Introduction to 3D PCB Design
In the world of electronic design, printed circuit boards (PCBs) play a crucial role in connecting and supporting various components. As technology advances and designs become more complex, traditional 2D PCB design methods may no longer suffice. This is where 3D PCB design comes into play, revolutionizing the way engineers and designers approach circuit board creation.
What is 3D PCB Design?
3D PCB design is the process of creating a three-dimensional representation of a printed circuit board. Unlike traditional 2D PCB design, which focuses on the flat layout of components and traces, 3D PCB design incorporates the height, depth, and spatial relationships of the board and its components. This added dimension allows for a more comprehensive and realistic view of the PCB, enabling designers to identify potential issues and optimize the design before manufacturing.
Benefits of 3D PCB Design
- Improved Visualization
- With 3D PCB design, engineers and designers can visualize the board from various angles and perspectives, providing a clearer understanding of the overall layout and component placement.
-
3D models allow for better communication and collaboration among team members, as the design can be easily shared and discussed.
-
Enhanced Design Accuracy
- 3D PCB design tools enable designers to accurately model components, connectors, and mechanical features, ensuring proper fit and alignment.
-
Potential interference and clearance issues can be identified and resolved early in the design process, reducing the likelihood of costly redesigns.
-
Thermal Management
- 3D PCB design allows for the analysis of thermal characteristics and heat dissipation, helping designers optimize component placement and cooling solutions.
-
Thermal simulations can be performed to identify hot spots and ensure the board operates within acceptable temperature ranges.
-
Mechanical Integration
- 3D PCB design facilitates the integration of the PCB with mechanical enclosures and other system components.
-
Designers can ensure proper fit and alignment, reducing the risk of mechanical issues during assembly and manufacturing.
-
Manufacturing Optimization
- By utilizing 3D PCB design, manufacturers can optimize the production process, minimizing errors and improving efficiency.
- 3D models can be used for automated assembly planning, component placement, and generating precise manufacturing instructions.
3D pcb design software and Tools
To effectively create 3D PCB designs, engineers and designers rely on specialized software and tools. These tools provide a range of features and capabilities to streamline the design process and ensure accurate results.
Popular 3D PCB Design Software
Software | Manufacturer | Key Features |
---|---|---|
Altium Designer | Altium | – 3D visualization and modeling |
– MCAD integration | ||
– Thermal analysis | ||
EAGLE 3D | Autodesk | – 3D PCB visualization |
– Real-time 3D rendering | ||
– Component placement and routing | ||
PADS 3D | Mentor | – 3D PCB modeling and visualization |
Graphics | – MCAD collaboration | |
– Thermal and signal integrity analysis | ||
CR-8000 Design | Zuken | – 3D PCB design and modeling |
Force | – Multi-board 3D visualization | |
– MCAD integration and collaboration |
These software tools offer a range of capabilities, from 3D visualization and modeling to thermal analysis and MCAD integration. Designers can choose the software that best suits their needs and workflow preferences.
3D PCB Design Workflow
The typical 3D PCB design workflow involves several key steps:
- schematic design
-
Create the schematic diagram of the circuit, defining the components and their interconnections.
-
Component Selection and Placement
- Select the appropriate components based on the schematic and place them on the PCB layout.
-
Consider factors such as component size, pin configuration, and thermal requirements.
-
3D Modeling
- Create 3D models of the components and the PCB itself using the selected design software.
-
Ensure accurate representation of component dimensions, heights, and shapes.
-
Routing and Trace Optimization
- Route the traces between components, considering signal integrity, impedance matching, and crosstalk.
-
Optimize trace widths, spacing, and lengths to minimize signal degradation and interference.
-
Mechanical Integration
- Integrate the 3D PCB model with the mechanical enclosure and other system components.
-
Ensure proper fit, clearance, and alignment to avoid mechanical issues during assembly.
-
Thermal Analysis
- Perform thermal simulations to analyze heat dissipation and identify potential thermal issues.
-
Optimize component placement and cooling solutions to ensure acceptable operating temperatures.
-
Design Review and Validation
- Review the 3D PCB design for any potential issues or areas for improvement.
-
Validate the design against design rules, manufacturing constraints, and project requirements.
-
Manufacturing Preparation
- Generate manufacturing files, such as Gerber files and assembly instructions, based on the 3D PCB design.
- Communicate with the manufacturing team to ensure smooth transition from design to production.
By following this workflow and leveraging the capabilities of 3D PCB design software, designers can create high-quality, reliable, and manufacturable PCBs.
Case Studies and Real-World Applications
To further illustrate the benefits and impact of 3D PCB design, let’s explore some real-world case studies and applications.
Case Study 1: Automotive Electronics
In the automotive industry, PCBs play a critical role in various electronic systems, from infotainment to advanced driver assistance systems (ADAS). 3D PCB design has proven invaluable in this sector due to its ability to optimize space utilization and ensure reliable performance in harsh environments.
One prominent example is the development of an automotive electronic control unit (ECU) using 3D PCB design. By creating a detailed 3D model of the PCB and its components, engineers were able to:
– Optimize component placement for efficient space utilization within the limited confines of the ECU enclosure.
– Analyze thermal dissipation and implement appropriate cooling solutions to ensure reliable operation in high-temperature environments.
– Integrate the PCB seamlessly with the mechanical enclosure, ensuring proper fit and alignment during assembly.
The use of 3D PCB design in this automotive application resulted in a more compact, reliable, and thermally optimized ECU, contributing to improved vehicle performance and safety.
Case Study 2: Medical Devices
Medical devices require high levels of precision, reliability, and safety. 3D PCB design has become increasingly important in this field, enabling the development of compact and intricate devices that meet stringent regulatory requirements.
One example is the design of a wearable medical monitoring device using 3D PCB design. The challenges in this project included:
– Miniaturization of the PCB to fit within the compact wearable form factor.
– Ensuring proper signal integrity and electromagnetic compatibility (EMC) to avoid interference with other medical equipment.
– Integrating the PCB with the device enclosure and other mechanical components for a seamless and comfortable user experience.
By leveraging 3D PCB design tools, the engineering team was able to:
– Create a detailed 3D model of the PCB, optimizing component placement and routing for miniaturization.
– Simulate and analyze signal integrity and EMC performance, making necessary adjustments to ensure reliable operation.
– Collaborate effectively with mechanical engineers to ensure proper integration of the PCB within the wearable device enclosure.
The resulting medical monitoring device achieved the desired level of miniaturization, reliability, and user comfort, demonstrating the value of 3D PCB design in the medical industry.
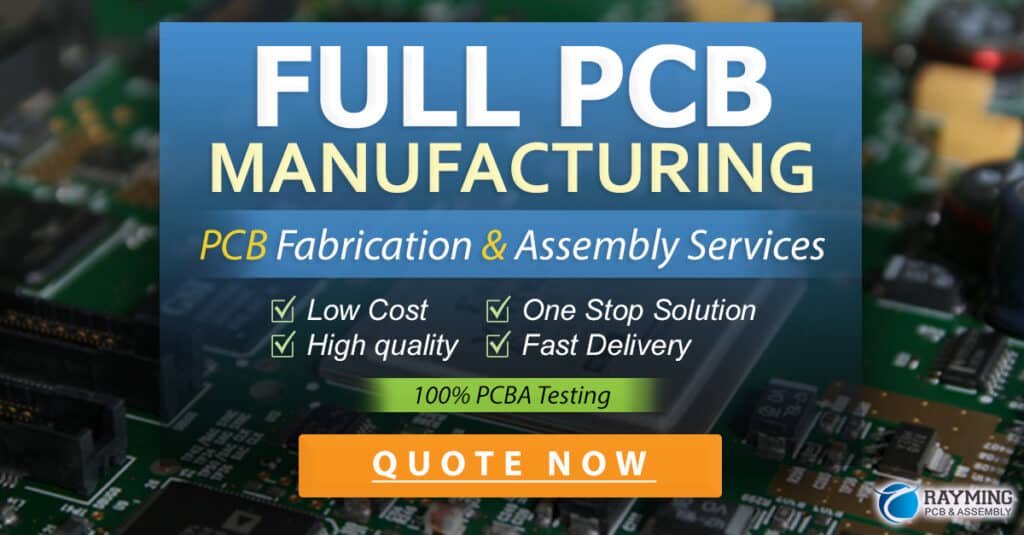
Frequently Asked Questions (FAQ)
-
Q: What are the system requirements for running 3D PCB design software?
A: System requirements vary depending on the specific software, but generally, a modern computer with a multi-core processor, dedicated graphics card, and sufficient RAM (16GB or more) is recommended for optimal performance. Large PCB designs may require even higher specifications. -
Q: Can 3D PCB design files be easily shared and collaborated on with team members?
A: Yes, most 3D PCB design software tools support file sharing and collaboration features. Design files can be shared through version control systems, cloud-based platforms, or exported in common file formats for easy exchange and review among team members. -
Q: How does 3D PCB design impact the manufacturing process?
A: 3D PCB design provides a more accurate representation of the final product, allowing manufacturers to optimize their processes. The 3D models can be used for automated assembly planning, component placement, and generating precise manufacturing instructions. This reduces the risk of errors and improves overall manufacturing efficiency. -
Q: Is 3D PCB design suitable for all types of PCBs?
A: 3D PCB design is beneficial for a wide range of PCBs, from simple single-layer boards to complex multi-layer designs. It is particularly advantageous for high-density PCBs, boards with intricate mechanical requirements, and designs that require thermal optimization. However, for very simple or low-complexity PCBs, traditional 2D design methods may suffice. -
Q: What skills are required to effectively use 3D PCB design software?
A: To effectively use 3D PCB design software, individuals should have a strong foundation in electronic design principles, including schematic capture, component selection, and PCB layout. Familiarity with 3D modeling concepts and experience with cad tools can also be beneficial. Additionally, knowledge of manufacturing processes and design for manufacturability (DFM) principles is important for creating successful 3D PCB designs.
Conclusion
3D PCB design has revolutionized the way engineers and designers approach circuit board creation. By providing a comprehensive and realistic representation of the PCB, 3D design tools enable improved visualization, enhanced design accuracy, thermal optimization, mechanical integration, and manufacturing efficiency.
As technology continues to advance and electronic systems become more complex, the adoption of 3D PCB design will become increasingly crucial. By leveraging the capabilities of 3D design software and following best practices, engineers and designers can create high-quality, reliable, and manufacturable PCBs that meet the demands of today’s innovative applications.
Embracing 3D PCB design is not only beneficial but also necessary for staying competitive in the ever-evolving world of electronics. By investing in the right tools, skills, and workflows, companies can unlock the full potential of 3D PCB design and drive innovation in their products and services.
Leave a Reply