Introduction to Designing Circuit Boards with Altium Designer
Altium Designer is a powerful and versatile software tool for designing printed circuit boards (PCBs). It offers a comprehensive set of features that enable engineers and designers to create high-quality, reliable, and efficient PCBs. Whether you are a beginner or an experienced designer, following these 10 easy steps will help you navigate the process of designing circuit boards using Altium Designer.
Step 1: Setting Up Your Altium Designer Project
Creating a New Project
To begin designing your circuit board, you first need to create a new project in Altium Designer. Follow these simple steps:
- Open Altium Designer
- Click on “File” in the top menu bar
- Select “New” and then “Project”
- Choose the project type (e.g., PCB Project) and give it a name
- Select the location where you want to save your project
- Click “OK” to create your new project
Configuring Project Settings
Once your project is created, it’s essential to configure the project settings to ensure consistency and accuracy throughout the design process. Some key settings to consider include:
- Units (e.g., metric or imperial)
- Grids and snap settings
- Default layer stack
- Design rules
- Output file formats
Step 2: Creating Your Schematic
Understanding schematic symbols
Before you start creating your schematic, it’s important to understand the various schematic symbols used to represent components. Some common symbols include:
Symbol | Component |
---|---|
Resistor | |
Capacitor | |
Inductor | |
Diode | |
Transistor |
Placing Components
To place components in your schematic:
- Open the Libraries panel
- Search for the desired component
- Drag and drop the component onto the schematic sheet
- Position the component and repeat the process for all necessary components
Wiring Components
Once your components are placed, you need to wire them together to create your circuit. To wire components:
- Select the “Wire” tool from the toolbar
- Click on the first component’s pin you want to connect
- Drag the wire to the second component’s pin and click to complete the connection
- Repeat the process for all necessary connections
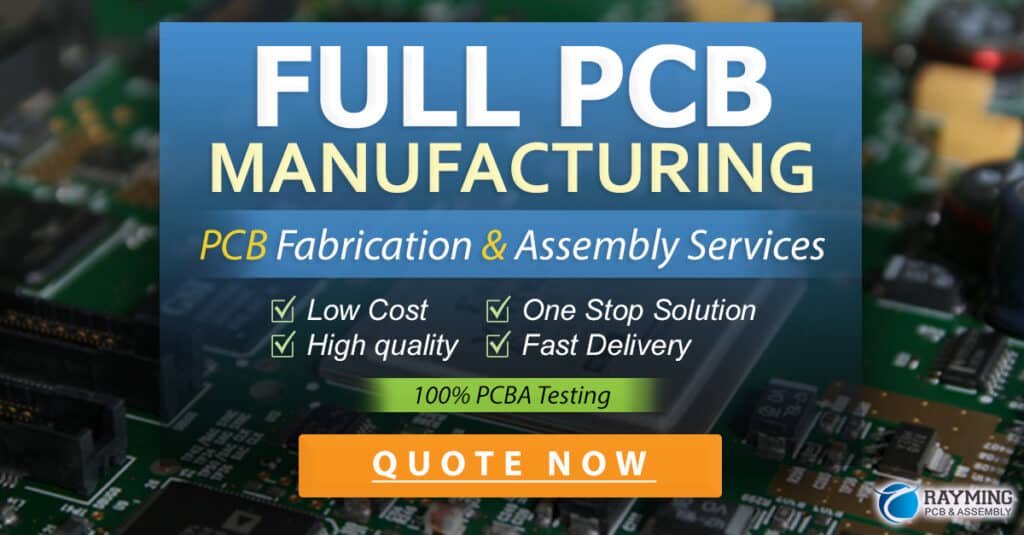
Step 3: Assigning Footprints
Understanding Footprints
Footprints are the physical representations of components on the PCB. They define the size, shape, and pin layout of each component. Assigning the correct footprint is crucial for ensuring proper component placement and PCB layout.
Associating Footprints with Components
To assign footprints to your components:
- Select a component in the schematic
- Right-click on the component and choose “Properties”
- In the properties window, select the “PCB” tab
- Click on the “Footprint” dropdown menu and select the appropriate footprint for the component
- Repeat the process for all components in your schematic
Step 4: Creating Your PCB Layout
Importing Your Schematic
To start your PCB layout, you need to import your schematic into the PCB editor. Follow these steps:
- In the project tree, right-click on your schematic file
- Select “Update PCB Document” and choose the PCB file you want to update
- Click “OK” to import the schematic changes into the PCB layout
Placing Components
Once your schematic is imported, you can begin placing components on the PCB. To place components:
- Select the “Move” tool from the toolbar
- Click on a component and drag it to the desired location on the PCB
- Use the “Rotate” tool to orient the component as needed
- Repeat the process for all components
Routing Traces
After placing your components, you need to route traces to connect them according to your schematic. To route traces:
- Select the “Route” tool from the toolbar
- Choose the appropriate routing layer and width
- Click on a component pad to start the trace
- Drag the trace to the destination pad and click to complete the connection
- Repeat the process for all necessary connections
Step 5: Applying Design Rules
Understanding Design Rules
Design rules are constraints that help ensure your PCB layout meets manufacturing requirements and functions as intended. Some common design rules include:
- Minimum trace width and spacing
- Minimum drill size and spacing
- copper pour clearance
- Silk screen clearance
Configuring Design Rules
To configure design rules in Altium Designer:
- Open the “Design” menu and select “Rules”
- In the Design Rule Editor, select the rule category you want to configure
- Set the desired constraints and values for each rule
- Click “Apply” to save your changes
Checking Design Rule Violations
To check for design rule violations:
- Open the “Tools” menu and select “Design Rule Check”
- Configure the rule check settings as needed
- Click “Run Design Rule Check”
- Review any violations and make necessary corrections to your PCB layout
Step 6: Adding Copper Pours
Understanding Copper Pours
Copper pours are solid areas of copper on your PCB that provide a low-impedance connection to ground or power planes. They help improve signal integrity, reduce EMI, and dissipate heat.
Creating Copper Pours
To create copper pours in Altium Designer:
- Select the “polygon Pour” tool from the toolbar
- Choose the appropriate layer and net for your copper pour
- Draw the outline of your copper pour on the PCB
- Right-click on the polygon and select “Properties”
- Configure the pour settings, such as clearance and thermal relief
- Repeat the process for additional copper pours as needed
Step 7: Generating Manufacturing Files
Understanding Manufacturing Files
Manufacturing files are the output files you send to your PCB manufacturer to fabricate your board. Common manufacturing files include:
- Gerber files (top and bottom layers, solder mask, silk screen)
- Drill files (NC Drill, Excellon)
- Pick and place files
- Bill of Materials (BOM)
Generating Manufacturing Files
To generate manufacturing files in Altium Designer:
- Open the “File” menu and select “Fabrication Outputs”
- Select the desired output format (e.g., Gerber, NC Drill)
- Configure the output settings, such as layer selection and file naming conventions
- Click “OK” to generate the files
- Repeat the process for all necessary manufacturing files
Step 8: Reviewing and Refining Your Design
Conducting a Design Review
Before finalizing your PCB design, it’s essential to conduct a thorough design review. A design review helps identify potential issues and ensure your design meets all requirements. Some key aspects to review include:
- Schematic accuracy
- Component placement and orientation
- Trace routing and spacing
- Design rule compliance
- Manufacturing feasibility
Making Design Refinements
Based on the findings of your design review, make any necessary refinements to your PCB layout. This may involve:
- Adjusting component placement
- Rerouting traces
- Modifying copper pours
- Updating design rules
- Regenerating manufacturing files
Step 9: Collaborating with Your Team
Sharing Your Design
Collaboration is key to successful PCB design projects. Altium Designer offers several tools for sharing your design with your team, including:
- Version control integration (e.g., SVN, Git)
- altium 365 cloud platform
- Exporting and importing design files
Reviewing and Commenting on Designs
When collaborating with your team, it’s important to have a process for reviewing and commenting on designs. Altium Designer provides features like:
- Design commenting and markup tools
- Altium 365 design reviews and discussions
- Change tracking and history
Step 10: Finalizing and Manufacturing Your PCB
Conducting a Final Design Review
Before sending your design to manufacturing, conduct a final design review to ensure all requirements are met and any issues have been resolved. This review should involve all relevant stakeholders, including:
- Electrical engineers
- Mechanical engineers
- PCB layout designers
- Manufacturing partners
Releasing Your Design for Manufacturing
Once your design has passed the final review, you can release it for manufacturing. This typically involves:
- Generating and packaging final manufacturing files
- Communicating with your manufacturing partner
- Providing any necessary documentation or instructions
- Tracking the manufacturing process and addressing any issues that arise
Frequently Asked Questions (FAQ)
1. What are the system requirements for running Altium Designer?
Altium Designer requires a 64-bit Windows operating system (Windows 10 or later) with at least 8 GB of RAM and 5 GB of free disk space. A dedicated graphics card with at least 1 GB of VRAM is also recommended.
2. How can I import existing schematic or PCB designs into Altium Designer?
Altium Designer supports importing design files from various other PCB design tools, such as Eagle, KiCad, and OrCAD. To import a design, go to “File” > “Open” and select the appropriate file format. Altium Designer will convert the design into its native format.
3. Can I create custom schematic symbols and PCB footprints in Altium Designer?
Yes, Altium Designer allows you to create custom schematic symbols and PCB footprints. To create a new symbol or footprint, go to “File” > “New” and select the appropriate editor (Symbol Editor or PCB Library Editor). You can then design your custom component using the available tools and settings.
4. How can I ensure my PCB design meets manufacturing requirements?
To ensure your PCB design meets manufacturing requirements, it’s essential to communicate with your manufacturing partner early in the design process. They can provide you with their specific design guidelines and constraints. Additionally, using Altium Designer’s design rule checking (DRC) feature can help you identify and resolve any potential manufacturing issues.
5. What resources are available for learning more about PCB design with Altium Designer?
Altium provides a wide range of resources for learning PCB design with Altium Designer, including:
- Altium Academy: Online courses and tutorials
- Altium Wiki: Comprehensive documentation and guides
- Altium Forums: Community-driven support and discussions
- Altium YouTube Channel: Video tutorials and webinars
Additionally, many third-party resources, such as blogs, books, and online communities, can provide valuable insights and tips for designing PCBs with Altium Designer.
Conclusion
Designing circuit boards with Altium Designer can be a complex process, but following these 10 easy steps can help you navigate the workflow and create high-quality PCBs. By setting up your project correctly, creating accurate schematics, assigning appropriate footprints, and applying design rules, you can ensure your PCB layout is functional and manufacturable.
Remember to collaborate with your team, conduct thorough design reviews, and communicate with your manufacturing partners throughout the process. With practice and experience, you’ll be able to design increasingly complex and sophisticated PCBs using Altium Designer’s powerful features and tools.
Leave a Reply