Introduction to PCB Design and Assembly
Printed Circuit Board (PCB) design and assembly is a critical process in the development of electronic devices. PCBs are the backbone of modern electronics, connecting components and allowing for complex circuits to be built in a compact and efficient manner. However, designing a PCB that is optimized for assembly can be a challenging task, requiring careful consideration of various factors such as component placement, routing, and manufacturability.
In this article, we will explore 15 tips for PCB design that can help ensure a smooth and efficient assembly process. By following these guidelines, you can reduce the risk of errors, improve the reliability of your PCBs, and ultimately save time and money in the manufacturing process.
Understanding the PCB Assembly Process
Before diving into specific design tips, it’s important to have a basic understanding of the PCB assembly process. This will help you make informed decisions during the design phase that can optimize the assembly process down the line.
The Main Steps in PCB Assembly
- Solder Paste Application: A stencil is used to apply solder paste to the PCB pads where components will be placed.
- Component Placement: A pick-and-place machine or manual placement is used to position components on the PCB according to the design.
- Reflow Soldering: The PCB is heated in a reflow oven, melting the solder paste and forming a permanent connection between the components and the PCB.
- Inspection and Testing: The assembled PCB undergoes visual inspection and electrical testing to ensure proper functionality and identify any defects.
Understanding these steps can help you design your PCB in a way that facilitates each stage of the assembly process.
Tip #1: Choose the Right PCB Size and Shape
The size and shape of your PCB can have a significant impact on the assembly process. Here are some factors to consider:
- Standardized Sizes: Whenever possible, stick to standard PCB sizes (e.g., 100mm x 100mm, 150mm x 200mm). This can reduce manufacturing costs and lead times.
- Panelization: If your PCB is small, consider panelizing multiple boards together to improve assembly efficiency and reduce handling costs.
- Odd Shapes: Avoid odd-shaped PCBs when possible, as they can be more difficult to handle and assemble. If an odd shape is necessary, ensure that it can be easily panelized.
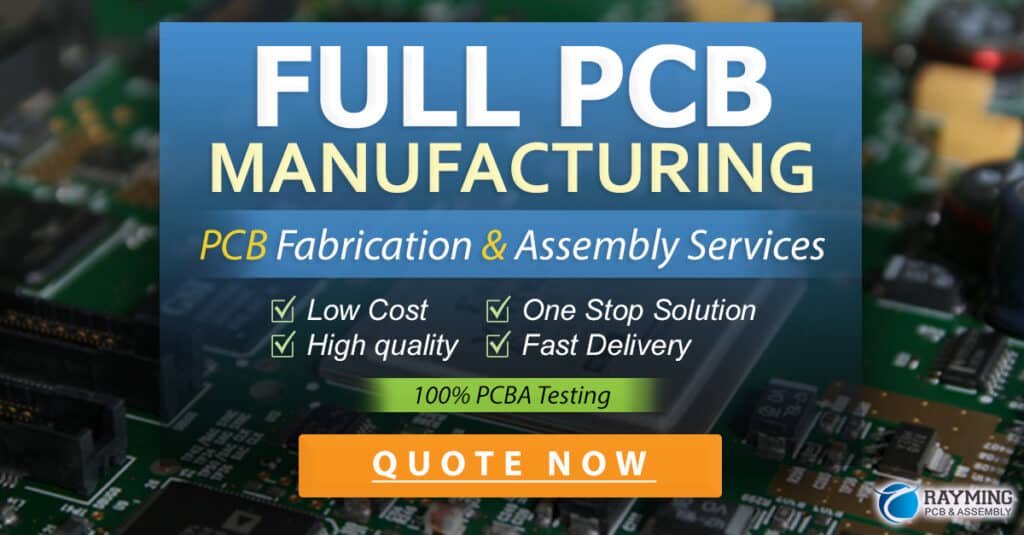
Tip #2: Use Appropriate Component Footprints
Component footprints are the patterns of pads and holes on the PCB that correspond to a particular component. Using the correct footprints is essential for proper component placement and soldering. Here are some guidelines:
- Manufacturer Recommendations: Always refer to the component manufacturer’s datasheet for recommended footprint dimensions.
- Pad Size: Ensure that pads are large enough for reliable soldering but not so large that they interfere with adjacent components.
- Hole Size: For through-hole components, make sure the hole size is appropriate for the component lead diameter.
Tip #3: Optimize Component Placement
The placement of components on your PCB can greatly affect the assembly process. Here are some tips for optimizing component placement:
- Grouping: Group similar components together (e.g., resistors, capacitors) to improve pick-and-place efficiency.
- Orientation: Orient components in the same direction when possible to reduce placement errors and improve visual inspection.
- Clearance: Ensure adequate clearance between components to avoid interference and facilitate inspection and rework.
Tip #4: Consider Thermal Requirements
Thermal management is crucial for the long-term reliability of your PCB. Here are some tips for addressing thermal requirements in your design:
- High-Power Components: Place high-power components (e.g., voltage regulators, power transistors) away from heat-sensitive components and provide adequate heat sinking.
- Thermal Relief: Use thermal relief pads for components that generate significant heat to prevent solder joint fatigue.
- Copper Pour: Use copper pour on the PCB to improve heat dissipation and reduce thermal stress on components.
Tip #5: Optimize Routing and Trace Widths
Proper routing and trace widths are essential for signal integrity and manufacturability. Here are some guidelines:
- Trace Width: Use appropriate trace widths based on the current carrying requirements of the circuit. Wider traces can handle higher currents but may increase the board size.
- Routing: Route traces as directly as possible to minimize signal reflections and crosstalk. Avoid sharp angles and use curved traces when necessary.
- Spacing: Maintain adequate spacing between traces to prevent short circuits and improve manufacturability.
Tip #6: Use Appropriate Solder Mask and Silkscreen
Solder mask and silkscreen are important for protecting the PCB and providing visual indicators for assembly. Here are some tips:
- Solder Mask: Use solder mask to cover exposed copper traces and prevent short circuits. Ensure adequate solder mask clearance around pads for proper soldering.
- Silkscreen: Use silkscreen to label components, provide assembly instructions, and indicate test points. Ensure that silkscreen text is legible and does not interfere with component placement.
Tip #7: Implement Design for Manufacturing (DFM) Rules
Design for Manufacturing (DFM) rules are guidelines that help ensure your PCB can be efficiently and reliably manufactured. Some key DFM rules include:
- Minimum Trace Width and Spacing: Adhere to the manufacturer’s minimum trace width and spacing requirements to ensure reliable etching and prevent short circuits.
- Drill Hole Size and Spacing: Use appropriate drill hole sizes and spacing for through-hole components and vias to ensure proper plating and prevent drill breakage.
- Solder Mask and Silkscreen Clearance: Maintain adequate clearance between solder mask openings, silkscreen, and components to prevent interference and improve assembly reliability.
Tip #8: Use Standardized Components
Using standardized components can greatly simplify the assembly process and reduce costs. Here are some benefits of standardized components:
- Availability: Standardized components are readily available from multiple suppliers, reducing lead times and minimizing the risk of obsolescence.
- Cost: Standardized components are often less expensive than custom or specialized components due to economies of scale.
- Familiarity: Assembly personnel are more familiar with standardized components, reducing the risk of placement errors and improving efficiency.
Tip #9: Consider Assembly Orientation
The orientation of your PCB during assembly can impact the efficiency and reliability of the process. Here are some factors to consider:
- Component Placement: Place components on the same side of the board whenever possible to reduce the number of assembly steps and minimize handling.
- Connector Placement: Place connectors and other external interfaces along the edges of the board for easy access and to reduce the risk of damage during handling.
- Panelization: Consider the orientation of your PCB when panelizing to optimize the assembly process and minimize waste.
Tip #10: Incorporate Fiducial Markers
Fiducial markers are small, precisely placed features on the PCB that serve as reference points for automated assembly equipment. Here are some tips for incorporating fiducial markers:
- Placement: Place fiducial markers on both sides of the board, near the corners, and away from components and other features.
- Size and Shape: Use a standard size and shape for fiducial markers (e.g., 1mm diameter circular pads) to ensure compatibility with assembly equipment.
- Solder Mask: Leave fiducial markers exposed (no solder mask) to provide a clear visual reference for the assembly equipment.
Tip #11: Use Appropriate Solder Paste
Selecting the appropriate solder paste is crucial for achieving reliable solder joints and preventing defects. Here are some factors to consider:
- Alloy Composition: Choose a solder paste alloy that is compatible with your components and meets the required melting temperature and strength.
- Particle Size: Select a solder paste with an appropriate particle size for your component pitch and stencil thickness.
- Flux Activity: Consider the flux activity level of the solder paste based on the cleanliness of your components and the desired solder joint quality.
Tip #12: Optimize Stencil Design
The solder paste stencil is a critical tool in the PCB assembly process, and its design can greatly impact the quality of the solder joints. Here are some tips for optimizing your stencil design:
- Aperture Size: Use appropriate aperture sizes based on the component pad size and desired solder volume.
- Aperture Shape: Consider using specialized aperture shapes (e.g., home plate, trapezoidal) for fine-pitch components to improve solder paste release.
- Stencil Thickness: Choose a stencil thickness that balances solder paste volume and release characteristics, typically between 0.1mm and 0.15mm.
Tip #13: Implement Testability Features
Incorporating testability features into your PCB design can greatly simplify the inspection and testing process during assembly. Here are some testability features to consider:
- Test Points: Include test points for critical signals and power rails to facilitate in-circuit testing and debugging.
- Boundary Scan: Implement boundary scan (JTAG) testing for complex digital circuits to enable automated testing and fault isolation.
- Functional Test Pads: Include pads or connectors for functional testing of the assembled PCB to verify proper operation before final installation.
Tip #14: Collaborate with Your Assembly Partner
Effective communication and collaboration with your PCB assembly partner can help ensure a smooth and successful assembly process. Here are some tips for collaboration:
- Early Involvement: Engage your assembly partner early in the design process to identify potential issues and optimize the design for assembly.
- Documentation: Provide clear and comprehensive documentation, including bill of materials (BOM), assembly drawings, and special instructions.
- Design Review: Request a design review from your assembly partner to catch any potential issues before production begins.
Tip #15: Prototype and Test
Prototyping and testing your PCB design before full-scale production can help identify and resolve any issues early in the process. Here are some tips for prototyping and testing:
- Prototype Assembly: Have a small batch of boards assembled to verify the design and identify any assembly challenges.
- Functional Testing: Perform thorough functional testing on the prototypes to ensure proper operation and catch any design or component issues.
- Design Revisions: Incorporate any necessary design revisions based on the prototype results before proceeding with full-scale production.
Frequently Asked Questions (FAQ)
1. What is the difference between surface mount (SMT) and through-hole (THT) assembly?
Surface mount technology (SMT) involves placing components directly onto the surface of the PCB, while through-hole technology (THT) requires components to be inserted through holes in the board. SMT is generally more efficient and allows for smaller component sizes, while THT is often used for larger, heavier components or when mechanical strength is a priority.
2. How can I reduce the cost of PCB assembly?
Some ways to reduce PCB assembly costs include:
- Using standardized components and PCB sizes
- Minimizing the number of unique components
- Optimizing the PCB layout for efficient assembly
- Choosing a cost-effective assembly partner
- Ordering larger quantities to take advantage of volume discounts
3. What is the minimum feature size for PCB traces and spaces?
The minimum feature size depends on the capabilities of your PCB manufacturer and the desired reliability of the board. Typical minimum trace widths and spaces range from 0.1mm to 0.2mm, but some advanced manufacturers can achieve even smaller features. Always consult with your manufacturer for their specific capabilities and recommendations.
4. How do I ensure the reliability of my assembled PCBs?
To ensure the reliability of your assembled PCBs:
- Follow best practices for PCB design, including proper component selection, placement, and routing
- Use appropriate solder paste and stencil design for reliable solder joints
- Implement thorough testing and inspection processes during assembly
- Work with a reputable assembly partner with a proven track record of quality
- Perform accelerated life testing and environmental stress screening when necessary
5. What documentation is required for PCB assembly?
The essential documentation for PCB assembly includes:
- Bill of Materials (BOM): A comprehensive list of all components used in the design, including part numbers, quantities, and descriptions
- Assembly Drawings: Visual representations of the PCB layout, showing component placement, orientation, and any special instructions
- Gerber Files: The industry-standard format for describing the PCB layout, including copper layers, solder mask, and silkscreen
- NC Drill Files: The files that specify the locations and sizes of all holes in the PCB
- Pick and Place Files: The files that provide the coordinates and orientations for automated component placement
Conclusion
Designing a PCB for efficient and reliable assembly requires careful consideration of various factors, from component selection and placement to routing and manufacturability. By following the 15 tips outlined in this article, you can optimize your PCB design for assembly, reducing the risk of errors, improving reliability, and ultimately saving time and money in the manufacturing process.
Remember to collaborate closely with your assembly partner, prototype and test your designs, and continuously refine your processes based on feedback and results. With a commitment to best practices and continuous improvement, you can ensure the success of your PCB assembly projects and bring your electronic products to market with confidence.
Leave a Reply