Introduction to 2n2 PCB Stackup Design
In the world of high-density interconnect (HDI) printed circuit boards (PCBs), the 2n2 stackup design has emerged as a popular choice for its ability to balance performance, manufacturability, and cost-effectiveness. This article will delve into the intricacies of 2n2 PCB stackup design, exploring its benefits, considerations, and best practices for HDI boards.
What is a 2n2 PCB Stackup?
A 2n2 PCB stackup refers to a specific arrangement of layers in a PCB, where “2” represents the number of signal layers and “n” represents the number of power and ground layers. In a typical 2n2 stackup, there are two signal layers (top and bottom) and two internal layers dedicated to power and ground planes.
The general structure of a 2n2 PCB stackup is as follows:
Layer | Description |
---|---|
Top | Signal layer |
n | Power/Ground layer |
n | Power/Ground layer |
Bottom | Signal layer |
Advantages of 2n2 PCB Stackup Design
-
Improved Signal Integrity: The 2n2 stackup provides a balanced distribution of signal layers and power/ground planes, minimizing crosstalk and electromagnetic interference (EMI). The internal power and ground planes act as shields, reducing noise and ensuring cleaner signal transmission.
-
Enhanced Power Distribution: With dedicated power and ground layers, the 2n2 stackup offers a low-impedance power distribution network. This helps maintain stable voltage levels across the board, reducing voltage drop and improving overall power integrity.
-
Cost-Effectiveness: Compared to more complex stackups with a higher number of layers, the 2n2 design offers a cost-effective solution for HDI boards. It strikes a balance between performance and manufacturability, making it an attractive option for many applications.
-
Simplified Manufacturing: The 2n2 stackup simplifies the manufacturing process by reducing the number of layers and minimizing the need for complex via structures. This leads to improved yields, shorter lead times, and lower production costs.
Designing with 2n2 PCB Stackup
Layer Arrangement and Spacing
When designing a 2n2 PCB stackup, careful consideration should be given to the arrangement and spacing of layers. The typical layer arrangement is as follows:
Layer | Material | Thickness (mm) |
---|---|---|
Top | Copper | 0.035 |
Prepreg | FR-4 | 0.2 |
n | Copper | 0.035 |
Core | FR-4 | 0.2 |
n | Copper | 0.035 |
Prepreg | FR-4 | 0.2 |
Bottom | Copper | 0.035 |
The spacing between layers should be optimized to achieve the desired impedance and minimize signal integrity issues. The dielectric thickness and material properties play a crucial role in determining the impedance and signal propagation characteristics.
Via Structures and Routing
In HDI boards, the use of microvias and buried vias is common to achieve high-density interconnects. When designing with a 2n2 stackup, consider the following via structures:
-
Blind Vias: Blind vias connect the outer layers to the inner layers without penetrating through the entire board thickness. They are used to route signals from the top or bottom layer to the internal power or ground planes.
-
Buried Vias: Buried vias are used to interconnect internal layers without connecting to the outer layers. In a 2n2 stackup, buried vias can be used to route signals between the two internal power and ground planes.
-
Through-Hole Vias: Through-hole vias, also known as plated through-holes (PTHs), penetrate through the entire board thickness. They are used for component mounting and provide connections between all layers.
When routing traces in a 2n2 stackup, consider the following guidelines:
- Route critical signals on the outer layers to minimize the impact of via stubs and improve signal integrity.
- Use the internal power and ground planes for shielding and to provide a low-impedance return path for high-speed signals.
- Minimize the use of vias, especially for high-speed signals, to reduce discontinuities and reflections.
- Follow proper trace width and spacing guidelines based on the desired impedance and manufacturing capabilities.
Power and Ground Plane Considerations
The power and ground planes in a 2n2 stackup play a crucial role in maintaining power integrity and providing a stable reference for signals. Consider the following when designing power and ground planes:
-
Plane Thickness: The thickness of the power and ground planes should be sufficient to handle the expected current flow without excessive voltage drop. Thicker planes provide lower resistance and better current-carrying capacity.
-
Plane Splits: In some cases, it may be necessary to split the power or ground plane to accommodate multiple voltage domains or to isolate noise-sensitive regions. Carefully plan the plane splits to minimize disruption to the current flow and avoid creating unnecessary discontinuities.
-
Decoupling capacitors: Place decoupling capacitors close to the power pins of active components to minimize the loop area and provide a low-impedance path for high-frequency noise. Use a combination of bulk and ceramic capacitors to cover different frequency ranges.
-
Via Stitching: Use via stitching techniques to connect the power and ground planes at regular intervals. This helps reduce plane impedance, improves current distribution, and minimizes voltage drop.
Best Practices for 2n2 PCB Stackup Design
-
Collaborate with the Manufacturer: Engage with your PCB manufacturer early in the design process to discuss the capabilities, limitations, and recommended practices for 2n2 stackup design. They can provide valuable insights and help optimize your design for manufacturability.
-
Simulate and Validate: Use simulation tools to analyze signal integrity, power integrity, and EMI/EMC performance of your 2n2 stackup. Perform pre-layout and post-layout simulations to identify and address any potential issues before finalizing the design.
-
Adhere to Design Rules: Follow the design rules and guidelines provided by your PCB manufacturer and the relevant industry standards (e.g., IPC). This includes rules for minimum trace width and spacing, via sizes, and clearances.
-
Plan for Testability: Consider the testability requirements of your HDI board during the design phase. Incorporate test points, boundary scan, and other testability features to facilitate manufacturing testing and debugging.
-
Document and Communicate: Clearly document your 2n2 stackup design, including layer arrangements, material specifications, and design rules. Communicate this information effectively to the manufacturing team to ensure accurate fabrication and assembly.
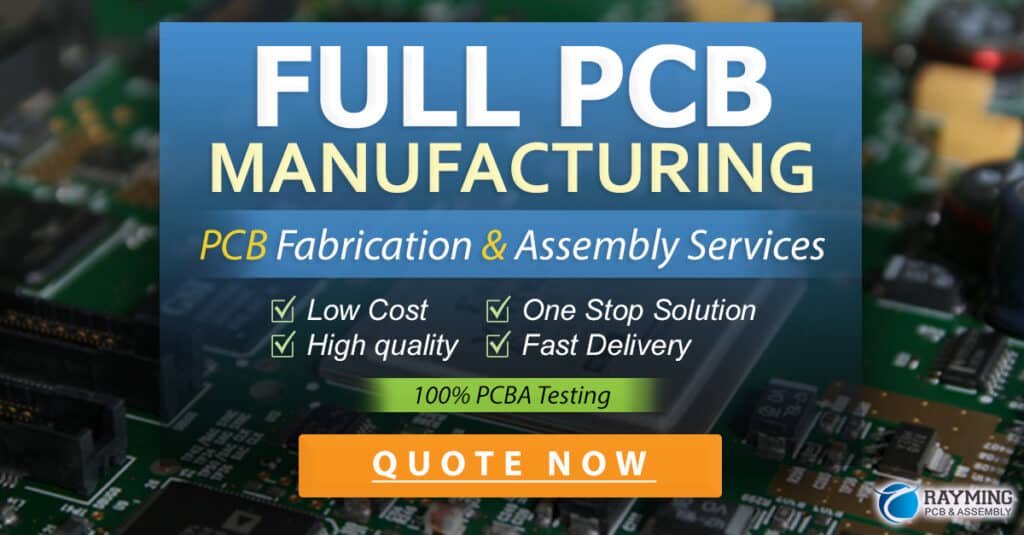
Frequently Asked Questions (FAQ)
-
Q: What is the difference between a 2n2 and a 4-layer PCB stackup?
A: A 2n2 PCB stackup has two signal layers (top and bottom) and two internal power/ground layers, while a 4-layer PCB stackup typically has four signal layers. The 2n2 stackup offers a more cost-effective solution with improved power distribution and signal integrity compared to a 4-layer stackup. -
Q: Can a 2n2 PCB stackup support high-speed designs?
A: Yes, a well-designed 2n2 PCB stackup can support high-speed designs. By carefully considering signal integrity, power distribution, and via structures, a 2n2 stackup can effectively handle high-speed signals while maintaining good signal quality and minimizing noise. -
Q: How does the choice of dielectric material affect the performance of a 2n2 PCB stackup?
A: The dielectric material used in a 2n2 PCB stackup influences the signal propagation speed, impedance, and loss characteristics. Low-loss materials, such as high-frequency laminates, can help minimize signal attenuation and maintain signal integrity at higher frequencies. The dielectric constant and dissipation factor of the material should be carefully selected based on the design requirements. -
Q: What are the limitations of using a 2n2 PCB stackup for HDI designs?
A: The limitations of a 2n2 PCB stackup for HDI designs include reduced routing flexibility compared to stackups with more layers, potential signal integrity challenges for extremely high-speed signals, and limited space for power and ground planes. However, for many HDI applications, a well-designed 2n2 stackup can provide a balanced and cost-effective solution. -
Q: Can a 2n2 PCB stackup accommodate mixed-signal designs?
A: Yes, a 2n2 PCB stackup can accommodate mixed-signal designs by carefully partitioning the board into analog and digital sections. Techniques such as split planes, proper grounding strategies, and appropriate component placement can help mitigate noise coupling between analog and digital domains. However, for more complex mixed-signal designs, additional layers or specialized stackups may be necessary.
Conclusion
The 2n2 PCB stackup design offers a balanced and cost-effective solution for HDI boards, providing improved signal integrity, power distribution, and manufacturability. By carefully considering layer arrangement, via structures, routing strategies, and power/ground plane design, engineers can optimize the performance of their HDI boards using a 2n2 stackup.
However, it is essential to collaborate closely with PCB manufacturers, adhere to design rules and guidelines, and perform thorough simulations and validations to ensure the success of a 2n2 PCB stackup design. By following best practices and staying updated with industry trends, designers can effectively leverage the benefits of 2n2 stackup for their HDI applications.
As technology continues to advance and the demands for high-density interconnects grow, the 2n2 PCB stackup design remains a valuable tool in the arsenal of PCB designers. By understanding its principles, advantages, and limitations, engineers can make informed decisions and create robust, reliable, and cost-effective HDI boards using the 2n2 stackup approach.
Leave a Reply