Rule 1: Establish a Clear and Consistent Naming Convention
A clear and consistent naming convention is essential for effective data management in PCB Design. This includes naming conventions for files, folders, components, and nets. By establishing a standardized naming convention, you can:
- Improve communication among team members
- Reduce the risk of errors and confusion
- Streamline the design process
- Facilitate easier maintenance and updates
Here’s an example of a naming convention for PCB design files:
File Type | Naming Convention | Example |
---|---|---|
Schematic | ProjectName_RevisionNumber_Schematic | ABC_Rev1_Schematic |
PCB Layout | ProjectName_RevisionNumber_PCB | ABC_Rev1_PCB |
Bill of Materials (BOM) | ProjectName_RevisionNumber_BOM | ABC_Rev1_BOM |
Gerber Files | ProjectName_RevisionNumber_GerberFiles | ABC_Rev1_GerberFiles |
Rule 2: Use Version Control
Version control is a must-have for any PCB design project. It allows you to:
- Track changes made to design files
- Revert to previous versions if needed
- Collaborate with team members effectively
- Maintain a clear history of the project’s evolution
There are several version control systems available, such as Git, Subversion (SVN), and Mercurial. Choose one that suits your team’s needs and workflow.
Rule 3: Organize Your Files and Folders
Proper organization of your files and folders is crucial for efficient data management. Create a logical folder structure that reflects the various stages and components of your PCB design project. For example:
- ProjectName
- Schematics
- PCB_Layouts
- Libraries
- Components
- Footprints
- Documentation
- Manufacturing_Files
- Gerber_Files
- Drill_Files
- Assembly_Files
By organizing your files and folders in a clear and structured manner, you can easily locate and manage your design data.
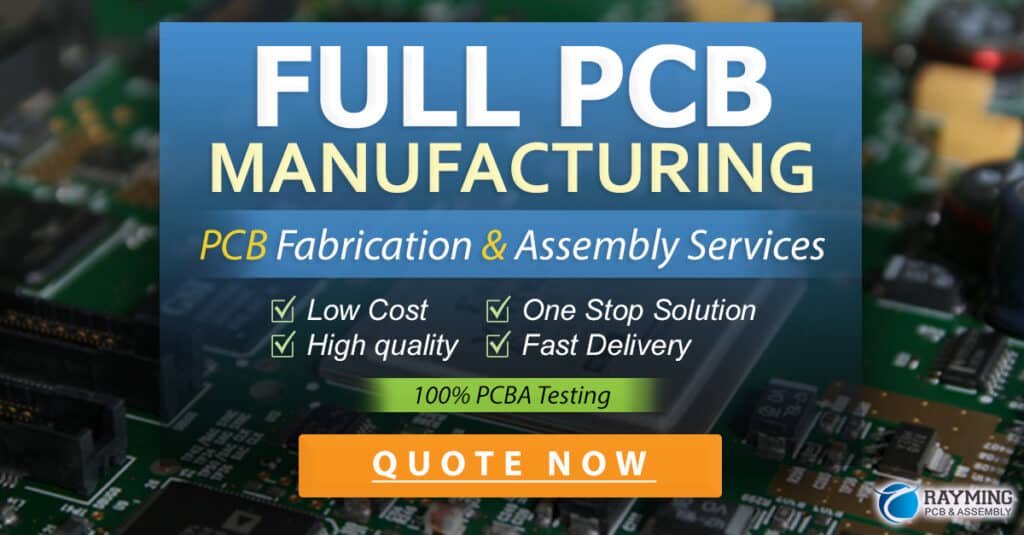
Rule 4: Maintain Accurate and Up-to-Date Libraries
Component libraries are the building blocks of your PCB design. Ensuring that your libraries are accurate and up-to-date is essential for avoiding design issues. Here are some best practices for library management:
- Use a centralized library management system
- Regularly update component information, such as footprints and symbols
- Verify component data against manufacturer datasheets
- Implement a review process for library updates
- Use a consistent naming convention for library elements
Rule 5: Document Your Design Decisions
Documentation is an integral part of PCB design data management. By documenting your design decisions, you can:
- Provide clarity for team members and stakeholders
- Facilitate easier troubleshooting and maintenance
- Ensure continuity in case of team member changes
- Streamline the design review process
Create design documentation that includes:
- Design specifications and requirements
- Schematic and PCB layout notes
- Component selection justifications
- Design rule checks (DRC) and electrical rule checks (ERC) reports
- Testing and validation procedures
Rule 6: Implement Design Reviews
Design reviews are essential for catching errors and ensuring that your PCB design meets the required specifications. Implement a formal design review process that includes:
- Schematic review
- PCB layout review
- Bill of Materials (BOM) review
- Manufacturing feasibility review
Involve relevant stakeholders, such as electrical engineers, PCB layout designers, and manufacturing experts, in the review process to ensure a comprehensive evaluation of your design.
Rule 7: Use Design Rule Checks (DRC) and Electrical Rule Checks (ERC)
Design Rule Checks (DRC) and Electrical Rule Checks (ERC) are automated tools that help you identify and correct design issues before moving to the manufacturing stage. These checks can detect problems such as:
- Clearance violations
- Trace width and spacing issues
- Unconnected nets
- Incorrect component placement
- Signal integrity issues
Regularly run DRC and ERC checks throughout the design process and address any flagged issues promptly.
Rule 8: Collaborate Effectively
Collaboration is key to successful PCB design projects. Implement tools and processes that facilitate effective collaboration among team members, such as:
- Cloud-based design platforms
- Real-time collaboration tools
- Clear communication channels
- Regular status meetings
- Design reviews and feedback sessions
By fostering a collaborative environment, you can ensure that all team members are working towards a common goal and that design issues are identified and addressed in a timely manner.
Rule 9: Manage Design Changes
Design changes are inevitable in any PCB design project. Implementing a robust change management process can help you:
- Track and document design changes
- Assess the impact of changes on the overall design
- Communicate changes to relevant stakeholders
- Ensure that changes are implemented correctly
Use a change request form or a similar tool to capture and manage design changes. This should include information such as:
- Description of the change
- Reason for the change
- Impact assessment
- Approval status
- Implementation plan
Rule 10: Perform Regular Data Backups
Data loss can be catastrophic for a PCB design project. Ensure that you have a regular backup process in place to protect your design data. This can include:
- Automated backup systems
- Cloud storage solutions
- Off-site data storage
- Regular testing of backup and restore procedures
By implementing a robust backup strategy, you can minimize the risk of data loss and ensure that your design data is always available when needed.
FAQ
Q1: What is the importance of a clear and consistent naming convention in PCB design?
A: A clear and consistent naming convention is essential for effective communication among team members, reducing the risk of errors, streamlining the design process, and facilitating easier maintenance and updates.
Q2: Why is version control important in PCB design?
A: Version control allows you to track changes made to design files, revert to previous versions if needed, collaborate with team members effectively, and maintain a clear history of the project’s evolution.
Q3: What are some best practices for managing component libraries in PCB design?
A: Best practices for managing component libraries include using a centralized library management system, regularly updating component information, verifying component data against manufacturer datasheets, implementing a review process for library updates, and using a consistent naming convention for library elements.
Q4: What should be included in PCB design documentation?
A: PCB design documentation should include design specifications and requirements, schematic and PCB layout notes, component selection justifications, design rule checks (DRC) and electrical rule checks (ERC) reports, and testing and validation procedures.
Q5: How can design changes be effectively managed in a PCB design project?
A: To effectively manage design changes, use a change request form or a similar tool to capture and manage design changes. This should include information such as a description of the change, reason for the change, impact assessment, approval status, and implementation plan. Regularly communicate changes to relevant stakeholders and ensure that changes are implemented correctly.
By following these ten rules for better data management in PCB design, you can avoid common issues, streamline your design process, and achieve successful outcomes. Remember to establish clear naming conventions, use version control, organize your files and folders, maintain accurate libraries, document your design decisions, implement design reviews, use automated checks, collaborate effectively, manage design changes, and perform regular data backups. By prioritizing data management, you can ensure that your PCB design projects are efficient, reliable, and successful.
Leave a Reply