Introduction
A Passive Distribution Network (PDN) is a critical component in modern electronic systems, responsible for delivering clean and stable power to various components on a printed circuit board (PCB). A well-designed PDN ensures that the system functions reliably and meets performance requirements. However, a poorly designed PDN can lead to various issues, such as signal integrity problems, electromagnetic interference (EMI), and even device failure. In this article, we will discuss 10 symptoms of a bad PDN and how to identify and address these issues.
What is a Passive Distribution Network (PDN)?
A Passive Distribution Network (PDN) is a network of passive components, such as capacitors, inductors, and resistors, that distribute power from the power supply to the various components on a PCB. The primary goal of a PDN is to provide a low-impedance path for the power supply current while minimizing voltage fluctuations and noise.
A typical PDN consists of the following components:
Component | Description |
---|---|
Power planes | Copper layers on the PCB that distribute power to components |
Decoupling capacitors | Capacitors placed near power-consuming components to provide local energy storage and reduce voltage fluctuations |
Bulk capacitors | Larger capacitors used to store energy and stabilize the power supply voltage |
Ferrite beads | Inductors used to filter out high-frequency noise |
Voltage regulators | Devices that maintain a constant output voltage despite variations in the input voltage or load current |
The Importance of a Well-Designed PDN
A well-designed PDN is crucial for ensuring the proper functioning and reliability of electronic systems. Some of the key benefits of a good PDN include:
- Reduced voltage fluctuations: A good PDN minimizes voltage variations, ensuring that components receive a stable power supply.
- Improved signal integrity: By reducing noise and voltage fluctuations, a well-designed PDN helps maintain signal integrity and reduces the likelihood of data errors.
- Enhanced EMI performance: A properly designed PDN can help mitigate electromagnetic interference (EMI) by filtering out high-frequency noise and preventing it from coupling with other signals.
- Increased system reliability: By providing clean and stable power to components, a good PDN contributes to overall system reliability and reduces the risk of device failure.
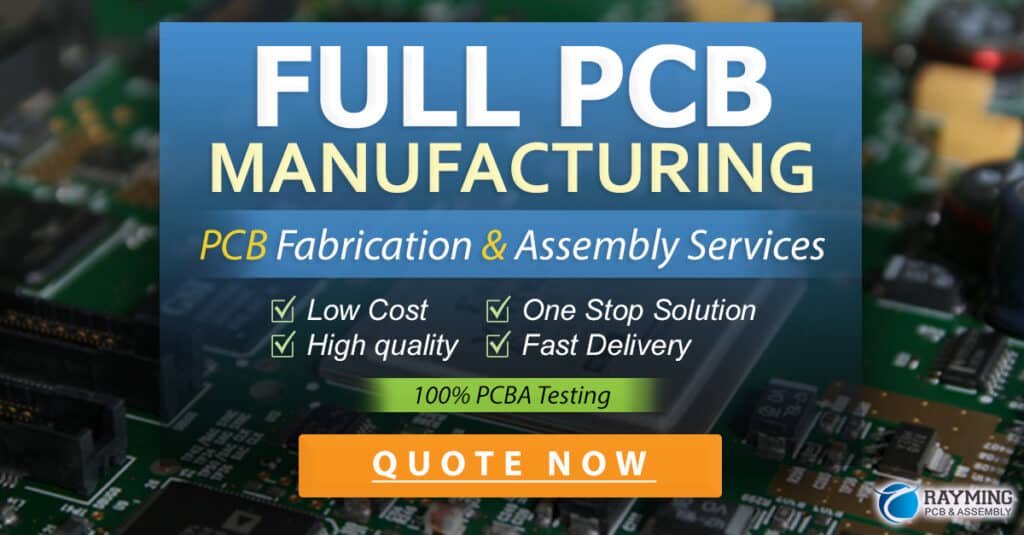
10 Symptoms of a Bad PDN
1. Excessive Voltage Ripple
Voltage ripple refers to the AC component of the DC power supply voltage. Excessive voltage ripple is a common symptom of a bad PDN and can be caused by insufficient decoupling capacitance, high-frequency noise, or poor power plane design. Voltage ripple can lead to signal integrity issues, increased EMI, and even device failure.
To identify voltage ripple, you can use an oscilloscope to measure the power supply voltage at various points on the PCB. If the ripple exceeds the specified limits for your components, it indicates a problem with the PDN.
Solutions for Excessive Voltage Ripple
- Add more decoupling capacitors: Increase the number or capacity of decoupling capacitors near power-consuming components to provide local energy storage and reduce voltage fluctuations.
- Optimize power plane design: Ensure that power planes have sufficient copper coverage and are properly segmented to minimize impedance and reduce voltage ripple.
- Use low-esr capacitors: Select capacitors with low equivalent series resistance (ESR) to minimize the voltage drop across the capacitor and improve its ability to suppress high-frequency noise.
2. Power Supply Noise
Power supply noise refers to unwanted high-frequency fluctuations in the power supply voltage. These fluctuations can be caused by switching noise from voltage regulators, digital logic transitions, or external sources such as nearby electronic devices. Power supply noise can couple with sensitive analog or digital signals, leading to signal integrity issues and decreased system performance.
To detect power supply noise, use a spectrum analyzer or an oscilloscope with FFT (Fast Fourier Transform) capability to measure the frequency content of the power supply voltage.
Solutions for Power Supply Noise
- Use noise-filtering components: Incorporate ferrite beads, LC filters, or pi-filters into the PDN to attenuate high-frequency noise.
- Implement proper grounding techniques: Ensure that the PCB has a solid ground plane and that components are properly grounded to minimize ground loops and reduce noise coupling.
- Isolate sensitive circuits: Physically separate sensitive analog or digital circuits from noisy power supplies or high-speed digital logic to minimize noise coupling.
3. Ground Bounce
Ground bounce occurs when there are rapid changes in the current flowing through the ground plane, causing the ground voltage to fluctuate. This is often caused by simultaneous switching of multiple digital outputs, leading to a sudden increase in current demand. Ground bounce can cause signal integrity issues, false triggering of logic devices, and increased EMI.
To identify ground bounce, use an oscilloscope to measure the voltage between the ground pins of affected components and a stable reference ground point.
Solutions for Ground Bounce
- Implement proper decoupling: Place decoupling capacitors close to the power pins of digital ICs to provide a local, low-impedance path for switching currents.
- Use ground planes: Incorporate a solid ground plane in the PCB design to minimize ground impedance and reduce ground bounce.
- Optimize component placement: Place high-speed digital components close to their decoupling capacitors and separate them from sensitive analog components to minimize noise coupling.
4. Electromagnetic Interference (EMI)
EMI refers to the unwanted coupling of electromagnetic energy from one component or circuit to another. A bad PDN can contribute to increased EMI by allowing high-frequency noise to propagate through the power and ground planes. This can lead to interference with nearby electronic devices, violation of EMC (Electromagnetic Compatibility) regulations, and decreased system performance.
To detect emi issues, use a spectrum analyzer or an EMI receiver to measure the electromagnetic emissions from the PCB or device.
Solutions for EMI
- Implement proper power plane segmentation: Divide the power plane into separate regions for analog and digital circuits, and use ferrite beads or inductors to isolate these regions and prevent noise propagation.
- Use shielding techniques: Incorporate shielding materials, such as copper tape or conductive elastomers, to contain electromagnetic emissions from high-noise components.
- Optimize component placement and routing: Place components and route traces in a manner that minimizes loop areas and reduces the coupling of high-frequency noise.
5. Inadequate Decoupling
Decoupling capacitors are used to provide local energy storage and maintain a stable power supply voltage for components. Inadequate decoupling can lead to voltage fluctuations, increased power supply noise, and signal integrity issues.
To identify inadequate decoupling, use an impedance analyzer or a vector network analyzer (VNA) to measure the impedance of the PDN across a range of frequencies. If the impedance is too high at certain frequencies, it indicates insufficient decoupling.
Solutions for Inadequate Decoupling
- Add more decoupling capacitors: Increase the number or capacity of decoupling capacitors near power-consuming components to provide adequate local energy storage.
- Use a variety of capacitor values: Incorporate a mix of capacitor values (e.g., bulk, ceramic, and small-value capacitors) to provide effective decoupling across a wide frequency range.
- Minimize capacitor parasitic inductance: Select capacitors with low equivalent series inductance (ESL) and place them close to the power pins of components to minimize the parasitic inductance in the decoupling path.
6. Resonance Issues
Resonance occurs when the inductive and capacitive elements in the PDN form a resonant circuit, leading to impedance peaks at specific frequencies. These impedance peaks can amplify power supply noise, cause voltage fluctuations, and degrade signal integrity.
To identify resonance issues, use an impedance analyzer or a VNA to measure the impedance of the PDN across a range of frequencies. Impedance peaks at specific frequencies indicate resonance problems.
Solutions for Resonance Issues
- Optimize capacitor selection and placement: Choose capacitors with appropriate values and place them strategically to minimize the formation of resonant circuits.
- Use damping techniques: Incorporate damping resistors or ferrite beads in series with decoupling capacitors to reduce the quality factor (Q) of resonant circuits and suppress impedance peaks.
- Implement power plane segmentation: Divide the power plane into separate regions with different resonant frequencies to prevent the formation of a single, large resonant circuit.
7. Insufficient Copper Coverage
Insufficient copper coverage in the power and ground planes can lead to increased impedance, voltage drops, and voltage fluctuations. This can cause signal integrity issues, increased EMI, and decreased system performance.
To identify insufficient copper coverage, review the PCB layout and use pcb design software to calculate the current density and voltage drop in the power and ground planes.
Solutions for Insufficient Copper Coverage
- Increase copper thickness: Use thicker copper layers in the PCB to reduce impedance and improve current-carrying capacity.
- Optimize power plane design: Ensure that power planes have sufficient copper coverage and are properly segmented to minimize impedance and reduce voltage drops.
- Use multiple power and ground planes: Incorporate multiple power and ground planes in the PCB stackup to increase copper coverage and reduce impedance.
8. Poor Via Placement
Vias are used to connect components and different layers of the PCB. Poor via placement can lead to increased inductance, impedance discontinuities, and signal integrity issues. This can cause reflections, crosstalk, and increased EMI.
To identify poor via placement, review the PCB layout and use signal integrity simulation tools to analyze the impact of via placement on signal quality.
Solutions for Poor Via Placement
- Optimize via placement: Place vias close to the power pins of components to minimize the inductance in the power delivery path.
- Use via stitching: Implement via stitching techniques, such as placing multiple vias in parallel or using arrays of small vias, to reduce via inductance and improve current-carrying capacity.
- Minimize via stubs: Ensure that via stubs (the unused portion of a via) are as short as possible to reduce impedance discontinuities and reflections.
9. Incorrect Plane Stackup
The arrangement of power, ground, and signal layers in a PCB, known as the stackup, can significantly impact the performance of the PDN. An incorrect plane stackup can lead to increased impedance, crosstalk, and signal integrity issues.
To identify incorrect plane stackup, review the PCB stackup design and use PCB design software to simulate the performance of the PDN and analyze the impact of the stackup on impedance and signal quality.
Solutions for Incorrect Plane Stackup
- Follow best practices for stackup design: Adhere to industry-standard stackup configurations, such as alternating power and ground layers, to minimize impedance and reduce crosstalk.
- Use appropriate dielectric materials: Select dielectric materials with suitable properties, such as low dielectric constant and low loss tangent, to minimize signal loss and improve PDN performance.
- Optimize layer spacing: Adjust the spacing between layers to control impedance and minimize crosstalk while ensuring manufacturability.
10. Thermal Issues
Thermal issues, such as excessive heat generation or inadequate heat dissipation, can impact the performance and reliability of the PDN. High temperatures can cause increased resistance in conductors, reduced capacitor performance, and accelerated component aging.
To identify thermal issues, use thermal imaging cameras or temperature sensors to measure the temperature distribution on the PCB and identify hot spots.
Solutions for Thermal Issues
- Improve heat dissipation: Incorporate heat sinks, thermal vias, or other heat dissipation techniques to remove heat from high-power components and distribute it evenly across the PCB.
- Optimize component placement: Place high-power components away from temperature-sensitive devices and ensure adequate spacing to facilitate heat dissipation.
- Use temperature-stable components: Select components with appropriate temperature ratings and stability to ensure reliable operation over the expected temperature range.
Frequently Asked Questions (FAQ)
1. What is the difference between a good PDN and a bad PDN?
A good PDN provides a low-impedance, stable power delivery path to components, minimizing voltage fluctuations, noise, and EMI. A bad PDN, on the other hand, can lead to excessive voltage ripple, power supply noise, ground bounce, and other issues that degrade signal integrity and system performance.
2. How can I measure the impedance of my PDN?
To measure the impedance of your PDN, you can use an impedance analyzer or a vector network analyzer (VNA). These instruments can measure the impedance of the PDN across a range of frequencies, allowing you to identify impedance peaks, resonance issues, and insufficient decoupling.
3. What is the importance of decoupling capacitors in a PDN?
Decoupling capacitors are critical components in a PDN that provide local energy storage and maintain a stable power supply voltage for components. They help to reduce voltage fluctuations, suppress high-frequency noise, and minimize the impact of sudden current demands from digital logic transitions.
4. How can I reduce EMI in my PDN?
To reduce EMI in your PDN, you can implement several techniques, such as proper power plane segmentation, shielding, optimizing component placement and routing, and using noise-filtering components like ferrite beads or LC filters. Additionally, following best practices for grounding and decoupling can help minimize noise coupling and reduce EMI.
5. What are the consequences of a bad PDN in my electronic system?
A bad PDN can lead to various issues in your electronic system, such as signal integrity problems, increased EMI, reduced system performance, and even device failure. These issues can manifest as data errors, false triggering of logic devices, violation of EMC regulations, and decreased reliability. Addressing PDN issues early in the design process is crucial to ensure the proper functioning and longevity of your electronic system.
Conclusion
A well-designed Passive Distribution Network (PDN) is essential for ensuring the proper functioning, reliability, and performance of electronic systems. By understanding the 10 symptoms of a bad PDN and implementing appropriate solutions, designers can optimize their PDN design and mitigate issues such as excessive voltage ripple, power supply noise, ground bounce, EMI, and thermal problems.
To create a robust PDN, designers should follow best practices for component selection and placement, power plane design, decoupling, grounding, and stackup configuration. Additionally, using simulation tools and measurement techniques to analyze the performance of the PDN can help identify and address issues early in the design process.
By prioritizing PDN design and addressing the symptoms of a bad PDN, designers can create electronic systems that meet performance requirements, comply with EMC regulations, and provide reliable operation over the intended lifespan of the product.
Leave a Reply