Introduction to HDI Materials
High Density Interconnect (HDI) materials are essential components in modern electronics manufacturing. These materials enable the creation of compact, high-performance devices by allowing for increased circuit density and improved signal integrity. As the demand for smaller, more powerful electronic devices continues to grow, understanding the various HDI materials available and their properties is crucial for designers and manufacturers.
In this article, we will explore 11 essential HDI materials you need to know, their characteristics, and their applications in the electronics industry. We will also discuss the advantages and disadvantages of each material and provide insights into selecting the right HDI material for your specific project requirements.
1. Copper Clad Laminates (CCL)
Copper Clad Laminates (CCLs) are the foundation of HDI printed circuit boards (PCBs). These materials consist of a dielectric substrate, such as FR-4, bonded with a thin layer of copper on one or both sides. CCLs provide the base for creating conductive traces and pads on the PCB.
Advantages of CCLs
- Good thermal stability
- Excellent mechanical strength
- High electrical insulation properties
- Wide range of dielectric constants available
Disadvantages of CCLs
- Limited flexibility
- Higher cost compared to other base materials
- Requires additional processing steps for HDI applications
2. Prepregs
Prepregs, short for pre-impregnated materials, are used in the fabrication of multilayer PCBs. These materials consist of a reinforcement fabric, such as glass or aramid fibers, pre-impregnated with a partially cured thermoset resin. Prepregs are used to bond the layers of a multilayer PCB together during the lamination process.
Advantages of Prepregs
- Excellent dimensional stability
- Good thermal resistance
- High mechanical strength
- Allows for the creation of complex multilayer structures
Disadvantages of Prepregs
- Limited shelf life due to partial curing
- Requires precise control of lamination parameters
- Higher cost compared to other bonding materials
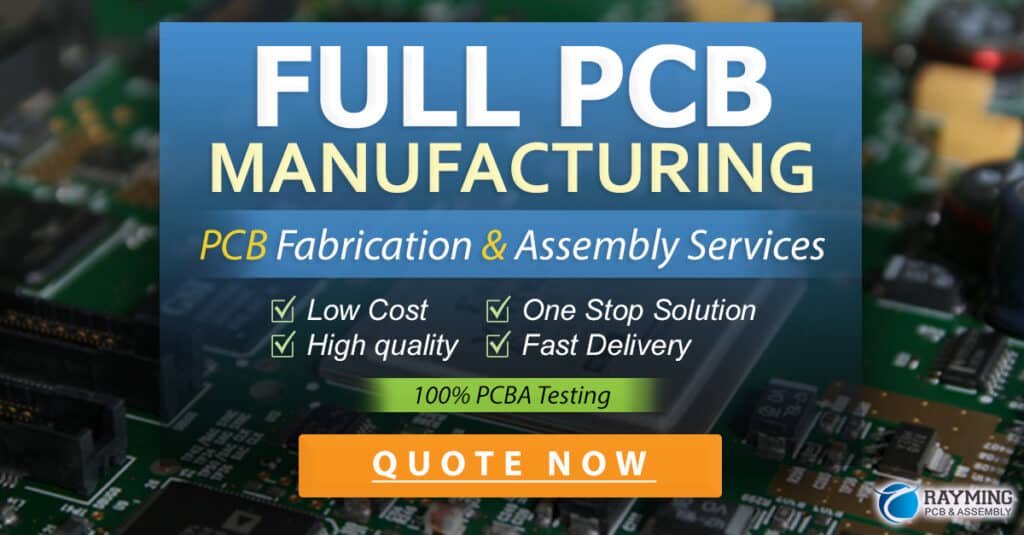
3. Solder Mask
Solder mask, also known as solder resist, is a protective coating applied to the surface of a PCB. It serves to protect the copper traces from oxidation, prevent solder bridges during assembly, and provide electrical insulation between components. In HDI applications, solder mask plays a crucial role in maintaining signal integrity and reliability.
Advantages of Solder Mask
- Protects copper traces from oxidation and damage
- Prevents solder bridging during assembly
- Provides electrical insulation between components
- Enhances the appearance of the PCB
Disadvantages of Solder Mask
- Adds additional thickness to the PCB
- May require specialized application techniques for HDI designs
- Can impact the impedance of high-frequency signals
4. Flexible Substrates
Flexible substrates, such as polyimide (PI) and polyethylene terephthalate (PET), are used in the production of flexible and rigid-flex PCBs. These materials offer excellent mechanical and electrical properties, making them suitable for applications that require bendability or conformity to irregular shapes.
Advantages of Flexible Substrates
- Enables the creation of flexible and rigid-flex PCBs
- Excellent mechanical properties, including high tensile strength and elongation
- Good thermal and chemical resistance
- Lightweight and thin, allowing for compact designs
Disadvantages of Flexible Substrates
- Higher cost compared to rigid substrates
- Requires specialized processing techniques
- May have limitations in terms of layer count and component placement
5. Adhesives
Adhesives play a vital role in the assembly and bonding of HDI components. These materials are used to attach components to the PCB, provide mechanical support, and ensure reliable electrical connections. Common adhesives used in HDI applications include epoxies, acrylics, and silicones.
Advantages of Adhesives
- Enables secure attachment of components to the PCB
- Provides mechanical support and strain relief
- Enhances thermal dissipation in some cases
- Allows for the use of diverse component packages
Disadvantages of Adhesives
- May require specialized application techniques
- Can impact the electrical performance of high-frequency signals
- Some adhesives may have limited temperature resistance
6. Anisotropic Conductive Film (ACF)
Anisotropic Conductive Film (ACF) is a specialized adhesive material used for connecting fine-pitch components, such as chip-on-glass (COG) and chip-on-flex (COF) assemblies. ACF contains conductive particles suspended in an insulating adhesive matrix, allowing for electrical conductivity in the z-axis while maintaining insulation in the x and y axes.
Advantages of ACF
- Enables high-density interconnections for fine-pitch components
- Provides both electrical and mechanical bonding
- Allows for lower bonding temperatures compared to soldering
- Suitable for flexible and transparent substrate applications
Disadvantages of ACF
- Requires precise alignment and bonding parameters
- Limited current-carrying capacity compared to soldered connections
- May be susceptible to thermal cycling fatigue
7. Underfill Materials
Underfill materials are used to fill the gap between a chip and the substrate in flip-chip assemblies. These materials provide mechanical support, reduce stress on the solder joints, and improve thermal dissipation. Underfill materials are crucial for ensuring the reliability and longevity of HDI flip-chip assemblies.
Advantages of Underfill Materials
- Reduces stress on solder joints, improving reliability
- Provides mechanical support to the chip
- Enhances thermal dissipation
- Protects the active surface of the chip from environmental factors
Disadvantages of Underfill Materials
- Requires additional processing steps
- Can be time-consuming to apply, especially for large dies
- May impact the reworkability of the assembly
8. Embedded Capacitor Materials
Embedded capacitor materials are used to create integrated passive components within the layers of an HDI PCB. These materials typically consist of a high-dielectric constant ceramic powder suspended in a polymer matrix. Embedding capacitors within the PCB reduces the need for discrete components, saving space and improving electrical performance.
Advantages of Embedded Capacitor Materials
- Reduces the need for discrete capacitors, saving board space
- Improves electrical performance by reducing parasitic inductance
- Enhances power distribution network (PDN) performance
- Enables more compact and efficient designs
Disadvantages of Embedded Capacitor Materials
- Requires specialized manufacturing processes
- May increase the cost of the PCB
- Limits the range of capacitance values available
9. High-Frequency Laminates
High-frequency laminates are specialized materials designed for use in high-speed, high-frequency applications, such as 5G networks and automotive radar systems. These materials offer low dielectric loss, stable dielectric constant, and controlled impedance, enabling the transmission of high-frequency signals with minimal distortion.
Advantages of High-Frequency Laminates
- Low dielectric loss, minimizing signal attenuation
- Stable dielectric constant over a wide frequency range
- Enables controlled impedance designs
- Suitable for high-speed, high-frequency applications
Disadvantages of High-Frequency Laminates
- Higher cost compared to standard laminates
- May require specialized processing techniques
- Limited availability and longer lead times
10. Thermal Interface Materials (TIMs)
Thermal Interface Materials (TIMs) are used to enhance heat transfer between components and heat sinks in HDI assemblies. These materials fill the air gaps between mating surfaces, reducing thermal resistance and improving overall thermal management. Common TIMs include thermal greases, pads, and phase change materials.
Advantages of TIMs
- Enhances heat transfer between components and heat sinks
- Reduces thermal resistance, improving overall thermal management
- Helps maintain component temperatures within acceptable limits
- Extends the lifespan of temperature-sensitive components
Disadvantages of TIMs
- Requires careful application to ensure optimal performance
- Some TIMs may degrade over time, requiring periodic replacement
- May add additional assembly steps and costs
11. 3D Printing Materials
3D printing materials, such as conductive filaments and resins, are emerging as potential solutions for creating HDI structures and components. These materials enable the rapid prototyping and production of complex geometries, opening up new possibilities for HDI design and manufacturing.
Advantages of 3D Printing Materials
- Enables rapid prototyping and iteration of HDI designs
- Allows for the creation of complex geometries and structures
- Reduces lead times and tooling costs for low-volume production
- Offers the potential for customization and personalization
Disadvantages of 3D Printing Materials
- Limited material options compared to traditional HDI materials
- May have lower electrical and mechanical performance
- Requires specialized 3D printing equipment and expertise
- Limited scalability for high-volume production
Frequently Asked Questions (FAQ)
1. What are the key considerations when selecting an HDI material?
When selecting an HDI material, key considerations include:
– Electrical properties (dielectric constant, loss tangent, etc.)
– Thermal properties (glass transition temperature, thermal conductivity, etc.)
– Mechanical properties (tensile strength, flexural strength, etc.)
– Compatibility with the desired manufacturing processes
– Cost and availability
– Compliance with relevant industry standards and regulations
It is essential to carefully evaluate the specific requirements of your application and consult with material suppliers and industry experts to make an informed decision.
2. Can HDI materials be used for high-temperature applications?
Yes, certain HDI materials are suitable for high-temperature applications. These materials typically have a high glass transition temperature (Tg) and good thermal stability. Examples of high-temperature HDI materials include:
– Polyimide (PI) laminates and adhesives
– High-Tg FR-4 laminates
– Ceramic-based substrates, such as low-temperature co-fired ceramic (LTCC)
When selecting HDI materials for high-temperature applications, it is crucial to consider the maximum operating temperature, duration of exposure, and any additional environmental factors that may impact the material’s performance.
3. How do embedded capacitor materials compare to discrete capacitors?
Embedded capacitor materials offer several advantages over discrete capacitors in HDI applications:
– Space savings: Embedding capacitors within the PCB layers frees up surface space for other components.
– Improved electrical performance: Embedded capacitors have lower parasitic inductance, enhancing power distribution network (PDN) performance and reducing signal distortion.
– Increased reliability: Embedded capacitors are less susceptible to mechanical stress and vibration compared to surface-mounted discrete capacitors.
However, embedded capacitor materials may have limitations in terms of the range of capacitance values available and may require specialized manufacturing processes, which can increase costs. Discrete capacitors still play a crucial role in many HDI designs, particularly for applications requiring high capacitance values or specific performance characteristics.
4. Are 3D printing materials suitable for production-grade HDI applications?
Currently, 3D printing materials are primarily used for prototyping and low-volume production of HDI components and structures. While these materials offer unique advantages in terms of design flexibility and rapid iteration, they may have limitations in terms of electrical and mechanical performance compared to traditional HDI materials.
As 3D printing technologies and materials continue to evolve, it is expected that their use in production-grade HDI applications will increase. However, it is essential to carefully evaluate the specific requirements of your application and conduct thorough testing and validation before implementing 3D printing materials in production-grade HDI designs.
5. How can I ensure the reliability of my HDI assembly?
To ensure the reliability of your HDI assembly, consider the following best practices:
– Select materials that are compatible with your application requirements and manufacturing processes.
– Follow recommended design guidelines for HDI, including trace width and spacing, via size and placement, and component layout.
– Use appropriate surface finishes and coatings to protect against environmental factors, such as moisture and corrosion.
– Implement robust testing and quality control procedures, including visual inspection, electrical testing, and environmental stress testing.
– Partner with experienced HDI manufacturers and assembly providers who have a proven track record of delivering reliable, high-quality products.
By adhering to these best practices and working closely with industry experts, you can significantly improve the reliability and longevity of your HDI assemblies.
Conclusion
Understanding the various HDI materials available and their properties is essential for designing and manufacturing high-performance electronic devices. From copper clad laminates and prepregs to flexible substrates and embedded capacitor materials, each HDI material plays a crucial role in ensuring the reliability, functionality, and efficiency of modern electronics.
When selecting HDI materials for your application, it is essential to consider factors such as electrical and thermal properties, mechanical strength, compatibility with manufacturing processes, and cost. By carefully evaluating your specific requirements and consulting with industry experts, you can make informed decisions that optimize the performance and reliability of your HDI assemblies.
As technology continues to advance and new materials emerge, staying up-to-date with the latest developments in HDI materials is crucial for staying competitive in the rapidly evolving electronics industry. By understanding the advantages and disadvantages of each material and implementing best practices in design and manufacturing, you can unlock the full potential of HDI technology and create innovative, high-performance electronic devices that meet the demands of today’s market.
Material | Advantages | Disadvantages |
---|---|---|
Copper Clad Laminates (CCL) | – Good thermal stability – Excellent mechanical strength – High electrical insulation properties – Wide range of dielectric constants available |
– Limited flexibility – Higher cost compared to other base materials – Requires additional processing steps for HDI applications |
Prepregs | – Excellent dimensional stability – Good thermal resistance – High mechanical strength – Allows for the creation of complex multilayer structures |
– Limited shelf life due to partial curing – Requires precise control of lamination parameters – Higher cost compared to other bonding materials |
Solder Mask | – Protects copper traces from oxidation and damage – Prevents solder bridging during assembly – Provides electrical insulation between components – Enhances the appearance of the PCB |
– Adds additional thickness to the PCB – May require specialized application techniques for HDI designs – Can impact the impedance of high-frequency signals |
Flexible Substrates | – Enables the creation of flexible and rigid-flex PCBs – Excellent mechanical properties, including high tensile strength and elongation – Good thermal and chemical resistance – Lightweight and thin, allowing for compact designs |
– Higher cost compared to rigid substrates – Requires specialized processing techniques – May have limitations in terms of layer count and component placement |
Adhesives | – Enables secure attachment of components to the PCB – Provides mechanical support and strain relief – Enhances thermal dissipation in some cases – Allows for the use of diverse component packages |
– May require specialized application techniques – Can impact the electrical performance of high-frequency signals – Some adhesives may have limited temperature resistance |
Anisotropic Conductive Film (ACF) | – Enables high-density interconnections for fine-pitch components – Provides both electrical and mechanical bonding – Allows for lower bonding temperatures compared to soldering – Suitable for flexible and transparent substrate applications |
– Requires precise alignment and bonding parameters – Limited current-carrying capacity compared to soldered connections – May be susceptible to thermal cycling fatigue |
Underfill Materials | – Reduces stress on solder joints, improving reliability – Provides mechanical support to the chip – Enhances thermal dissipation – Protects the active surface of the chip from environmental factors |
– Requires additional processing steps – Can be time-consuming to apply, especially for large dies – May impact the reworkability of the assembly |
Embedded Capacitor Materials | – Reduces the need for discrete capacitors, saving board space – Improves electrical performance by reducing parasitic inductance – Enhances power distribution network (PDN) performance – Enables more compact and efficient designs |
– Requires specialized manufacturing processes – May increase the cost of the PCB – Limits the range of capacitance values available |
High-Frequency Laminates | – Low dielectric loss, minimizing signal attenuation – Stable dielectric constant over a wide frequency range – Enables controlled impedance designs – Suitable for high-speed, high-frequency applications |
– Higher cost compared to standard laminates – May require specialized processing techniques – Limited availability and longer lead times |
Thermal Interface Materials (TIMs) | – Enhances heat transfer between components and heat sinks – Reduces thermal resistance, improving overall thermal management – Helps maintain component temperatures within acceptable limits – Extends the lifespan of temperature-sensitive components |
– Requires careful application to ensure optimal performance – Some TIMs may degrade over time, requiring periodic replacement – May add additional assembly steps and costs |
3D Printing Materials | – Enables rapid prototyping and iteration of HD |
Leave a Reply