Understanding the Importance of PCB Thermal Management
Before diving into specific techniques, it’s essential to understand why thermal management is critical for PCBs. Excess heat can lead to various issues, including:
- Component failure due to thermal stress
- Reduced performance and efficiency
- Shortened lifespan of electronic devices
- Increased risk of thermal runaway
By implementing proper thermal management strategies, designers can mitigate these risks and ensure optimal PCB performance.
Thermal Management Techniques
1. Copper Plane Placement
One of the most effective ways to improve thermal dissipation is by strategically placing copper planes on the PCB. Copper is an excellent thermal conductor, allowing heat to spread evenly across the board. Consider the following guidelines:
- Place copper planes near high-power components to facilitate heat transfer
- Use thicker copper planes for better thermal conductivity
- Ensure proper spacing between copper planes to avoid electrical interference
Copper Thickness | Thermal Conductivity (W/mK) |
---|---|
0.5 oz | 385 |
1 oz | 385 |
2 oz | 385 |
2. Thermal Vias
Thermal vias are small, conductive holes drilled through the PCB to transfer heat from one layer to another. They help dissipate heat away from hot spots and into the cooler areas of the board. When using thermal vias, keep these tips in mind:
- Place thermal vias close to high-power components
- Use an adequate number of vias to ensure effective heat transfer
- Optimize via size and spacing for better thermal performance
3. Component Placement
Proper component placement is crucial for efficient thermal management. Follow these guidelines:
- Distribute high-power components evenly across the board to avoid heat concentration
- Place temperature-sensitive components away from heat sources
- Consider the airflow direction when placing components
4. Heatsinks and Heat Spreaders
Heatsinks and heat spreaders are passive cooling devices that help dissipate heat away from components. They work by increasing the surface area for heat dissipation and promoting airflow. When using heatsinks or heat spreaders:
- Choose the appropriate size and material based on the component’s power dissipation
- Ensure proper thermal interface material (TIM) between the component and heatsink
- Consider the orientation and placement of the heatsink for optimal airflow
5. Thermal Interface Materials (TIMs)
TIMs are materials that fill the gaps between components and heatsinks, enhancing thermal conductivity. Common TIMs include thermal paste, thermal pads, and phase change materials. When selecting a TIM:
- Choose a material with high thermal conductivity
- Ensure proper application and thickness for optimal performance
- Consider the ease of application and removal for maintenance purposes
TIM Type | Thermal Conductivity (W/mK) |
---|---|
Thermal Paste | 0.5 – 10 |
Thermal Pad | 1 – 5 |
Phase Change | 5 – 10 |
6. Airflow and Ventilation
Proper airflow and ventilation are essential for effective thermal management. Consider the following techniques:
- Incorporate fan-assisted cooling for high-power applications
- Design enclosures with adequate ventilation holes or grills
- Optimize component placement to promote natural convection
7. Board Material Selection
The choice of PCB material can significantly impact thermal performance. Some key considerations include:
- Use high thermal conductivity materials like aluminum or copper core PCBs for better heat dissipation
- Consider using low-loss dielectrics to minimize heat generation
- Evaluate the thermal expansion coefficients of materials to ensure compatibility
PCB Material | Thermal Conductivity (W/mK) |
---|---|
FR-4 | 0.3 |
Aluminum Core | 150 – 200 |
Copper Core | 380 – 400 |
8. Thermal Simulation and Analysis
Conducting thermal simulations and analyses during the design phase can help identify potential thermal issues early on. Use specialized software tools to:
- Analyze heat distribution and identify hot spots
- Evaluate the effectiveness of cooling solutions
- Optimize component placement and PCB layout for better thermal performance
9. Thermal Monitoring and Protection
Incorporating thermal monitoring and protection features can help prevent thermal runaway and ensure safe operation. Consider the following:
- Use temperature sensors to monitor critical components
- Implement thermal shutdown or throttling mechanisms to protect against overheating
- Incorporate thermal fuses or cutoffs for added safety
10. Conformal Coating
Conformal coating is a thin, protective layer applied to the PCB surface to protect against environmental factors like moisture and contaminants. While primarily used for protection, some conformal coatings also offer thermal benefits:
- Choose a conformal coating with good thermal conductivity
- Ensure uniform coating thickness for optimal performance
- Consider the impact on component cooling when selecting a coating material
11. Thermal Pad Design
Thermal pads are conductive areas on the PCB that help transfer heat from components to the board or heatsink. Proper thermal pad design is crucial for effective heat dissipation:
- Size thermal pads appropriately based on component power dissipation
- Ensure good contact between the component and thermal pad
- Consider using thermal vias to enhance heat transfer
12. Thermal Isolation
In some cases, it may be necessary to thermally isolate sensitive components from heat sources. Techniques for thermal isolation include:
- Using thermal barriers or insulating materials
- Placing sensitive components on separate PCB layers
- Incorporating air gaps or trenches to reduce heat transfer
13. Active Cooling Solutions
For high-power applications or environments with limited natural convection, active cooling solutions may be necessary. Some options include:
- Forced air cooling using fans or blowers
- Liquid cooling systems with heat exchangers
- Thermoelectric coolers (TECs) for precise temperature control
14. Thermal Management in High-Density PCBs
As PCBs become more compact and high-density, thermal management becomes increasingly challenging. Techniques for managing heat in high-density designs include:
- Using embedded heat pipes or vapor chambers for efficient heat transfer
- Implementing 3D PCB design techniques to optimize component placement
- Utilizing advanced packaging technologies like chip-on-board (COB) or flip-chip
15. Collaboration and Communication
Effective thermal management requires collaboration and communication among various stakeholders, including PCB designers, component manufacturers, and thermal engineers. Ensure that:
- Thermal requirements and constraints are clearly communicated
- Regular design reviews are conducted to address thermal concerns
- Manufacturers provide accurate thermal data for components
Frequently Asked Questions (FAQ)
1. What is the most important factor in PCB thermal management?
The most important factor in PCB thermal management is identifying and addressing the primary heat sources on the board. This involves understanding the power dissipation of components, their placement, and the overall heat distribution across the PCB. By focusing on the main heat generators, designers can implement targeted cooling solutions for optimal thermal performance.
2. How do I choose the right heatsink for my PCB?
Choosing the right heatsink depends on several factors, including the component’s power dissipation, available space, and the desired cooling performance. Consider the following steps:
- Calculate the component’s power dissipation and determine the required thermal resistance of the heatsink.
- Evaluate the available space and any size constraints for the heatsink.
- Select a heatsink material with good thermal conductivity, such as aluminum or copper.
- Consider the heatsink’s surface area and fin design for optimal heat dissipation.
- Ensure proper thermal interface material between the component and heatsink.
3. Can I use thermal simulation software to predict PCB thermal performance?
Yes, thermal simulation software is a valuable tool for predicting PCB thermal performance. These tools allow designers to analyze heat distribution, identify potential thermal issues, and evaluate the effectiveness of cooling solutions before physical prototyping. Some popular thermal simulation software packages include:
- Ansys Icepak
- Mentor Graphics FloTHERM
- Autodesk Fusion 360
- SolidWorks Flow Simulation
By using thermal simulation software, designers can optimize PCB layouts, component placement, and cooling strategies for improved thermal management.
4. What are the benefits of using a copper core PCB for thermal management?
Copper core PCBs offer several benefits for thermal management compared to traditional FR-4 PCBs:
- Higher thermal conductivity: Copper has a thermal conductivity of around 400 W/mK, compared to 0.3 W/mK for FR-4. This allows for more efficient heat dissipation across the board.
- Better temperature uniformity: The high thermal conductivity of copper helps distribute heat evenly, reducing hot spots and thermal gradients.
- Improved mechanical stability: Copper core PCBs have better dimensional stability and less warping under thermal stress.
- Enhanced electrical performance: The copper core acts as a large ground plane, providing better signal integrity and EMI shielding.
However, copper core PCBs are more expensive and may require specialized manufacturing processes compared to traditional FR-4 PCBs.
5. How do I ensure proper thermal management in high-density PCB designs?
High-density PCB designs pose unique challenges for thermal management due to the close proximity of components and limited space for cooling solutions. To ensure proper thermal management in high-density designs:
- Optimize component placement to distribute heat evenly and avoid hot spots.
- Use thermal vias strategically to transfer heat from components to other layers or heatsinks.
- Consider advanced PCB materials with higher thermal conductivity, such as aluminum or copper core PCBs.
- Implement embedded heat pipes or vapor chambers for efficient heat transfer in limited spaces.
- Utilize 3D PCB design techniques to optimize component placement and cooling paths.
- Incorporate active cooling solutions, such as forced air or liquid cooling, for high-power components.
- Conduct thorough thermal simulations and analyses to identify and address potential thermal issues early in the design phase.
By following these guidelines and carefully considering the unique thermal requirements of high-density PCBs, designers can ensure optimal thermal management and reliable performance.
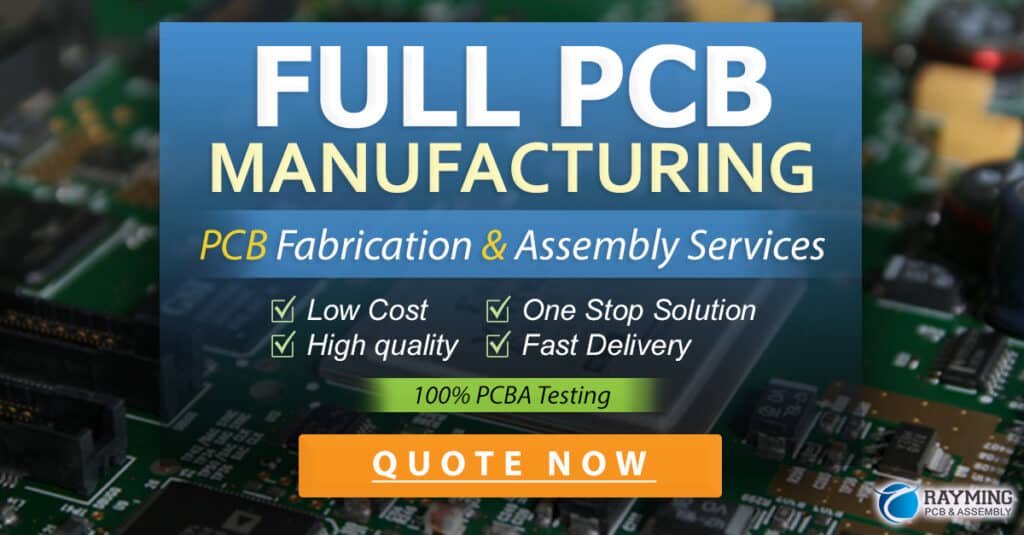
Conclusion
Effective thermal management is essential for ensuring the reliability, performance, and longevity of PCBs. By implementing the 15 techniques discussed in this article, designers can optimize thermal PCB design and improve overall thermal management. From strategic component placement and copper plane usage to advanced cooling solutions and thermal simulation, a comprehensive approach to thermal management is crucial for success.
As electronic devices continue to push the boundaries of performance and miniaturization, the importance of thermal management will only continue to grow. By staying informed about the latest techniques and technologies, PCB designers can meet the evolving thermal challenges and deliver reliable, high-performance products.
Leave a Reply