enables rapid prototyping of electronic boards. With traditional PCB manufacturing methods, creating a prototype can take weeks or even months. 3D printing allows for the creation of a prototype in a matter of hours or days, enabling faster iteration and development cycles.
Customization
Another benefit of 3D printing electronic boards is the ability to customize the design. Traditional PCB manufacturing methods often require standardized designs and layouts. 3D printing allows for greater flexibility in design, enabling the creation of complex geometries and unique shapes that would be difficult or impossible to achieve with traditional methods.
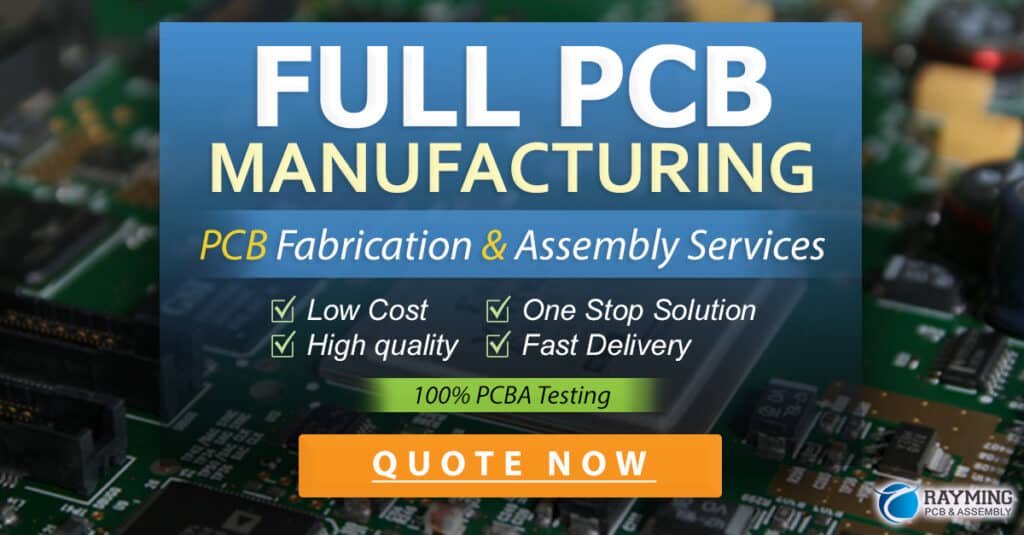
The Process of 3D Printing Electronic Boards
Materials
The first step in 3D printing electronic boards is selecting the appropriate materials. The most common materials used in 3D printing electronic boards are conductive filaments, which are thermoplastics infused with conductive materials such as carbon, graphene, or metal particles. These filaments can be used in standard FDM (fused deposition modeling) 3D printers.
Design
The next step is designing the electronic board using CAD (computer-aided design) software. The design should include the necessary components, such as resistors, capacitors, and integrated circuits, as well as the conductive traces that connect them. The design should also take into account the limitations of the 3D printing process, such as the minimum feature size and the need for support structures.
Printing
Once the design is complete, it can be sent to the 3D printer for printing. The printer will deposit the conductive filament layer by layer, building up the electronic board according to the design. The printing process can take several hours, depending on the size and complexity of the board.
Post-processing
After printing, the electronic board may require some post-processing. This can include removing support structures, smoothing the surface, and adding additional components or connectors. In some cases, the board may also need to be cured or sintered to improve its conductivity and mechanical properties.
Challenges and Limitations of 3D Printing Electronic Boards
Conductivity
One of the main challenges of 3D printing electronic boards is achieving sufficient conductivity. While conductive filaments can be used to create conductive traces, their conductivity is typically lower than that of traditional PCB materials such as copper. This can limit the performance and reliability of 3D-printed electronic boards.
Resolution
Another limitation of 3D printing electronic boards is the resolution of the printing process. While 3D printers can create features as small as a few hundred microns, this is still larger than the minimum feature size of traditional PCB manufacturing methods. This can limit the complexity and density of 3D-printed electronic boards.
Durability
3D-printed electronic boards may also have limited durability compared to traditional PCBs. The materials used in 3D printing are typically less robust than those used in traditional manufacturing, and the layered structure of 3D-printed objects can create weak points and vulnerabilities.
Applications of 3D Printing Electronic Boards
Prototyping
One of the main applications of 3D printing electronic boards is prototyping. 3D printing enables rapid iteration and testing of electronic designs, allowing designers to quickly identify and address issues before committing to full-scale production.
Custom Electronics
3D printing also enables the creation of custom electronics for specialized applications. For example, 3D printing can be used to create electronic boards for wearable devices, medical implants, or aerospace applications where traditional PCB manufacturing methods may not be suitable.
Education
3D printing electronic boards can also be used in education and training. By allowing students to design and print their own electronic boards, 3D printing can help develop skills in electronics, programming, and design.
Future Developments in 3D Printing Electronic Boards
Multi-material Printing
One area of future development in 3D printing electronic boards is multi-material printing. This involves using multiple materials with different properties, such as conductivity and insulation, to create more complex and functional electronic boards.
Embedded Components
Another area of development is the ability to embed electronic components directly into the 3D-printed board. This could enable the creation of more compact and integrated electronic devices.
Improved Materials
Researchers are also working on developing new materials for 3D printing electronic boards, such as conductive ceramics and composites. These materials could offer improved conductivity, durability, and performance compared to current conductive filaments.
Frequently Asked Questions (FAQ)
1. What is the cost of 3D printing electronic boards compared to traditional PCB manufacturing?
The cost of 3D printing electronic boards can vary depending on the materials and equipment used, but it is generally lower than traditional PCB manufacturing for small-scale production or prototyping. However, for large-scale production, traditional PCB manufacturing may be more cost-effective.
2. What is the minimum feature size that can be achieved with 3D printing electronic boards?
The minimum feature size that can be achieved with 3D printing electronic boards depends on the specific printing process and materials used. FDM printing with conductive filaments can typically achieve feature sizes of around 100-200 microns, while other processes such as aerosol jet printing can achieve feature sizes as small as 10 microns.
3. Can 3D-printed electronic boards be used in high-performance applications?
Currently, 3D-printed electronic boards may not be suitable for high-performance applications due to limitations in conductivity, durability, and resolution. However, with ongoing research and development, it is possible that 3D printing could eventually be used to create high-performance electronic boards.
4. What software is used to design 3D-printed electronic boards?
There are several cad software packages that can be used to design 3D-printed electronic boards, including Autodesk Fusion 360, SolidWorks, and KiCad. These software packages allow designers to create 3D models of electronic boards and specify the placement of components and conductive traces.
5. How long does it take to 3D print an electronic board?
The time it takes to 3D print an electronic board depends on the size and complexity of the board, as well as the specific printing process and equipment used. A simple board may take a few hours to print, while a more complex board could take several days.
Conclusion
3D printing electronic boards offers a cost-effective and efficient alternative to traditional PCB manufacturing methods. While there are still challenges and limitations to overcome, ongoing research and development in materials, processes, and software are opening up new possibilities for 3D-printed electronics. As the technology continues to evolve, we can expect to see more widespread adoption of 3D printing in the electronics industry, enabling faster prototyping, greater customization, and new applications in fields such as wearables, medical devices, and aerospace.
Advantages of 3D Printing Electronic Boards | Limitations of 3D Printing Electronic Boards |
---|---|
Cost-effective for small-scale production | Lower conductivity compared to traditional PCBs |
Enables rapid prototyping | Limited resolution and feature size |
Allows for customization and unique designs | Reduced durability compared to traditional PCBs |
Suitable for specialized applications | Not yet suitable for high-performance applications |
In summary, 3D printing electronic boards is an exciting and rapidly evolving technology that has the potential to transform the way we design, prototype, and manufacture electronic devices. While there are still challenges to overcome, the benefits of 3D printing, including cost-effectiveness, rapid prototyping, and customization, make it a promising alternative to traditional PCB manufacturing methods. As research and development continue, we can expect to see even more innovative applications of 3D printing in the electronics industry in the years to come.
Leave a Reply