What is a 2+N+2 PCB Stackup?
A 2+N+2 PCB stackup is a specific arrangement of layers in an HDI PCB, where “2” represents the number of outer layers (top and bottom), “N” represents the number of inner layers, and the second “2” represents the two additional layers used for power and ground planes. This stackup design offers several advantages over traditional PCB stackups, making it an ideal choice for HDI applications.
The typical structure of a 2+N+2 PCB stackup is as follows:
Layer | Description |
---|---|
Top Layer | Signal layer |
Inner Layer 1 | Signal layer |
Inner Layer 2 | Signal layer |
… | … |
Inner Layer N-1 | Signal layer |
Inner Layer N | Signal layer |
Power Layer | Power plane |
Ground Layer | Ground plane |
Bottom Layer | Signal layer |
Benefits of 2+N+2 PCB Stackup
1. Improved Signal Integrity
One of the primary benefits of the 2+N+2 PCB stackup is its ability to maintain signal integrity. By placing the power and ground planes between the inner signal layers and the outer layers, the stackup effectively shields the sensitive inner signals from external noise and interference. This arrangement also reduces the loop area between the signal and return paths, minimizing electromagnetic interference (EMI) and crosstalk.
2. Enhanced Power Distribution
The dedicated power and ground planes in the 2+N+2 stackup provide a low-impedance path for power distribution throughout the PCB. This helps to minimize voltage drops and ensure stable power delivery to all components on the board. The uniform power distribution also contributes to reducing EMI and improving overall system performance.
3. Increased Routing Density
With the 2+N+2 stackup, designers have the flexibility to accommodate a higher number of signal layers, enabling increased routing density. The additional inner layers allow for more complex routing patterns and higher component density, which is crucial for HDI designs. This stackup also facilitates the use of smaller via sizes and finer pitch components, further enhancing the board’s density and functionality.
Design Considerations for 2+N+2 PCB Stackup
When designing a 2+N+2 PCB stackup for HDI boards, several key factors must be considered to ensure optimal performance and manufacturability.
1. Material Selection
The choice of dielectric materials plays a crucial role in the performance of an HDI PCB. For the 2+N+2 stackup, it is recommended to use low-loss, high-speed materials such as RO4350B, FR-4, or IS400. These materials offer excellent electrical properties, including low dielectric constant (Dk) and dissipation factor (Df), which help to minimize signal loss and distortion.
2. Layer Thickness and Spacing
The thickness of the copper layers and the spacing between them should be carefully chosen to achieve the desired impedance and minimize signal reflections. Typical copper weights for HDI PCBs range from 0.5 oz to 1 oz, with thinner layers preferred for finer pitch components and higher routing density. The dielectric thickness between layers should be optimized based on the desired impedance and the chosen material’s Dk value.
3. Via Design
Via design is critical in HDI PCBs, as it directly affects signal integrity and manufacturability. For the 2+N+2 stackup, micro vias and buried vias are commonly used to minimize the via size and improve routing density. The via aspect ratio (depth to diameter) should be kept within manufacturable limits, typically 1:1 or less. Additionally, via stubs should be minimized to reduce signal reflections and improve impedance matching.
4. Power and Ground Plane Design
The power and ground planes in the 2+N+2 stackup should be designed to provide a low-impedance return path for high-speed signals. Proper power plane decoupling and the use of ground stitching vias help to minimize power supply noise and improve signal integrity. The placement of decoupling capacitors close to the power pins of active components is also crucial for maintaining stable power delivery.
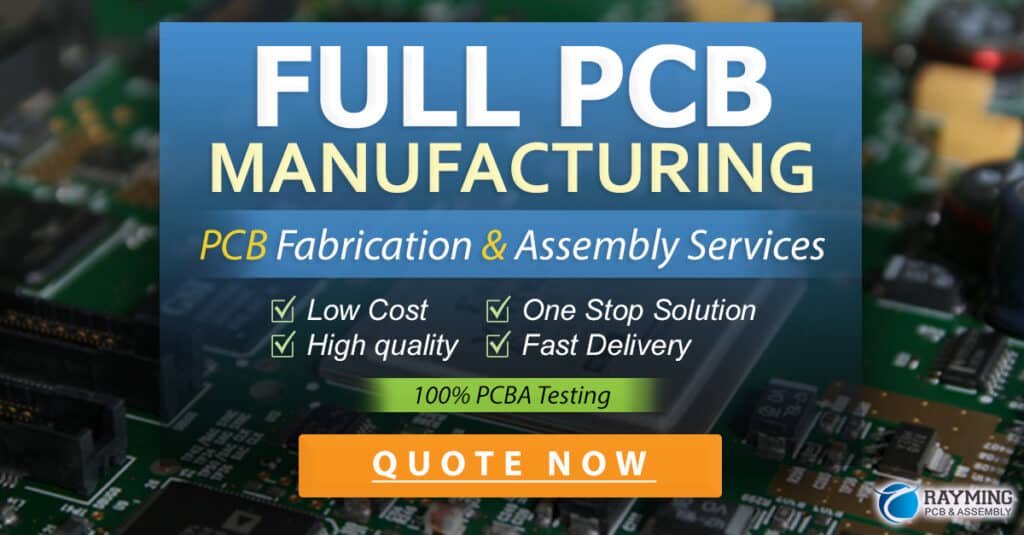
Best Practices for 2+N+2 PCB Stackup Design
To achieve optimal performance and manufacturability in 2+N+2 PCB stackups for HDI boards, consider the following best practices:
- Use a symmetrical stackup whenever possible to minimize warpage and ensure even copper distribution.
- Keep the signal layers close to the power and ground planes to minimize loop area and reduce EMI.
- Use appropriate trace widths and spacing based on the desired impedance and current carrying requirements.
- Minimize the use of vias, especially through-hole vias, to reduce signal discontinuities and improve routing density.
- Implement proper power plane decoupling and ground stitching techniques to maintain signal integrity.
- Collaborate closely with your PCB manufacturer to ensure that your design is manufacturable and meets their specific guidelines.
Frequently Asked Questions (FAQ)
1. What is the minimum via size achievable in a 2+N+2 PCB stackup?
The minimum via size in a 2+N+2 PCB stackup depends on the specific manufacturer’s capabilities and the chosen materials. Typically, micro vias with diameters as small as 0.1 mm (4 mil) can be achieved in HDI designs.
2. How many inner layers can be accommodated in a 2+N+2 PCB stackup?
The number of inner layers (N) in a 2+N+2 PCB stackup is limited by the overall board thickness and the chosen material thicknesses. In general, up to 8 inner layers can be accommodated in a standard 2+N+2 stackup, but this can vary depending on the specific design requirements and manufacturing capabilities.
3. Can blind vias be used in a 2+N+2 PCB stackup?
Yes, blind vias can be used in a 2+N+2 PCB stackup to connect the outer layers to the inner layers without going through the entire board thickness. This can help to improve routing density and minimize the use of through-hole vias.
4. What is the typical impedance target for traces in a 2+N+2 PCB stackup?
The typical impedance target for traces in a 2+N+2 PCB stackup is 50 ohms for single-ended signals and 100 ohms for differential pairs. However, the actual impedance values may vary depending on the specific application and design requirements.
5. How does the 2+N+2 PCB stackup compare to other HDI stackups?
The 2+N+2 PCB stackup offers several advantages over other HDI stackups, such as improved signal integrity, enhanced power distribution, and increased routing density. However, other stackups like 1+N+1 or 3+N+3 may be more suitable for certain applications depending on the specific design requirements and manufacturing constraints.
Conclusion
The 2+N+2 PCB stackup is a powerful design approach for HDI boards, offering improved signal integrity, enhanced power distribution, and increased routing density. By carefully considering material selection, layer thickness and spacing, via design, and power and ground plane design, engineers can create high-performance HDI PCBs that meet the demanding requirements of modern electronics.
When designing a 2+N+2 PCB stackup, it is essential to follow best practices and work closely with your PCB manufacturer to ensure optimal performance and manufacturability. By understanding the benefits and design considerations of this stackup, engineers can unlock the full potential of HDI technology and create innovative, reliable, and compact electronic devices.
Leave a Reply